Enterprise Process Management: Enhancing Efficiency
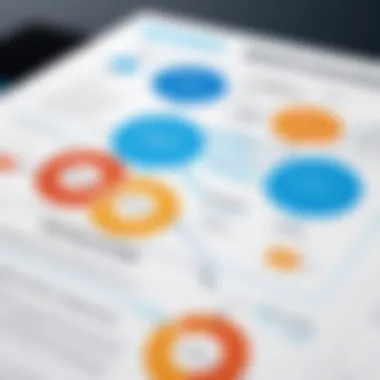
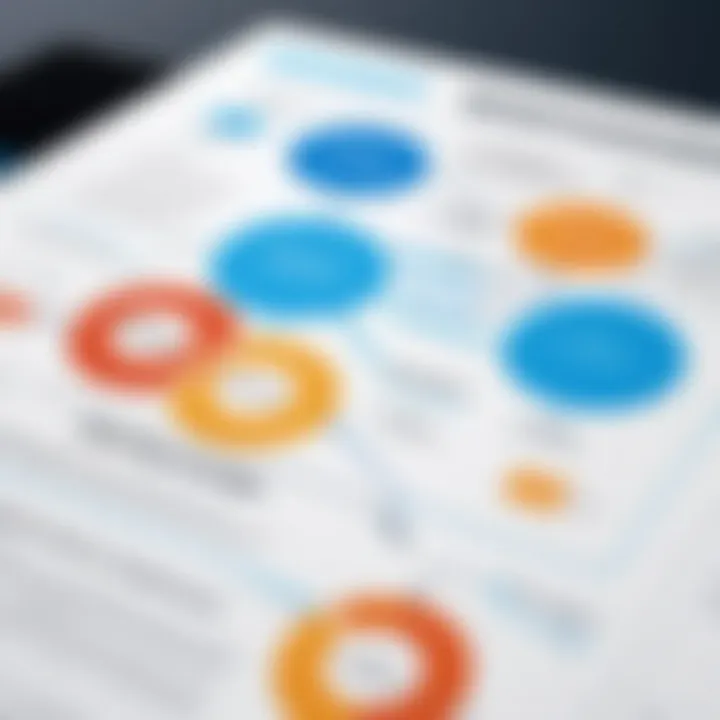
Intro
In today's fast-paced and competitive business landscape, the ability to efficiently manage processes can make or break an organization. Enterprise process management goes beyond simple task coordination; it covers a range of strategies, methodologies, and technological tools crafted to streamline operations and boost productivity. This section lays the groundwork for understanding how these components fit together, setting the stage for a deeper examination of relevant concepts and practices.
While it may sound like corporate jargon, the essence of effective enterprise process management lies in its practicality. It's about aligning resources, minimizing redundancies, and ensuring that every cog in the wheel is turning smoothly. When companies implement a structured approach to managing their processes, they not only enhance operational efficiency but also set themselves up for long-term success.
Beneath this overarching objective, enterprise process management encompasses various characteristics essential for thriving in the digital age. In the following sections, we will dissect these features, examine both pros and cons of implementing such frameworks, and explore how technology emerges as a critical player in this domain.
Understanding Enterprise Process Management
Enterprise Process Management (EPM) stands as a crucial pillar in achieving organizational efficiency and effectiveness. In a world where business environments continuously evolve, having a solid grasp of how EPM works enables organizations to not just survive but thrive. By effectively managing processes, businesses can streamline operations, reduce waste, enhance customer satisfaction, and ultimately bolster their bottom line.
Defining Enterprise Process Management
Enterprise Process Management involves the systematic approach to managing and optimizing an organization's processes. It consists of documenting, analyzing, and improving business processes to ensure they support the organization’s goals. EPM encompasses a range of methodologies and practices that aim to create a culture of continuous improvement. In simple terms, it’s about getting the right things done in the right way, which often includes looking closely at workflows, performance metrics, and employee engagement.
Imagine a ship navigating through stormy seas. Without a clear map or processes to follow, it risks getting lost or capsizing. Similarly, organizations rely on EPM to chart their course towards greater growth and stability.
Historical Overview
Tracing the roots of Enterprise Process Management may surprise some. The foundations of process management can be seen in early production methods during the Industrial Revolution. Fast forward through time, and you'll see figures like Frederick Taylor, known for his work on Scientific Management, who emphasized optimizing work processes for increased productivity.
