Enhancing Inventory Control with QuickBooks
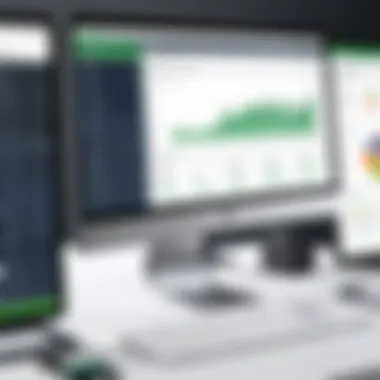
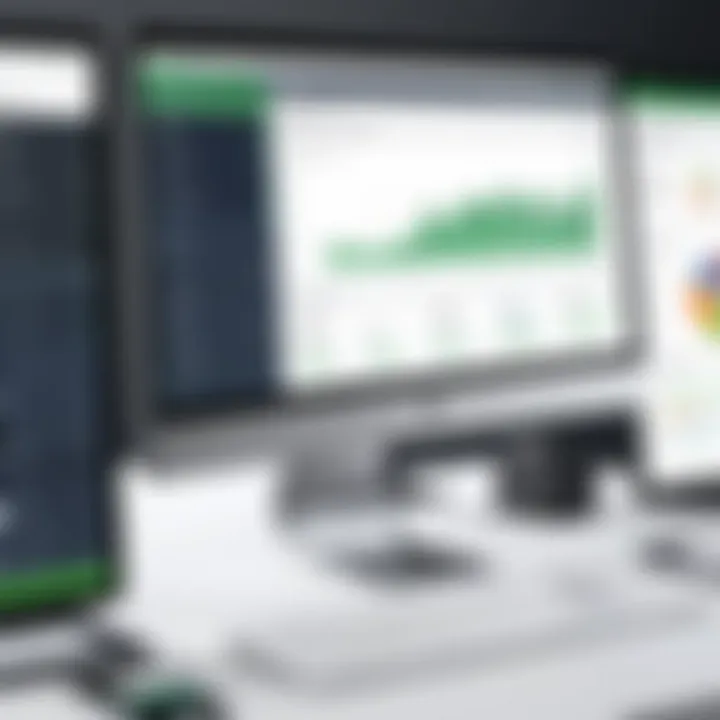
Intro
In today's fast-paced business environment, effective inventory management is essential for success. Many small to medium-sized manufacturing enterprises face challenges in maintaining accurate records and managing stock levels. QuickBooks Manufacturing Software offers solutions tailored to these needs. Understanding its functionalities is crucial for stakeholders aiming to optimize their operations. This article outlines the features, advantages, and limitations of QuickBooks in the context of inventory control for manufacturing businesses.
Features Overview
QuickBooks Manufacturing Software provides an array of functionalities designed specifically for managing inventory efficiently.
Key Functionalities
The software includes essential tools that help businesses track inventory levels, manage orders, and forecast demand. Notable features include:
- Automated Inventory Tracking: Continuous monitoring of stock levels helps prevent shortages or surpluses.
- Order Management: Users can easily create purchase orders and sales orders, simplifying the communication with suppliers and customers.
- Reporting and Analysis: Built-in reporting tools reveal trends and patterns in inventory data, allowing for informed decision-making.
- Barcoding: Integration with barcode scanners enables quick scanning of products during sales and receiving processes.
Integration Capabilities
Integrating QuickBooks with other systems is vital for seamless operations. The software offers capabilities to connect with various applications, such as:
- E-commerce Platforms: QuickBooks can sync with platforms like Shopify or WooCommerce to streamline online sales.
- Shipping Software: Integrations with services like ShipStation facilitate order fulfillment processes efficiently.
- Customer Relationship Management (CRM) Systems: This enhances communication and customer service by keeping track of customer interactions.
Pros and Cons
Identifying the advantages and disadvantages of QuickBooks Manufacturing Software helps businesses make informed decisions.
Advantages
- User-Friendly Interface: The software is designed for ease of use, enabling quick onboarding for employees.
