Exploring Work Order Maintenance Software Benefits
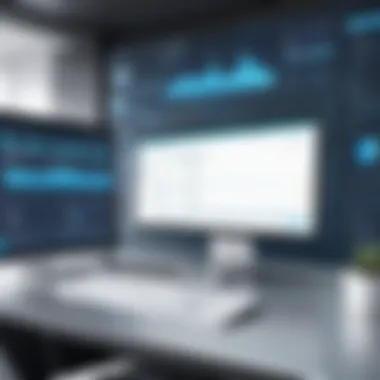
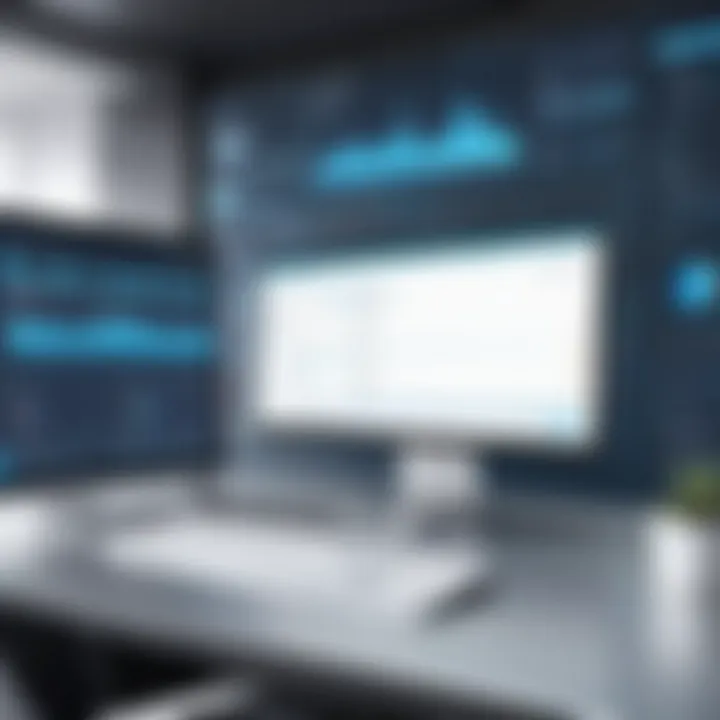
Intro
Work order maintenance software has increasingly cemented itself as an integral component in the operational arsenal of many organizations. It serves as the backbone of maintenance management, streamlining workflows, tracking assets, and facilitating communication across teams. As businesses grow, the complexity of managing maintenance activities often follows suit. This growth paves the way to potential challenges, which is where effective software solutions come into play.
In today's fast-paced environment, the intersection of technology and maintenance management is more relevant than ever. Organizations are constantly seeking ways to minimize downtime, optimize resource allocation, and enhance overall productivity. Therefore, delving into the features, advantages, and potential limitations of work order maintenance software is not just useful—it's essential for businesses aiming to stay ahead in a competitive landscape.
Understanding Work Order Maintenance Software
Work order maintenance software plays a crucial role in modern organizations, bringing structure and efficiency to the often chaotic world of task management and operational upkeep. By automating many of the manual processes associated with maintenance tasks, this software not only helps streamline operations but also ensures that resources are allocated compitently. The rise of such tools reflects a shift in how businesses prioritize their operations and maintenance strategies, especially in industries like manufacturing, facilities management, and service delivery.
Definition and Purpose
At its core, work order maintenance software is designed to facilitate the creation, tracking, and completion of maintenance tasks. It serves multiple stakeholders: from facility managers who need insight into workflow efficiency to technicians who rely on clear communication for successful task execution. This kind of software centralizes information, allowing all relevant parties to see job status, resource availability, and priority levels at a glance. In a nutshell, the purpose of work order maintenance software is to enhance workflow efficiency, minimize downtime, and promote proactive maintenance strategies.
Some key features that this software typically includes are:
- Task Assignment: Clearly assign tasks to individuals or teams, enabling accountability.