In recent decades, the advent of technology has shifted how EPM is perceived and practiced. With tools like software analytics and automation technology, the methods of managing processes have transformed significantly. No longer are we just looking at manual processes. Today, organizations are blending traditional methodologies with modern technology to create dynamic, responsive systems.
Importance of Process Management
The significance of process management can’t be overstated. Effective process management leads to several benefits, including:
- Operational Efficiency: Streamlined processes reduce time and resources spent on activities that do not add value.
- Enhanced Agility: Organizations can swiftly adapt to changes in the market, regulations, or technologies.
- Improved Quality: Structured processes lead to consistent output quality, minimizing errors and rework.
- Employee Satisfaction: By improving workflows, employees often find their jobs more manageable and rewarding.
Additionally, process management provides a holistic view of organizational performance. By having clear processes documented, it becomes easier to identify bottlenecks, optimize resources, and set clear benchmarks for success.
"In today’s hyper-competitive business landscape, those who manage processes effectively are the ones who succeed."
Grasping Understanding Enterprise Process Management is more than a formal exercise; it’s about creating lasting change that promotes efficiency, qualities that can offer organizations a competitive edge. Understanding these fundamentals sets the stage for delving deeper into the key components, methodologies, and technological impacts that define EPM today.
Key Components of Enterprise Process Management
In the realm of enterprise process management, understanding and leveraging key components can make a world of difference in how organizations streamline operations and enhance efficiency. As businesses navigate an increasingly competitive landscape, these components serve as the backbone for effective process management. Properly grasping each element becomes crucial for any decision-maker aiming to refine their business's processes.
Process Mapping
Process mapping is the art of visually laying out the steps involved in any business function. By creating a roadmap, organizations can identify inefficiencies and redundancies that might not be apparent in a verbal description. This method involves utilizing tools like flowcharts or SIPOC (Suppliers, Inputs, Process, Outputs, Customers) diagrams to illustrate workflows.
The benefits are significant. As teams visualize their processes, comprehension deepens, and alignment improves across departments. A clear mapping can facilitate smoother communication and make training new employees more straightforward. Oftentimes, it becomes a vital starting point for discussions about optimization. Without this step, it’s like trying to navigate a new city without a map; one can easily get lost.
Process Analysis
Once the mapping of processes is laid out, it’s imperative to delve into process analysis. This involves scrutinizing procedures to determine how they can be refined. Analysts often employ various methods, like root cause analysis or value stream mapping, to dissect inefficiencies.
During this phase, organizations should consider critical performance indicators to assess the process effectiveness. Are there bottlenecks? Is there unnecessary complexity? Are resources being squandered? When organizations dig into these questions, they often uncover the "why" behind poor performance that may have been overlooked.
Process Optimization
The ultimate goal following analysis is optimization. Here, organizations take the findings from the analysis and implement strategic changes to improve performance. This may involve reengineering workflows, automating repetitive tasks, or reallocating resources where they are truly needed.
Any adjustments should be measured against previously established benchmarks to gauge success. In this context, it is essential to be open to continuous improvement. The process doesn’t end with optimization. Instead, it should create a culture of excellence where teams are always looking for ways to enhance the existing processes.
Process Monitoring
Last but not least, the importance of process monitoring cannot be stressed enough. For optimization efforts to yield lasting results, organizations must have mechanisms in place to continuously assess performance. This involves setting up KPIs (Key Performance Indicators) and dashboards that provide real-time data about process efficiency.
By closely monitoring outcomes, businesses can swiftly detect deviations from established standards and make necessary adjustments before issues escalate. In many scenarios, continuous monitoring acts like a safety net, ensuring that processes remain aligned with organizational goals.
"In the digital world, the brands that adapt tend to succeed, but it’s those that continuously improve their processes that thrive."
Epilogue
In summary, the key components of enterprise process management—process mapping, analysis, optimization, and monitoring—intertwine to build a robust framework for operational success. With an understanding of these elements, professionals can look beyond mere tactical changes and cultivate a sustainable environment of continuous improvement. Embracing this comprehensive approach will ultimately lay the groundwork for superior organizational performance.
Methodologies in Process Management
When diving into the world of enterprise process management, understanding methodologies becomes crucial. These structured approaches aid organizations in streamlining operations, reducing waste, and enhancing overall performance. Methodologies offer frameworks that guide teams through the intricacies of refining processes, ensuring consistent results. This section dissects three predominant methodologies: Lean Management, Six Sigma, and Agile Practices, each bringing unique strengths to the table.