- Cost-Effective: Compared to other manufacturing systems, QuickBooks is often more affordable, particularly for smaller businesses.
- Scalability: It can grow along with the business, accommodating increased inventory and production needs.
Disadvantages
- Limited Advanced Features: Some high-end manufacturing functionalities may be lacking compared to specialized software.
- Customization Restrictions: Users may face limitations if they require extensive customization for unique business processes.
"Understanding inventory management software like QuickBooks is not merely about choosing a system; it is about aligning it with the specific demands of your business."
In summary, QuickBooks Manufacturing Software offers valuable tools for inventory management, making it an attractive option for many businesses. However, decision-makers must carefully evaluate its fit for their unique needs against the backdrop of its limitations.
Foreword to QuickBooks Manufacturing Inventory Management Software
Efficient inventory control is crucial for businesses, especially in the manufacturing sector. As companies grow, the volume and complexity of inventory management tend to increase, causing potential disruptions if not handled appropriately. QuickBooks Manufacturing Inventory Management Software provides a solution that streamlines these processes, enhancing overall operational productivity.
This software plays an important role in optimizing inventory accuracy, reducing excess stock, and ensuring that materials are available when needed. The value of reducing errors in inventory cannot be understated; a small mistake in stock levels can lead to production delays, lost sales, and unsatisfied customers. As manufacturing environments are highly dynamic, having a robust system like QuickBooks becomes essential for maintaining smooth operations.
QuickBooks Manufacturing software is not just about tracking inventory; it offers a range of features tailored to meet the specific needs of manufacturers. From improving order management to setting the stage for insightful reporting, each aspect is designed to provide businesses with a competitive edge. Furthermore, understanding QuickBooks' capabilities ensures that decision-makers can successfully integrate this tool into their existing workflows.
In this section, we will delve deeper into the software solutions offered by QuickBooks. We will also explore specifics related to manufacturing inventory management to give you a comprehensive overview of its effectiveness.
Key Features of QuickBooks Manufacturing Inventory Software
For businesses aiming for efficient inventory management, understanding the key features of QuickBooks Manufacturing Inventory Software is crucial. This software provides manufacturers with the tools necessary to streamline operations, reduce errors, and enhance overall productivity. Key features not only help in managing stock levels but also facilitate improved decision-making. Each aspect of the software is designed to address specific challenges faced by manufacturers today.
Inventory Tracking Capabilities
One of the most significant advantages of QuickBooks Manufacturing Software is its robust inventory tracking capabilities. The software enables businesses to monitor their inventory in real-time. This means users can easily see what products are available, what needs to be reordered, and what is on hand across multiple locations.
QuickBooks allows for managing various inventory items, including raw materials and finished goods. With barcoding functionalities, it minimizes manual entry errors, resulting in more accurate counts and fewer stock discrepancies. Moreover, the software automatically updates inventory levels as sales are made or new stock is received. This feature is critical for preventing stockouts or overstock situations.
Order Management Functionality
Efficient order management is vital for maintaining customer satisfaction. QuickBooks Manufacturing Software includes features that streamline the entire order process. Users can create and manage sales orders, purchase orders, and invoices in one place.
The software tracks orders from initiation to fulfillment. Automated notifications alert staff when orders are placed, ready for shipment, or delayed. Such clarity improves response times and enhances customer service. Additionally, users can assess order history for valuable insights into customer buying patterns, which aids in inventory predictions and stocking decisions.