- Progress Tracking: Keep tabs on the status of tasks in real-time.
- Reporting Modules: Generate reports to evaluate performance metrics and identify areas for improvement.
In essence, such tools help organizations become more agile, be it in a manufacturing setting or managing a complex facility.
Historical Context and Evolution
The roots of work order maintenance software stretch back several decades, evolving from basic paper-based systems to the sophisticated digital solutions we see today. Early systems relied heavily on manual logging and paperwork, which were prone to errors and inefficiencies. The paper trail could easily become cluttered, leading to fragmented communications between various departments.
As technology advanced, organizations began to adopt computerized maintenance management systems (CMMS). These systems started integrating databases to handle work orders better and track assets. Over time, the software began to incorporate features such as mobile accessibility, allowing technicians to receive updates and input information while on the go.
"Early adopters of maintenance software noted significant time savings and improved communication, setting the trend for broader implementation across different sectors."
Now, work order maintenance software includes cutting-edge technologies such as cloud computing and IoT integration, allowing organizations to manage their assets from anywhere, at any time. The future promises even more advancements, leading us to consider how technology will change the landscape of maintenance practices for years to come.
Understanding the historical context and evolution of work order maintenance software gives users invaluable insights into its current capabilities and potential future developments.
Key Features of Work Order Maintenance Software
Understanding the critical features of work order maintenance software is essential for organizations aiming to enhance their operational strategies. These features are not just fancy add-ons; they form the backbone of effective maintenance management. When crafted thoughtfully, key features can streamline processes, bolster communication, and elevate overall efficiency.
Task Management Capabilities
At the heart of work order maintenance software lies robust task management capabilities. This aspect allows users to create, assign, and track work orders seamlessly. Imagine being able to prioritize tasks based on urgency or importance–it’s like having a personal assistant that knows what's on your plate.
Furthermore, task management helps in visualizing workflows. Teams can unambiguously see who’s responsible for what and when it’s due, facilitating accountability. By utilizing these capabilities, organizations can reduce the tendency for double work or missed deadlines. It’s an organizational lifesaver, especially for industries dealing with high volumes of maintenance tasks.
Scheduling and Dispatching Functions
Scheduling and dispatching are like the gears of a well-oiled machine. They ensure that the right people tackle the right jobs at the right time. This function is particularly important for organizations where time is money. For instance, a hospitality management company will find it indispensable to maintain guest facilities promptly.
An effective scheduling feature allows users to input various factors such as technician availability, job duration, and location. This means that dispatchers can allocate resources thoughtfully, avoiding situations where technicians are too spread out or overloaded. Streamlined scheduling leads to reduced operational downtime and happier teams.
Reporting and Analytics Tools
What good are tasks and schedules if not measured for effectiveness? Here is where reporting and analytics tools come into play. They allow organizations to sift through data, glean insights, and make informed decisions. These tools turn raw data into visual representations, making it easier to see trends and patterns.
Consider a scenario where a maintenance team identifies that a specific piece of equipment frequently fails. Reporting tools can provide statistics that indicate maintenance frequency, resource allocation, and even cost analysis. Equipped with this information, decision-makers can strategize preventive measures that save money in the long run.
"Data is the new oil; it’s valuable, but if unrefined it cannot really be used."