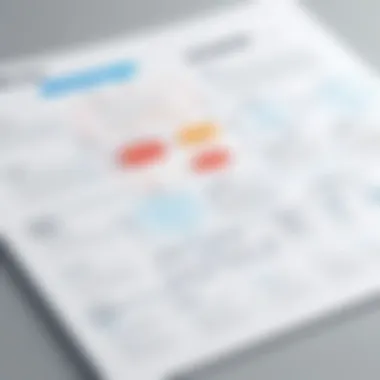
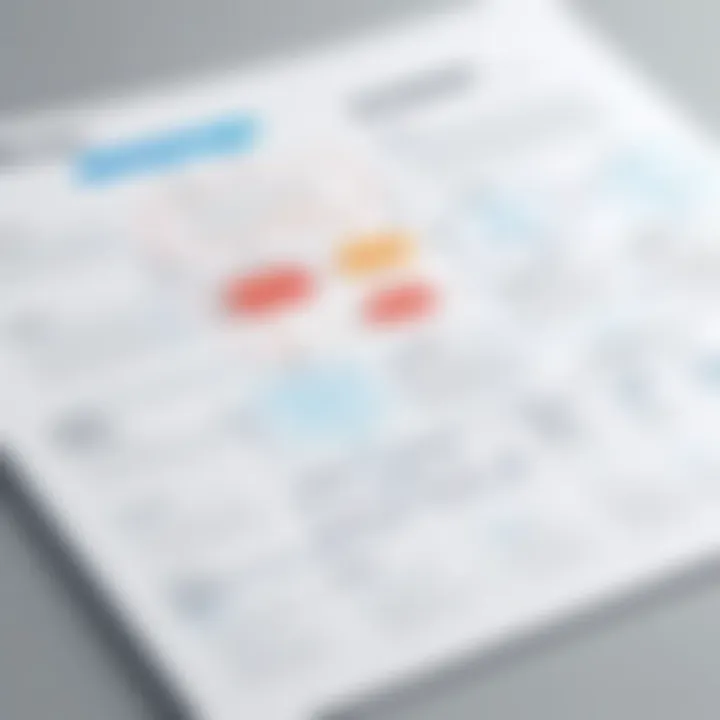
Lean Management
Lean Management emphasizes optimizing value by minimizing waste within an organization. Every activity that does not add value to the customer is deemed wasteful and is targeted for elimination. The origin of this methodology traces back to Toyota's production system, where the focus was on efficient workflows and quality. Its core principles include:
- Value Identification: Recognizing what specifically brings value to the customer.
- Value Stream Mapping: Illustrating the current process workflow to find inefficiencies.
- Creating Flow: Ensuring that each stage of production seamlessly moves to the next without interruption.
- Establishing Pull: Only producing what is necessary when it is necessary to avoid overproduction.
- Pursuing Perfection: A continuous effort to improve processes endlessly.
Implementing Lean Management requires a cultural shift within the organization. It demands that everyone, from top-level executives to frontline workers, embrace the mindset that any form of waste is unacceptable. Furthermore, this methodology fosters a collaborative environment where employee insights are valued.
Six Sigma
Six Sigma stands as a robust method primarily aimed at process improvement and quality management. It utilizes data-driven techniques and tools to eliminate defects in any process, striving for near perfection. Six Sigma projects typically follow the DMAIC framework, which stands for:
- Define: Clearly outline the problem or process improvement goals.
- Measure: Collect data to understand current process performance.
- Analyze: Identify the reasons for defects and weaknesses in the current process.
- Improve: Develop solutions, implement changes, and validate results.
- Control: Maintain improvements and ensure consistent performance.
Incorporating Six Sigma can be highly beneficial for organizations aiming to enhance quality and efficiency. It compels a meticulous examination of processes, leading to significant cost savings, increased customer satisfaction, and heightened market competitiveness. However, it’s important to note that Six Sigma requires trained professionals, such as Green Belts and Black Belts, to effectively lead projects, which can be resource-intensive.
Agile Practices
Agile Practices, often associated with software development, introduce a more adaptive and iterative approach to project management. Unlike traditional methodologies that follow a linear path, Agile focuses on flexibility and responsiveness to change. The Principles of Agile include:
- Customer Collaboration: Engaging with customers throughout the project life cycle to capture requirements that may evolve.