Reporting and Analytics Tools
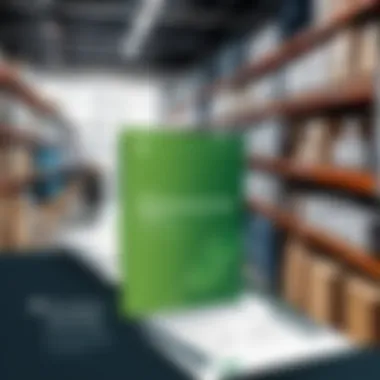
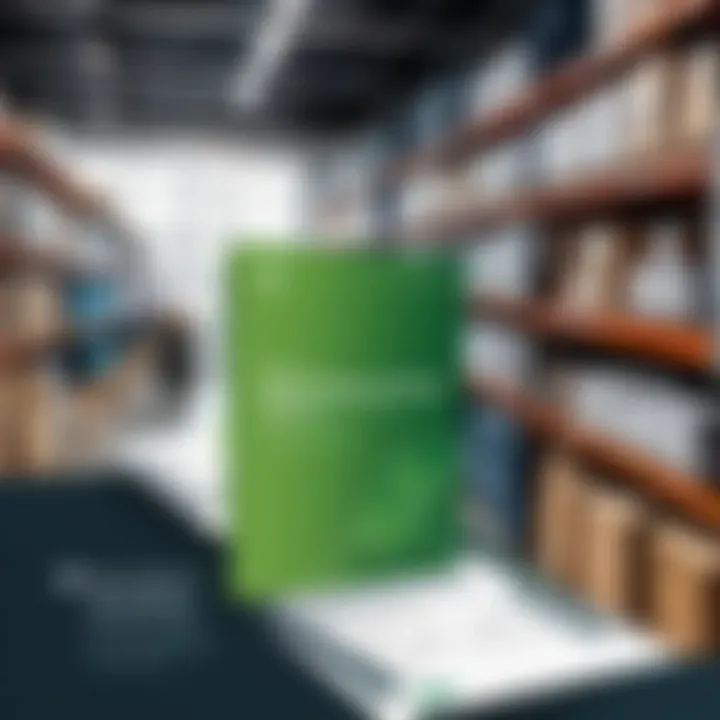
Data is at the heart of effective decision-making. QuickBooks offers powerful reporting and analytics tools that provide insights into inventory performance. Businesses can generate various reports to analyze turnover rates, inventory valuation, and sales trends.
These reports help identify best-selling items and products with slow movement. Armed with this information, businesses can make informed decisions about purchasing and sales strategies. The ability to visualize data through charts and graphs enhances understanding, turning complex information into actionable steps.
Integration with Other Systems
In today’s connected environment, integration capabilities are critical for any software solution. QuickBooks Manufacturing Software can seamlessly integrate with various other systems, such as eCommerce platforms and Customer Relationship Management (CRM) tools.
Such integrations allow for the centralization of data across platforms, leading to improved communication and a unified approach to inventory management. For instance, order information can be automatically shared between the eCommerce site and QuickBooks, eliminating the need for duplicate data entry.
This synergy not only saves time but also enhances accuracy across all systems involved. Manufacturers can thus focus more on core operations rather than on mundane data entry tasks.
"Integration capabilities allow businesses to break data silos, ensuring a smoother operation across multiple platforms."
Understanding these key features of QuickBooks Manufacturing Software provides a solid foundation for any business considering it as a solution for inventory management. The focus on real-time tracking, efficient order management, data analysis, and system integration makes it an essential tool for modern manufacturers.
Benefits of Using QuickBooks for Inventory Management
QuickBooks Manufacturing Software offers numerous advantages that can transform the way businesses handle their inventory. Understanding these benefits is crucial for organizations looking to optimize their operations. Each benefit contributes to a more refined, effective, and streamlined approach to inventory management. Below are the significant points regarding how QuickBooks can elevate a company's inventory practice.
Improved Inventory Accuracy
An enhanced level of accuracy in inventory management is indispensable for any manufacturing business. QuickBooks can significantly reduce the chances of errors that commonly occur in inventory counts.
Using this software, businesses can track inventory in real-time. Inputs are updated automatically when items are sold or produced, ensuring that the inventory records reflect the actual stock levels. This responsiveness is vital for preventing stockouts or overstock situations. Real-time data also empowers companies to make smarter purchasing decisions.
Moreover, the software allows for inventory alerts, which notify users about low stock levels. This feature minimizes the risk of lost sales due to stock shortages, thereby supporting customer satisfaction. Improved accuracy enhances overall operational effectiveness and strengthens the business’s reputation in supply chain management.