Integration with Other Systems
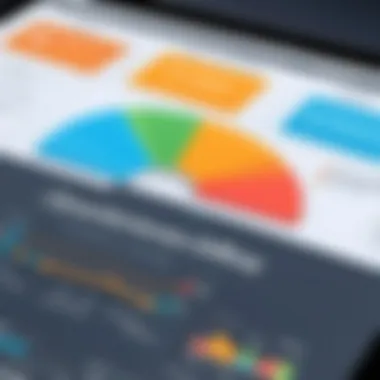
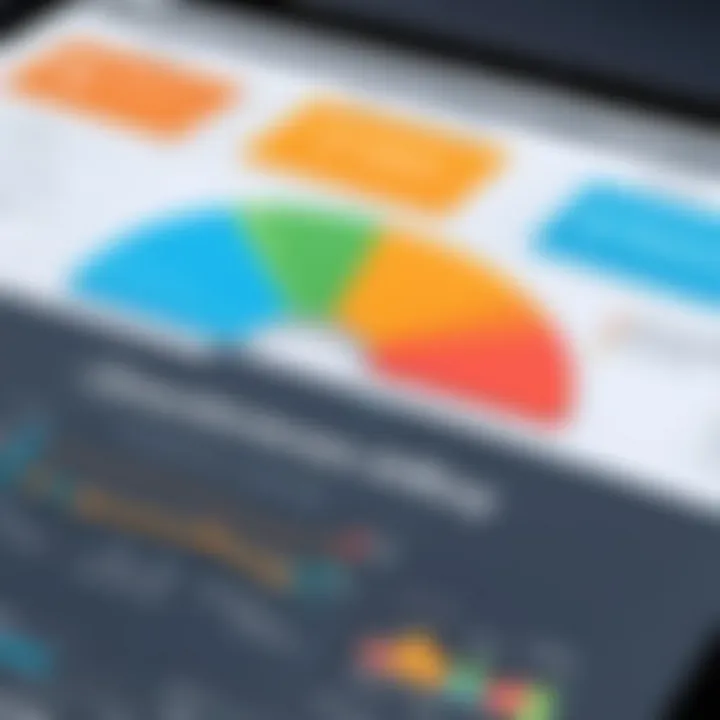
In today’s tech landscape, no software solution can afford to operate in isolation. Integration with other systems—like enterprise resource planning (ERP) software, inventory management tools, or financial systems—is crucial. This feature not only centralizes data but also ensures that all departments are aligned.
Moreover, proper integration can lead to improved accuracy in data entry. When one system updates, it reflects across others, minimizing discrepancies. Imagine an inventory management system notifying the maintenance team when supplies run low. Such interconnectedness fosters a proactive approach to challenges, making it easier for teams to pivot and adapt to changing scenarios.
In summary, the significance of key features in work order maintenance software cannot be overstated. They contribute to seamless task management, efficient scheduling, insightful reporting, and holistic integration with other systems. With these capabilities in place, organizations are empowered to not just maintain, but excel in their operational pursuits.
Advantages of Work Order Maintenance Software
The advantages of work order maintenance software are numerous and can be the lifeblood for many organizations looking to optimize their operational workflow. Businesses today face a deluge of tasks that must be managed effectively. From scheduling routine maintenance to documenting repairs, failing to streamline these processes can lead to inefficiencies that, over time, may consume resources and overwhelm teams. Adopting a comprehensive work order maintenance software system allows organizations to cut through the clutter and focus on what truly matters.
Enhanced Operational Efficiency
Operational efficiency often defines how well resources are used to achieve desired outcomes. With work order maintenance software in play, organizations can greatly enhance their efficiency levels. For instance, when technicians are assigned tasks, they receive immediate notifications, reducing downtime considerably compared to phone calls or paper-based systems.
This software enables real-time tracking of tasks. If a machine breaks down, a maintenance request can be logged instantly, prioritized, and dispatched to the right staff before the problem snowballs. In essence, the right software eliminates the guessing game of whether or not a task is in progress. Rather, stakeholders get clear insights from the dashboard about who is working on what and when a job is likely to be completed, leading to better resource allocation.
"Operational efficiency isn’t just about speed; it’s about precision too. Better management means fewer errors and smoother processes."
Improved Communication and Collaboration
Communication barriers can wreak havoc in any organization. Often, maintenance teams operate in silos, where a lack of cohesion results in misunderstandings about tasks and deadlines. Work order maintenance software can significantly bridge these gaps. By providing a centralized platform where all stakeholders can access, update, and comment on tasks, the software facilitates a culture of collaboration.