- Embracing Change: Accepting that changes can occur at any stage of the process, leading to better final results.
- Delivering Incrementally: Breaking down projects into smaller, manageable units allows for quicker feedback and adjustments.
- Self-Organizing Teams: Empowering teams to manage their work without excessive oversight fosters creativity and ownership.
The implementation of Agile practices can significantly boost the ability of organizations to respond to market changes swiftly. This is especially pertinent in industries where customer preferences can shift rapidly. However, transitioning to an Agile framework necessitates a cultural shift, where accountability and adaptability become the organization's backbone.
"The primary goal of every methodology is to cater to the dynamic nature of businesses, ensuring sustained growth and adaptation."
In summary, integrating methodologies such as Lean, Six Sigma, and Agile can empower organizations to develop a recipe for success that caters to their specific needs. Understanding the particulars of each approach enables businesses to refine their strategies better, ultimately driving them towards achieving their objectives in process management.
Technology's Role in Enterprise Process Management
In today’s fast-paced world, the role of technology in enterprise process management cannot be overstated. As organizations aim to streamline their operations and enhance efficiency, technology offers powerful tools that transform how processes are conducted. From automating mundane tasks to analyzing vast amounts of data, the integration of technology is fundamental in driving process improvement and innovation. Let’s dive deeper into specific technological elements that play a pivotal role in enterprise process management.
Automation Tools
Automation tools are game-changers in the realm of enterprise process management. They help eliminate redundant tasks, which can save both time and resources. By automating processes such as data entry, invoicing, or report generation, organizations can focus on higher-level strategic initiatives. For example, tools like Zapier or UiPath allow companies to create workflows that automatically transfer information between applications without human intervention.
Benefits of Automation Tools:
- Increased Efficiency: With less manual input, processes are completed faster and more accurately.
- Cost Savings: Eliminating repetitive tasks can significantly decrease operational costs.
- Enhanced Consistency: Automation minimizes errors, ensuring that tasks are performed uniformly every time.
However, integrating these tools requires careful consideration of the current systems and processes. Not all tasks are suitable for automation, and organizations need to thoughtfully assess which processes would benefit the most from this approach.
Software Solutions
When we talk about software solutions in enterprise process management, we refer to a wide range of applications designed to facilitate and optimize business processes. From enterprise resource planning (ERP) systems to customer relationship management (CRM) platforms, software solutions play a vital role in organizing and managing different aspects of an organization’s operations.
For instance, software like Salesforce or SAP helps in centralizing information, allowing for better access and manipulation of data across departments. Employees can share insights in real time, leading to better collaboration and decision-making.
Key Considerations when Choosing Software Solutions:
- Scalability: Will the software adapt as the organization grows?
- User-Friendliness: Is the software easy to use for all employees?
- Integration Capabilities: Can it work with existing systems seamlessly?
These considerations are essential, as the wrong choice can lead to wasted resources and decreased productivity.
Data Analytics
Data analytics serves as the backbone for informed decision-making within enterprise process management. In a world overflowing with information, organizations leveraging data analytics can uncover trends, patterns, and insights that inform future strategies. Behavioral data from customers, operational data from processes, and financial data are all ripe for analysis and can drive success.
Powerful analytics tools, such as Tableau or Google Analytics, offer visualization capabilities that turn raw data into understandable insights. This allows decision-makers to grasp complex information quickly and act accordingly.
Benefits of Data Analytics in Process Management:
- Informed Decision-Making: With data-driven insights, strategies are based on solid evidence rather than guesswork.
- Continuous Improvement: Analytics can highlight inefficiencies in current processes, leading to targeted improvements.
- Risk Mitigation: By understanding past trends, organizations can anticipate and mitigate potential challenges more effectively.
Integrating data analytics into enterprise processes not only provides clarity but also fosters a proactive approach to management.
In summary, technology's contribution to enterprise process management is significant and multifaceted. By embracing automation tools, leveraging software solutions, and harnessing data analytics, organizations can ensure they remain competitive in an ever-evolving landscape.
The Implementation Process
Establishing effective enterprise process management relies heavily on a well-thought-out implementation process. It is akin to laying the foundation of a house — without a solid base, everything that follows can be shaky at best. The implementation process encompasses various critical aspects: assessing needs, engaging stakeholders, and formulating change management strategies. Each of these elements plays a vital role in ensuring that the enterprise’s objectives are met while minimizing disruption to day-to-day operations.