Cost Reduction Potential
One of the most compelling reasons to adopt QuickBooks for inventory management is its potential for cost reduction. By maximizing efficiency and minimizing waste, companies can achieve significant savings in various aspects of their operations.
With better inventory management, businesses can pinpoint excess inventory and slow-moving items. This information allows for more informed purchasing decisions, helping to avoid unnecessary costs associated with storing unsold items. QuickBooks also provides insights into pricing trends, which can guide in setting competitive prices and negotiating supplier rates. Ultimately, enhanced control over inventory can result in lowered operational costs.
Enhanced Decision-Making through Data Insights
Leveraging data insights is a key strategy for making informed business decisions. QuickBooks offers robust analytics and reporting tools that generate useful reports on inventory performance. Executives and managers can access performance metrics that influence their strategic choices.
For instance, businesses can examine trends in sales, turnover rates, and inventory levels. Analyzing these metrics enables organizations to plan better for seasonal demands and promotional events. With data in hand, decision-makers can also assess which products are profitable and which might need a different marketing strategy. QuickBooks helps turn numbers into actionable information that drives growth and efficiency.
Streamlined Operations and Efficiency
Efficiency in operations is crucial for maintaining a competitive edge. QuickBooks Manufacturing Software fosters a cohesive workflow throughout the inventory management process. Automation of repetitive tasks, such as invoicing and reordering, streamlines operations, freeing up time for staff to focus on more strategic activities.
Additionally, QuickBooks allows for comprehensive tracking of inventory across multiple locations. This centralized view lets managers obtain a clear understanding of where products reside. As a result, assessing stock locations and fulfilling orders becomes a smoother process, reducing wait times and enhancing service levels. Ultimately, increased efficiency leads to improved productivity and a better bottom line.
Utilizing QuickBooks Manufacturing Software equips businesses with the tools necessary to improve inventory accuracy, reduce costs, and enhance overall efficiency.
Implementation of QuickBooks Manufacturing Software
Implementing QuickBooks Manufacturing Software is a crucial step for businesses eager to streamline their inventory management practices. The right implementation can lead to improved accuracy, efficiency, and overall productivity. It is essential for organizations to consider factors such as preparation, execution, and ongoing support to harness the full potential of the software.
Necessary Preparations Before Implementation
Preparation is key when adopting any new software, especially one as comprehensive as QuickBooks Manufacturing. First, assess the current inventory management system. Identifying strengths and weaknesses helps in setting a clear baseline.
Next, gather input from team members who will use the software. This could include insights on what features would best serve their daily tasks. Engaging users early fosters a sense of ownership that is vital for the overall acceptance of the new system.
Additionally, ensure that your existing hardware and software infrastructure can support QuickBooks Manufacturing Software. Reviewing compatibility saves time during installation.
- Evaluate Current Processes: Analyze existing methods to improve upon them.
- Team Engagement: Involve users in the decision and implementation processes.
- Infrastructure Check: Confirm that your systems meet QuickBooks’s requirements.