For instance, when a technician encounters an unexpected issue while executing a job, they can quickly leave notes within the system. This ensures that any follow-up actions are documented and actionable insights are shared across teams. Teams can collaborate effectively on complex issues, share best practices, and even consult on equipment-related problems swiftly.
Cost Savings and ROI
At the end of the day, the bottom line matters. Work order maintenance software directly contributes to cost savings and a higher return on investment. While there may be an upfront cost to implement this software, the long-term benefits often justify the expenditure. For starters, reducing wasted time on managing tasks manually can lead to higher productivity.
Moreover, with better oversight of maintenance schedules, organizations can minimize costly breakdowns and extend the life of their assets. By ensuring that all necessary maintenance tasks are scheduled and carried out on time, there is a noticeable drop in emergency repairs, which are typically far more expensive.
In summary, enhancing operational efficiency, improving communication, and realizing cost savings all weave together to construct a compelling case for adopting work order maintenance software. With the tech-savvy audience in mind, features like analytics tools contribute further to making informed decisions about future investments and operational strategies. It’s a win-win situation for forward-thinking organizations.
Challenges in Implementing Work Order Maintenance Software
When an organization decides to implement work order maintenance software, it stands at the crossroads of modernization and potential turbulence. The challenges associated with this transition can be significant and need thorough consideration. Understanding these obstacles is crucial for ensuring a smooth rollout and long-term success with the software. Here are three primary challenges that organizations tend to face:
Resistance to Change
One of the most common hurdles businesses encounter is resistance to change among employees. This resistance can stem from various sources, including fear of the unknown, disruption of established routines, or simple reluctance to adapt to new technology. Unlike switching brands of office supplies, software change can feel monumental. Employees often worry about how the new system retains data integrity, impacts their daily work, and whether they will have adequate training to use it effectively.
- Cultural Factors: Companies with a deeply rooted culture may encounter significant pushback as team members cling to familiar processes.
- Communication Gaps: Insufficient communication about the benefits and functionalities of the new software often leads to misconceptions and a lack of enthusiasm.
Addressing this resistance typically requires clear communication. Making sure that employees understand the reasons behind the transition can aid significantly. Involving team members in the decision-making process may help to ease their fears and gain their input.
Integration Issues with Existing Systems
Another significant challenge is integration issues with existing systems. Many organizations use a mélange of software solutions to manage their operations, from legacy systems to cutting-edge tools. Bridging the gap between these disparate systems can be like fitting a square peg into a round hole. If the new work order maintenance software doesn’t mesh well with existing tools for inventory management or customer relationship management, it could lead to data silos and workflow interruptions.
- Compatibility: Understanding the technical specifications of both systems is vital to see if they can "talk" to each other.
- Data Migration: Moving existing data to the new system can be fraught with complications, including data loss or corruption.
Organizations need to meticulously assess compatibility before implementation. A thorough integration plan can minimize disruptions and ensure data flows seamlessly during the transition.
Training and Onboarding Employees
Finally, there’s the unavoidable reality of training and onboarding employees. Even the most intuitive software can present a steep learning curve for users. Without proper training, employees might find themselves floundering in unfamiliar territory, which breeds dissatisfaction and undermines productivity.
- Comprehensive Training Programs: A one-size-fits-all training approach may not suffice. Different roles might need tailored sessions to address specific functionalities relevant to their day-to-day tasks.
- Ongoing Support: Staff should have access to ongoing support post-implementation to answer questions and troubleshooting issues.