A well-executed implementation strategy directly correlates with the efficiency and effectiveness of process management practices in an organization. By aligning processes to meet both employee and organizational needs, companies not only enhance their productivity but also foster a culture of continuous improvement.
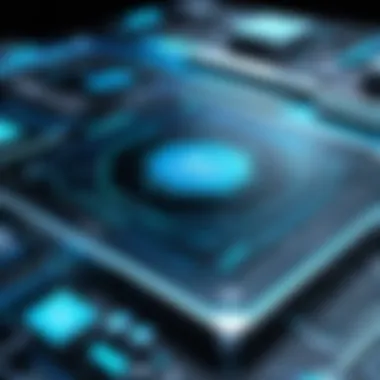
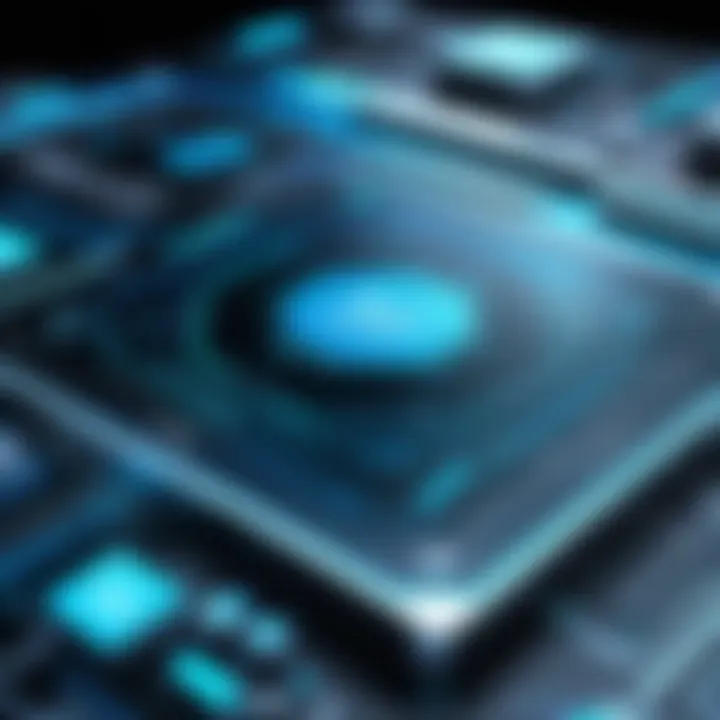
Assessing Needs
The first step in the implementation process is assessing the needs of the organization. This involves a careful examination of the current processes to identify gaps and weaknesses. It’s about understanding what works and what doesn’t.
To get a clearer picture, organizations can utilize various techniques such as:
- Interviews: Gathering insights from employees at different levels can reveal critical pain points that management might overlook.
- Surveys: These can capture quantitative data on employee satisfaction regarding existing processes.
- Process Audits: A thorough audit can uncover inefficiencies and help prioritize areas needing immediate attention.
In this phase, understanding the specific requirements of different departments can facilitate targeted enhancements, leading to greater overall effectiveness.
Stakeholder Engagement
Once needs have been assessed, the next step is stakeholder engagement. This is where collaboration comes into play, creating a well-rounded approach to change.
Engaging stakeholders involves:
- Identifying Key Stakeholders: Recognizing who has a stake in the process changes — be it upper management, department heads, or frontline employees.
- Communicating Effectively: Clear communication about the objectives, benefits, and expectations of the changes keeps everyone informed and involved.
- Creating Feedback Channels: Establishing avenues for stakeholders to voice concerns or suggestions encourages ownership and buy-in, which is crucial for successful implementation.
By involving stakeholders early in the process, their insights can lead to more robust solutions, and it reduces the likelihood of resistance once changes are rolled out.
Change Management Strategies
Finally, after needs have been assessed and stakeholders have been engaged, it’s time to plan and implement change management strategies. Change is often met with resistance, which is why having a structured approach is essential.
Some effective strategies may include:
- Training and Development: Offering targeted training sessions can equip employees with the skills they need to adapt to new processes.
- Pilot Programs: Implementing changes on a small scale can help gauge effectiveness before a full rollout.
- Incentives: Encouraging participation in the new processes through incentives can motivate employees to adapt.