Step-by-Step Implementation Guide
Once preparations are in place, the next step is to follow a structured implementation guide. Here’s a straightforward approach:
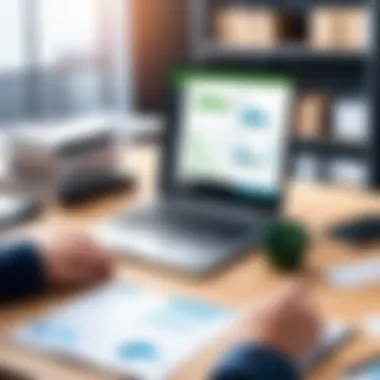
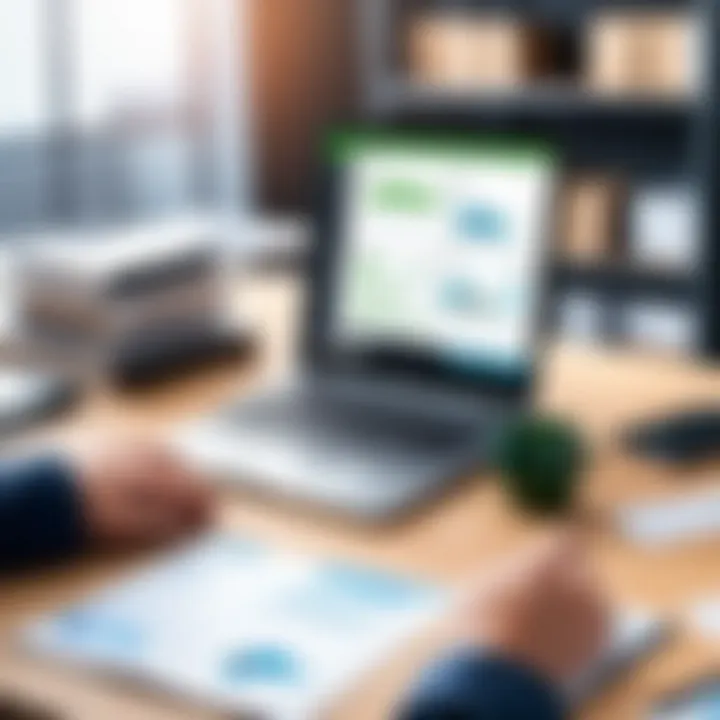
- Initial Setup: Create an account and install the software on your systems. Follow the guided prompts for installation.
- Configuration: Customize the software according to your organization’s needs. Set up user roles and permissions to ensure proper access.
- Data Migration: Import existing data, like inventory lists, supplier information, and customer records. It’s pivotal to validate this data post-migration.
- Test Functionality: Run a few transactions to ensure everything operates as expected. Identify any issues early.
- Feedback Loop: Collect feedback from users and make adjustments as necessary. This ongoing communication will optimize processes.
Training and Support for Users
Training is an integral part of successful implementation. Without adequate training, even the best software can underperform. Therefore, invest time in comprehensive training sessions for all users.
- Structured Training Programs: Create detailed training sessions covering every aspect of QuickBooks Manufacturing.
- Ongoing Support: Establish a helpdesk or support team for ongoing queries. This can be an internal team or guided by QuickBooks specialists.
- Access to Resources: Provide users with access to tutorials, webinars, and forums for self-learning.
"Investing in user training not only ensures a smoother transition but also maximizes the benefits of your new software setup."
Challenges of Using QuickBooks Manufacturing Software
Implementing QuickBooks Manufacturing Software presents some significant challenges that businesses must navigate. Understanding these hurdles is crucial for effective inventory management. Despite the software’s many advantages, without awareness of potential issues, users may face complications that could undermine the intended benefits. This section details common challenges encountered when using QuickBooks and offers insights for overcoming these barriers.
Potential Integration Issues
One of the foremost challenges is integration with existing systems. When businesses utilize multiple platforms for their operations, integrating QuickBooks can become complex. Software incompatibility may lead to data silos, creating inefficiencies that affect overall productivity. Timely updates and accurate data flow are essential for seamless operation, and any disruption can complicate inventory control.
To address these issues, businesses should conduct thorough assessments of their existing systems before implementation. It is beneficial to enlist the support of IT professionals or third-party integration experts. This proactive approach can help identify potential conflicts and establish necessary adjustments in advance.
User Adoption and Resistance
Another challenge lies in user adoption and resistance to change. Staff members used to a different system may find it difficult to adapt to QuickBooks. This resistance can hinder the full use of the software, limiting its effectiveness. Proper change management strategies should be utilized to foster a positive transition.
Training programs play a vital role in this process. They should not solely cover system functionality but also emphasize how QuickBooks can benefit daily tasks. Encouraging user feedback during early stages can also enhance adoption as it promotes a sense of ownership over the new system.
Limitations in Customization
While QuickBooks offers a range of features, its customization options can be limited compared to other advanced systems. Businesses often have unique needs that may not align perfectly with the software's predefined settings. This limitation can lead to frustrations as users seek to customize workflows or reporting tools.