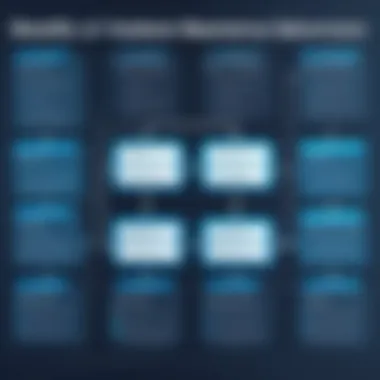
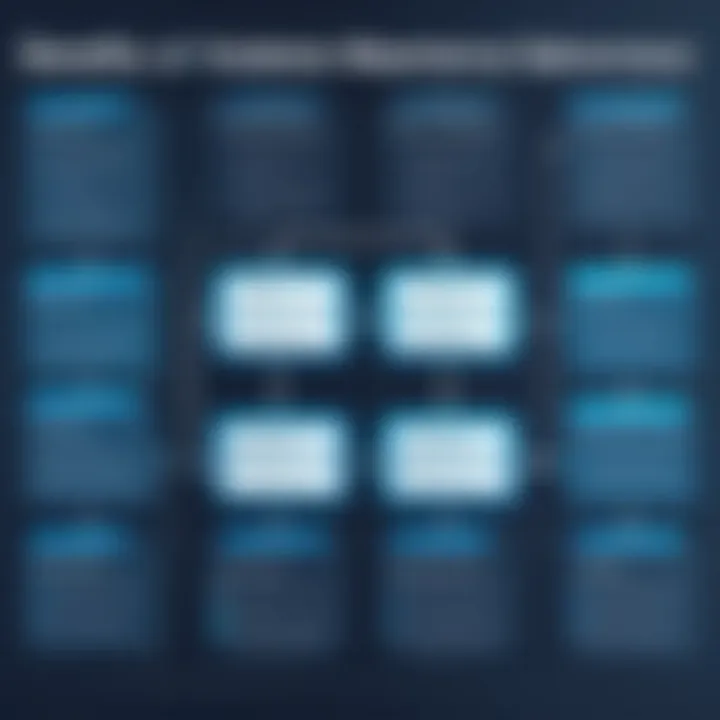
Utilizing a variety of training methods—from interactive workshops to video tutorials—can foster a smoother transition. Providing on-demand resources can also empower employees to learn at their own pace, helping to alleviate frustration.
"It's not just about having the software in place; it's about making sure people feel comfortable using it."
The path to successful implementation of work order maintenance software is fraught with challenges, but understanding these issues lays the foundation for a productive deployment. Addressing resistance, ensuring integration, and facilitating training can turn potential roadblocks into stepping stones for progress.
Market Landscape and Leading Providers
Importance of Market Landscape and Leading Providers
When dealing with work order maintenance software, understanding the market landscape as well as identifying the leading providers is crucial. The software choices available reflect the growing need for organizations to streamline operational processes, boost efficiency, and enhance collaboration across various teams.
This landscape isn’t just about picking a product off the shelf; it’s about finding solutions that align with organizational goals and daily operations. Knowing the key players in the industry allows decision-makers to gauge the features that can be leveraged and assess which tools best meet their requirements. This process ultimately impacts productivity, costs, and the overall health of a business.
Furthermore, keeping an eye on market trends can provide insights into what features will be indispensable in the near future. For example, if many companies are adopting AI-enhanced solutions, it may serve as a valuable indicator of the direction in which the industry is moving. In essence, familiarizing oneself with this landscape can guide strategic decisions that resonate throughout an organization’s structure and performance.
Top Software Solutions Reviewed
As you browse through the various options available in the realm of work order maintenance software, some solutions stand out due to their capabilities and utilities. Here's a detailed look at some of the top software solutions:
- FMX: This platform is known for its user-friendly interface and flexibility in handling different types of maintenance requests. It allows for scheduling, tracking, and entire management of work orders seamlessly.
- ServiceTitan: Often favored by service businesses, this software combines scheduling, dispatching, and reporting into one cohesive unit. Its robust analytics tools can help organizations understand their performance better.
- Hippo CMMS: With customizable features, Hippo is great for businesses looking to tailor their maintenance software to fit unique needs. Its cloud-based service allows for easy access and use from various locations, which is becoming increasingly important in today’s remote-work environment.