Implementing change management strategies is about creating a smooth transition, preventing disruption, and ensuring that the benefits of process management are realized fully.
"Effective implementation is not just about following a plan; it’s about making sure every person involved is on board and informed."
Challenges in Enterprise Process Management
Enterprise Process Management faces numerous hurdles, as organizations strive to streamline operations effectively. Addressing these challenges is crucial. Understanding resistance to change, the need for seamless system integration, and the growing importance of data security all play a significant role in shaping how organizations approach process management.
Resistance to Change
Change is hard, and human nature does not always favor stepping out of comfort zones. Resistance to change can stem from various factors including fear of the unknown, attachment to current processes, or lack of understanding about the benefits of new practices. Staff may worry that new systems could jeopardize their jobs, thereby leading to a culture of mistrust.
Engaging employees early in the process is vital. Involving them in discussions about changes and actively addressing their concerns helps build a more positive attitude towards transformation. Change management strategies, such as clear communication about the reasons behind shifts and highlighting the anticipated benefits, can also ease the transition. In essence, if employees feel informed and involved, they are less likely to resist change.
Integration of Systems
In today's fast-paced environment, businesses often rely on diverse software and systems. However, integrating these disparate systems can prove complex and cumbersome. A lack of interoperability can result in data silos, inefficient workflows, and decreased productivity. Moreover, inconsistencies in data across systems can lead to errors that ultimately impact decision-making.
To overcome this, businesses must prioritize the harmonization of their systems. Investments might be needed in middleware or API solutions that facilitate communication between different applications. This step not only streamlines operations but also enhances the accuracy of data. So, a well-thought-out integration plan plays a crucial role in process effectiveness.
Data Security Issues
As organizations digitalize, the landscape of data security becomes increasingly urgent. With the heightened reliance on digital systems for process management, risks such as data breaches and cyberattacks have escalated. Firms handling sensitive customer and internal data must prioritize robust security measures to safeguard against these threats, which can result in severe financial and reputational damage.
Implementing strict protocols around data access and encrypting sensitive information can serve as foundational steps. Regular audits and assessments help ensure that security measures remain effective and up-to-date. Moreover, fostering a culture of security awareness among employees ensures everyone plays their part in protecting data assets.
Understanding these challenges can help organizations develop informed strategies that enhance the effectiveness of enterprise process management.
"Resistance to change isn't just a hurdle. It’s a chance to build stronger processes by understanding and addressing the root causes of the hesitance."
Measuring Success in Process Management
Measuring success in process management isn’t just about counting beans. It’s about really getting into the weeds of how effective your processes are and what impact they have on the overall performance of your organization. If you can't measure it, you can't improve it—they don't call it the measurement mantra for nothing. By establishing solid metrics, companies can pinpoint areas where they excel or, conversely, where they're stumbling over themselves. Let's unpack a couple of essential elements that make measuring success a golden ticket in enterprise process management.
Key Performance Indicators
Key performance indicators, or KPIs, are the yardsticks that organizations use to gauge how well they're doing. Think of KPIs as the dashboard lights on your car; if something’s flashing red, it’s time to take a closer look.
Consider the following aspects when crafting KPIs for your process management endeavors:
- Alignment with Objectives: KPIs must reflect the organization’s goals. If you’re aiming to improve customer satisfaction, a related KPI could be the average response time to customer inquiries.
- Quantifiable Metrics: Use metrics that can be tracked and quantified. Numbers don't lie. For example, measuring the time taken to resolve issues can provide clarity.
- Relevance: Ensure that the indicators are relevant to the processes you're monitoring. If you’re focusing on sales processes, tracking website traffic might not hit the mark as a direct indicator of success.
- Comparative Analysis: Evaluate performance over time or against industry benchmarks. This helps organizations to understand where they stand in the grand scheme of things. For instance, an increase in throughput alongside a decrease in errors signals positive performance.
In summary, KPIs nourishe the roots of process management visibility. When implemented correctly, they serve as a beacon, guiding decisions and improvements throughout the organization.