To mitigate this issue, companies should explore the software’s capabilities thoroughly before implementation. Understanding what customizations are possible can prevent unrealistic expectations. In some cases, exploring additional software integrations or add-ons may provide the necessary enhancements.
The efficient use of QuickBooks can significantly streamline operations, but awareness of potential challenges is essential for effective implementation and user satisfaction.
Cost Analysis of QuickBooks Manufacturing Inventory Management
Understanding the cost analysis of QuickBooks Manufacturing Inventory Management is crucial for businesses looking to optimize their operations. This section outlines the pricing structure, compares QuickBooks with its competitors, and emphasizes the return on investment considerations. Through a thoughtful evaluation of these elements, business leaders can make informed decisions about integrating this software into their systems.
Pricing Structure Explained
The pricing of QuickBooks Manufacturing Inventory Management varies based on the features and level of service chosen. QuickBooks offers various plans that cater to different business sizes and needs. Typically, the main plans include Simple Start, Essentials, Plus, and Advanced.
- Simple Start: A basic option for solo users, including essential features for invoicing and tracking income and expenses.
- Essentials: Includes everything in Simple Start plus bill tracking and support for up to three users.
- Plus: Offers inventory tracking and allows for up to five users, making it suited for small to medium-sized businesses.
- Advanced: Designed for larger businesses, it provides extensive features for customization and integration with third-party applications.
Aside from these core plans, there may be additional costs for specific add-ons or services like payroll processing or advanced reporting tools. These considerations are important for businesses planning budgets and assessing the total cost versus expected benefits.
Comparison with Competitors
When evaluating QuickBooks, it is useful to compare it with other inventory management solutions like Sage Intacct, NetSuite, and Fishbowl. Each software offers distinct capabilities, and prices may differ significantly.
- Sage Intacct: Known for its robust accounting features but can be more complex and costly than QuickBooks.
- NetSuite: Offers comprehensive ERP solutions with advanced functionalities, though at a higher price point, often more suited for larger organizations.
- Fishbowl: Specializes in inventory management but may lack some financial features present in QuickBooks.
In making comparisons, businesses should consider their specific needs, including user-friendliness, customer support, and the range of features available. QuickBooks is often recognized for its balance of productivity and cost-efficiency, making it a strong contender for small to medium enterprises.
Return on Investment Consideration
Calculating the return on investment (ROI) for QuickBooks Manufacturing Inventory Management is an essential part of the cost analysis. Businesses should evaluate both tangible and intangible benefits gained from using this software.
Tangible benefits can include:
- Time Savings: Automation of inventory management tasks saves considerable time, allowing employees to focus on productive activities.
- Cost Reduction: Efficient management leads to reduced waste and optimized stock levels, directly impacting the bottom line.
- Error Reduction: Fewer mistakes in inventory tracking improve data accuracy and decrease costly errors.