- eMaint: This software offers comprehensive asset management features, allowing organizations to achieve a high level of operational efficiency through effective maintenance management.
"Selecting the right work order maintenance software isn’t merely a tactical decision; it’s a strategic one that can redefine operational success."
Comparative Analysis of Features and Pricing
The next step is to conduct a comparative analysis of features and pricing. While many providers offer a basic set of functionalities, the real differentiators lie in unique features that cater to specific industries or operational needs.
Key Factors to Consider:
- Customization: How much can the software be tailored for specific business requirements?
- Scalability: Can the solution grow with the organization? This is vital for larger enterprises that may expand over time.
- Integration: Does the software integrate well with existing systems? Smooth integration can prevent many headaches down the road.
- User Experience: An intuitive interface can significantly reduce training times and increase adoption rates.
When it comes to pricing, potential buyers must evaluate not just the upfront costs but also any recurring fees, such as monthly subscriptions and support contracts. Some solutions might present initial lower pricing but could incur high additional costs for premium features or user licenses.
From this analysis, decision-makers can form a rounded view of which software might offer the best balance between features and cost, thereby making an informed decision aligned with the organization’s needs.
Evaluating Software for Your Organization
Evaluating software for your organization is not just a checklist item; it's a strategic move that can pave the way for a smoother, more efficient operational methodology. With the right work order maintenance software, you can foster a culture of productivity and accountability, while reducing miscommunication and overhead costs. This section will delve into three essential aspects: identifying organizational needs, scalability considerations, and user experience and interface design. Each element is pivotal in ensuring that you choose software that not only serves your current requirements but also anticipates future growth.
Identifying Organizational Needs
Understanding your organization's specific needs is akin to finding the right pair of shoes; if they don't fit well, they can cause discomfort and impede progress. When evaluating work order maintenance software, start by gathering input from various stakeholders. Engage with teams from maintenance, engineering, and management. Their insights can paint a vivid picture of the challenges they face and the tools they currently use.
A few guiding questions for this phase include:
- What are the most frequent maintenance tasks encountered?
- Which features in your current tools seem to be underutilized or ignored?
- How do teams communicate about maintenance tasks right now, and what are the bottlenecks?
This process should produce a clear overview of the required functionalities, potential gaps, and any unique specifications your organization might need. A direct approach to understanding your needs helps to mitigate future frustrations.
Scalability Considerations
Scalability isn’t just a buzzword; it’s a necessity in today’s fast-paced business environment. Imagine you’ve chosen software that perfectly addresses your needs today, only to find it falls short as your organization grows. You’d be back to square one, which is time-consuming and financially taxing.
When assessing different systems, consider:
- Will the software handle an increase in users or tasks?
- Is it adaptable to global growth scenarios?
- What is the update procedure? Is it seamless or cumbersome?
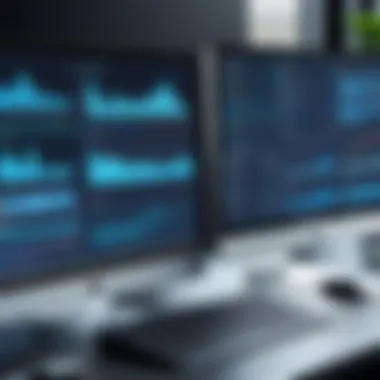
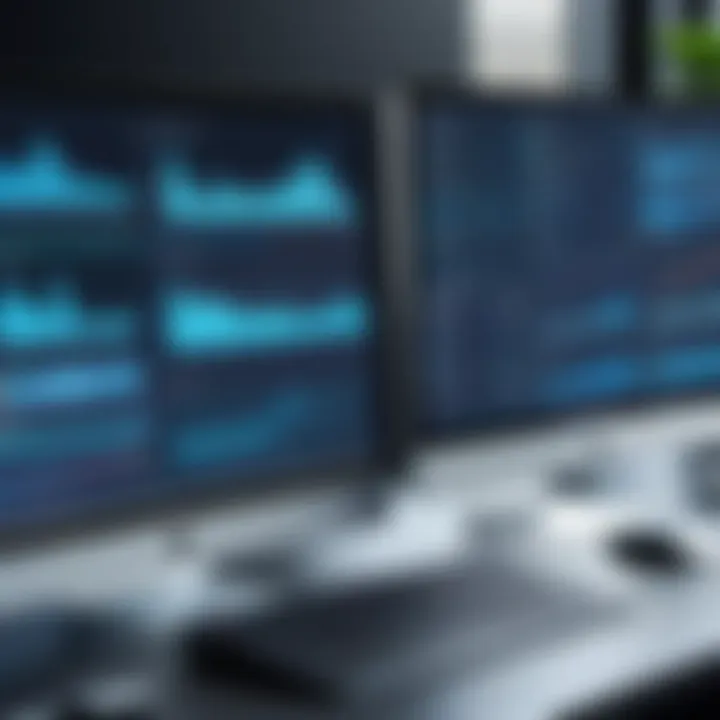