Feedback Mechanisms
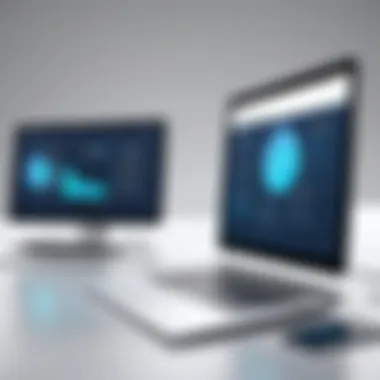
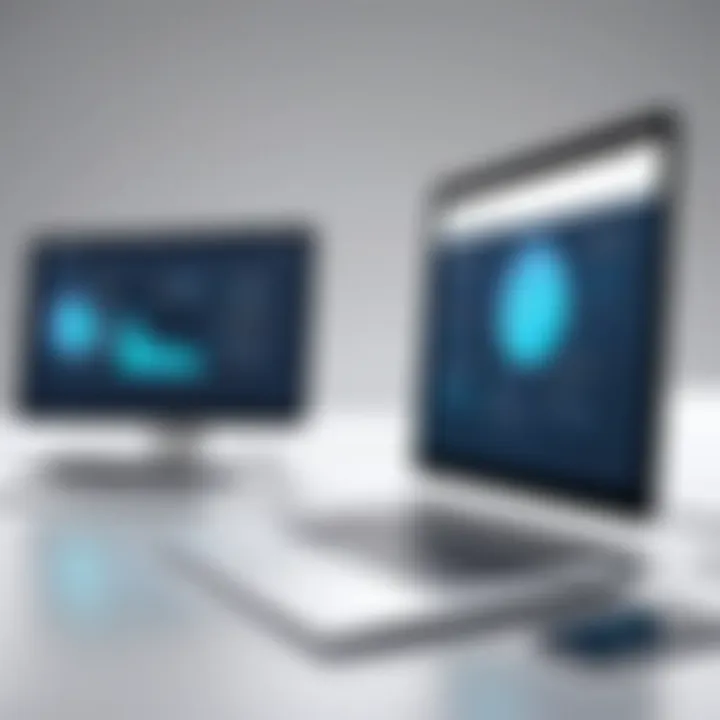
Feedback mechanisms are the ears and eyes of any process management initiative. Without feedback, organizations operate in a void. It’s crucial to establish pathways to gather insights from stakeholders who are affected by or engaged in these processes.
Here’s why feedback matters:
- Continuous Improvement: Feedback fuels the engine of continuous improvement. It's about recognizing when something is off and adjusting before it becomes a bigger issue.
- Engagement and Involvement: Involving team members in the feedback loop encourages buy-in and creates champions for process changes. People like to feel heard; it makes all the difference.
- Identifying Unseen Issues: Front-line employees often identify challenges that management may not even notice. Through regular check-ins or surveys, organizations can unearth these hidden hurdles.
To set up an effective feedback mechanism, consider the following:
- Surveys and Questionnaires: Use these tools to gather structured responses. Keep it brief but insightful to encourage participation.
- Regular Meetings: Schedule frequent discussions for open forums. This informal dialogue can unveil valuable perspectives.
- Technology Utilization: Deploy tools like Slack or Microsoft Teams for quick feedback collection. Even simple emojis can gauge sentiments in real-time, making feedback both accessible and immediate.
"The best feedback is a two-way street; it goes both ways and fosters genuine dialogue."
Employing these feedback mechanisms aids organizations in not just assessing current processes but also in shaping future ones, ensuring adaptability in a constantly changing business landscape.
Case Studies and Real-World Applications
Enterprise process management isn't just a theoretical framework; it’s the engine driving real success in organizations worldwide. Case studies and real-world applications offer valuable insights into how concepts translate into action and yield tangible results. By examining published examples of successes and some failures, professionals can better gauge the effectiveness of various strategies, recognize potential pitfalls, and identify best practices in process management.
Successful Implementations
Successful implementations of process management often highlight the importance of aligning processes with organizational goals. Take, for instance, the case of Toyota Motor Corporation. Their famous Toyota Production System isn't merely a production model; it’s a comprehensive approach to process management that encapsulates lean principles. By focusing on efficiency and waste reduction, Toyota has created a robust production system that is replicated across industries.
A few key points emerge from Toyota's successful approach:
- Focus on Continuous Improvement: This philosophy, known as "Kaizen," involves every employee in the quest for incremental improvements, fostering a culture of innovation.
- Customer-Centric Processes: Every initiative is crafted around customer needs, ensuring higher satisfaction and loyalty.
- Robust Training Programs: Employees are equipped with the skills necessary to identify inefficiencies and implement improvements.