Intangible benefits might be harder to quantify but are equally important:
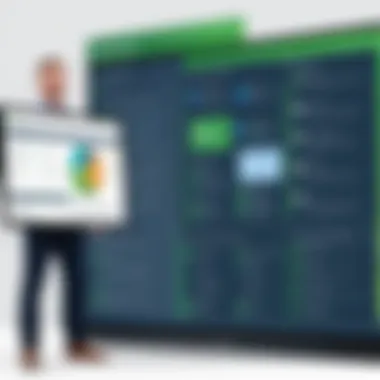
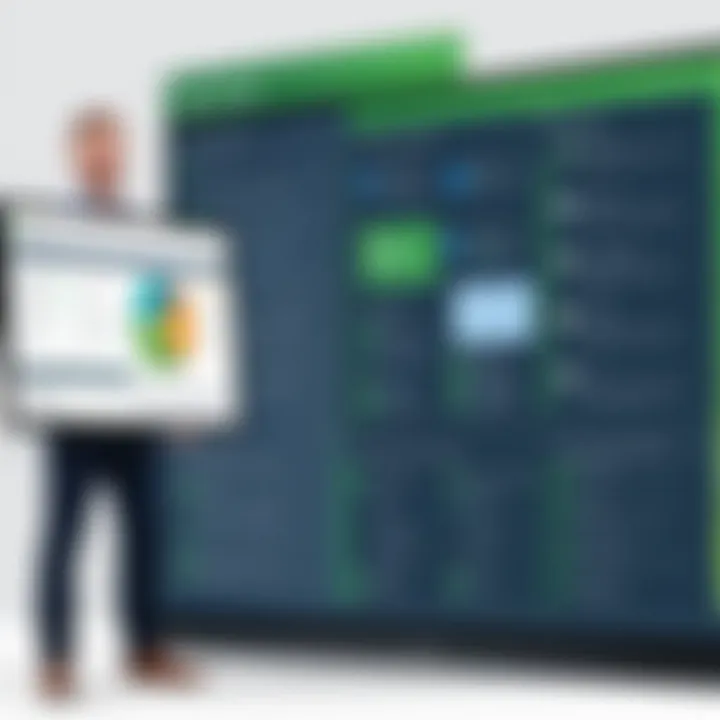
- Improved Decision-Making: With better data insights, managers can make more informed choices.
- Customer Satisfaction: Timely fulfillment and accurate inventory levels enhance customer service, leading to repeat business.
Ultimately, businesses should create a comprehensive ROI analysis that reflects their unique situation. Such analysis will inform investment decisions and help in justifying the costs associated with implementing QuickBooks Manufacturing Inventory Management.
Case Studies of Successful Implementations
Case studies serve as compelling evidence of the effectiveness and adaptability of QuickBooks Manufacturing Software. For decision-makers and IT professionals, these real-world examples offer valuable insights into how businesses have leveraged the software to enhance their inventory management processes. They reveal not just the operational improvements, but also the strategic advantages gained through effective software integration.
The importance of these case studies lies in their ability to demonstrate the practical application of theoretical concepts. By examining successful implementations, businesses can identify best practices, common challenges, and realistic outcomes. Additionally, case studies highlight the versatility of QuickBooks in varying business contexts, from small enterprises to larger operations.
Small Business Success Story
In a notable instance, a small manufacturing company encountered challenges related to inventory inefficiency. Before using QuickBooks, the business relied on manual tracking systems, leading to frequent overstocking and stockouts. This situation not only affected cash flow but also diminished customer satisfaction due to missed orders.
After implementing QuickBooks Manufacturing Software, the company reported significant transformations. The software’s inventory tracking capabilities allowed them to monitor stock levels in real-time, reducing excess inventory by 25%. Moreover, the automated order management features streamlined their procurement process, enabling quicker responses to customer orders.
As a result, the business improved its turnover rate and increased profitability. Financial constraints eased, allowing for reinvestment into the business. This success story underscores the potential of QuickBooks to empower small businesses to refine their operational practices.
Medium-Sized Firm Transformation
A medium-sized manufacturing firm sought to modernize its inventory management practices as it expanded operations. Prior to utilizing QuickBooks, the firm faced hurdles with data silos and ineffective communication between departments. The lack of integrated systems resulted in delays and inaccuracies that hampered production.
Upon adopting QuickBooks Manufacturing Software, the organization achieved a comprehensive overhaul of its inventory processes. The integration capabilities with existing systems enhanced communication across departments. Employees could access unified inventory data, fostering collaboration and informed decision-making. Notably, their production efficiency improved by 30%, directly impacting lead times and customer satisfaction.
Furthermore, the reporting and analytics tools provided actionable insights into inventory trends, guiding the firm’s strategic planning. The ability to analyze data trends facilitated smarter purchasing decisions. By effectively harnessing QuickBooks, the medium-sized firm not only minimized operational disruptions but also positioned itself for future growth in a competitive market.
These case studies exemplify the transformative power of QuickBooks Manufacturing Software. By adopting this tool, businesses can achieve improved inventory control, operational efficiency, and ultimately, greater financial success.