Such efforts have not only positioned Toyota as an industry leader but have also set benchmarks that companies globally aspire to. By investing in process management, they’ve secured their competitive edge, illustrating that tailored solutions can yield impressive outcomes.
Lessons Learned from Failures
On the flip side, analyzing failures in the realm of enterprise process management is equally enlightening. The case of Blockbuster serves as a stark reminder of the need for timely adaptation. At its peak, Blockbuster Dominated the movie rental industry, but as digital streaming gained momentum, the company failed to pivot its operations effectively.
Several lessons can be extracted from Blockbuster's challenges:
- Neglecting Technology Trends: Ignoring the rise of digital streaming hurt their revenue and relevance in a competitive market.
- Lack of Flexible Process Management: Rigid processes didn’t allow for rapid adjustment, showing a crucial need for flexibility in enterprise processes to respond to market shifts.
- Inadequate Market Research: Blockbuster's leadership overlooked significant consumer behavior changes, indicating a lack of proactive analysis in their process management efforts.
Reflecting on these failures can help organizations understand that not only the strategies but the adaptability of those strategies plays a crucial role in successful process management.
"The path of success is paved with missteps and learning curves. Embrace it to navigate future challenges effectively."
In summary, the exploration of both successful implementations and hard-learned lessons forms a fundamental part of enterprise process management. By recognizing the successes and failures of others, managers can refine their approach and lead their organizations more effectively in adapting to a constantly evolving business landscape.
Future Trends in Enterprise Process Management
The landscape of enterprise process management (EPM) is evolving continuously, driven by advancements in technology and shifts in workplace dynamics. Identifying these trends isn't just a passing interest; it offers valuable insights into how organizations can remain competitive while adapting to the demands of a fast-paced market. Understanding these trends helps organizations to anticipate challenges and seize opportunities that arise amidst change. Here are the main components to consider:
Artificial Intelligence Integration
Artificial Intelligence (AI) has emerged as a powerhouse in the realm of process management. The potency of AI helps organizations sort through enormous amounts of data swiftly and accurately, providing insights that human analysis might miss. For instance, NLP (Natural Language Processing) powers chatbots that can handle customer queries efficiently, freeing up teams for more complex tasks.
Moreover, machine learning algorithms can continually improve processes based on the data they analyze. Imagine a manufacturing facility that uses AI to predict machine failures before they happen. This not only reduces downtime but enhances overall operational efficiency.
- Benefits of AI integration:
- Automates repetitive tasks, reducing errors.
- Offers real-time data analysis for better decision-making.
- Facilitates predictive maintenance and quality control.
However, the road to AI adoption isn’t all sunshine and roses. Concerns about data privacy, potential biases in algorithms, and the need for upskilling workers are critical considerations. Consequently, businesses must strategize how they can integrate AI responsibly while ensuring compliance with regulations.
Remote Work Considerations
The rise of remote work has flipped traditional process management on its head. No longer are teams confined to office spaces, and this shift demands new strategies to maintain productivity and ensure processes run smoothly.
Organizations are learning to leverage technology like cloud applications and project management tools to support remote collaboration. It’s about creating a culture of accountability and engagement, even when teams aren't physically together.
To capitalize on this trend, firms might consider:
- Implementing robust communication tools to foster collaboration.
- Providing flexibility in work schedules to enhance employee satisfaction and work-life balance.
- Regularly assessing the effectiveness of remote processes to identify areas for improvement.
Navigating remote work also comes with its challenges. Managers need to balance autonomy with oversight to ensure workers are performing effectively without micromanaging them.
Sustainability Practices
Sustainability is no longer optional; it’s become a key consideration in enterprise process management. Companies are under increasing pressure from stakeholders to adopt practices that are not only profitable but also socially and environmentally responsible.
Integrating sustainable practices into EPM helps organizations reduce waste, lower costs, and improve their brand image. Consider a logistics company that optimizes its routes to decrease fuel consumption and carbon emissions. This is not only cost-effective but also positions the company as a leader in sustainability.
- Example initiatives:
- Adopting lean practices to eliminate waste.
- Using data analytics to monitor resource consumption.
- Collaborating with suppliers who prioritize sustainable practices.
While integrating sustainability into processes may seem daunting and resource-intensive upfront, the long-term benefits often outweigh initial costs. Ultimately, a commitment to sustainability can enhance customer loyalty and pave the way for future growth.