Future Trends in Manufacturing Inventory Management Software
Understanding the future trends in manufacturing inventory management software is critical for businesses aiming to maintain a competitive edge. As technology continues evolving, the capabilities of software platforms like QuickBooks also change. The ability to adapt to these trends ensures that organizations can streamline processes, reduce costs, and enhance productivity. The following sections delve into two significant aspects of this trend: emerging technologies and scalability for future-proofing businesses.
Emerging Technologies Impact
The integration of emerging technologies is reshaping manufacturing inventory management. Concepts such as Artificial Intelligence (AI), the Internet of Things (IoT), and cloud computing are taking center stage. With AI, businesses can predict inventory demands more accurately by analyzing past trends and current market conditions. This predictive analysis helps in minimizing excess stock and avoiding shortages.
IoT adds another layer by allowing devices and machinery to communicate with inventory software. For example, smart sensors can track the amount of raw materials on the production floor in real time, leading to more precise ordering processes.
Cloud computing plays a vital role in accessibility and collaboration. Businesses can access their inventory data from anywhere, enabling real-time updates. This flexibility supports remote work and enhances decision-making, as all stakeholders can view the same information instantaneously.
"Adoption of emerging technologies is not just a trend; it is a necessity for businesses wanting to stay relevant in today's fast-paced market."
Implementing these technologies allows for greater productivity and reduces human error, leading to improved overall efficiency in inventory management.
Scalability and Future-Proofing Businesses
Scalability is crucial in modern business environments. As companies grow, their inventory management needs will likely evolve. QuickBooks manufacturing software is designed with scalability in mind. This allows businesses to expand their operations without needing to overhaul their entire system.
QuickBooks can accommodate increased product lines, more complex supply chains, and a heightened volume of transactions seamlessly. Companies can customize features to suit their growing needs, ensuring they stay agile and responsive to market demands.
Future-proofing goes hand in hand with scalability. Businesses need to consider software solutions that can adapt to industry changes, such as regulatory shifts or new technological advancements. QuickBooks ensures that organizations can update their software without losing historical data or functionality.
Ending and Final Recommendations
In this final section, we reflect on the significance of QuickBooks Manufacturing Software in maintaining efficient inventory control. As examined throughout this article, QuickBooks not only enhances inventory tracking and order management, but it also provides actionable insights that can transform business strategies. For small to medium-sized enterprises, the ability to manage inventory effectively can distinguish between profitability and loss.
Summary of Key Insights
QuickBooks Manufacturing Inventory Management Software stands out due to several critical features that streamline operations:
- Inventory Accuracy: It minimizes stock discrepancies through real-time tracking, ensuring businesses have the right amount of product on hand.
- Cost Efficiency: Leveraging the software leads to reduced holding costs and waste, which directly impacts the bottom line positively.
- Data-Driven Decisions: The integration of reporting tools allows for data analysis that drives informed business strategies.
- Scalability: QuickBooks adapts to growing business needs, making it a long-term investment that adjusts with changes in the market.
This software equips businesses with tools that are essential for navigating today's competitive landscape, ensuring they remain agile and responsive.
Recommendations for Potential Users
For those contemplating the adoption of QuickBooks Manufacturing Software, consider the following recommendations:
- Assess Your Needs: Evaluate your current inventory management challenges. Identify specific areas where QuickBooks can add value.
- Utilize Training Resources: Take advantage of training sessions offered through QuickBooks to maximize the utilization of its features. Familiarity will enhance efficiency.
- Integrate with Existing Systems: Ensure that the software can work harmoniously with other systems and platforms in place within your organization.
- Regularly Review Performance: By routinely assessing how your inventory management metrics change, you can continuously optimize your processes and software utilization.
- Stay Updated: Keeping abreast of software updates and industry trends makes certain that you're getting the most from your investment.
Implementing QuickBooks can lead to significant operational improvements. Thus, carefully weighing these recommendations can assist in making an informed decision.