Modern work order maintenance systems typically come with features that allow for scaling, such as modular options where you can add functionalities as your needs evolve. Look for cloud-based solutions that inherently provide more flexibility and often lower maintenance costs.
User Experience and Interface Design
User experience is about more than just aesthetics; it directly impacts how effectively your employees can use the software. While a flashy interface can be eye-catching, it needs to also be intuitive. An effective interface reduces the learning curve, enhances productivity, and minimizes potential errors.
Consider these factors during your evaluation:
- Does the software have a user-friendly layout that simplifies navigation?
- Can tasks be completed with minimal clicks?
- Is it easy for users to access useful information quickly?
Take a look at feedback from current users of the software. Their experiences can reveal whether the interface truly supports their work routines.
"Choosing the right work order maintenance software is not merely an act of purchasing tools; it’s about equipping your team with a platform that enhances their capabilities while minimizing roadblocks."
In summary, evaluating software for your organization involves a thoughtful examination of its functionalities, scalability, and user experience. By honing in on these areas, you can select a work order maintenance software solution that not only meets your current needs but also has the capacity to support future growth.
Future Trends in Work Order Maintenance Software
As we gaze into the crystal ball of work order maintenance software, it’s evident that the landscape is shifting rapidly. The trends shaping this sector today are not just fads; they are foundational changes that offer substantial advantages to organizations willing to adapt. By harnessing emerging technologies, businesses can not only boost efficiency but also fortify their operational strategies for the future. Here, we outline some key trends that are carving the path ahead and why they matter.
AI and Machine Learning Integration
Artificial Intelligence (AI) and Machine Learning (ML) are at the forefront of the technological revolution, and work order maintenance software is no exception. These technologies empower organizations with the ability to process vast amounts of data, allowing for more informed decision-making.
- Predictive Maintenance: One of the standout capabilities of AI in maintenance software is predictive maintenance. By analyzing data from equipment and historical work orders, software can identify patterns that signal potential failures before they occur. Picture a scenario where a machine produces a specific sound when it’s about to break down; AI can detect this anomaly and alert staff, potentially saving thousands in repair costs and downtime.
- Resource Optimization: Alongside predictive maintenance, AI allows organizations to optimally allocate resources. For instance, it can suggest the most suitable technician for a specific task based on skills and availability. This not only improves work efficiency but also enhances employee satisfaction.
Mobile Accessibility and Remote Management
In today's hyper-connected world, mobile accessibility is no longer a luxury; it's a necessity. Employees on the go need to stay connected to their maintenance tasks, regardless of where they are.
- Real-Time Updates: Mobile-friendly work order maintenance software enables real-time updates, ensuring field workers have the latest information at their fingertips. Imagine a technician receiving live updates on work orders while they are on-site, which cuts down on back-and-forth communication and streamlines the process.
- Remote Management Capabilities: Remote management has become increasingly crucial, especially in a post-pandemic work environment. Decision-makers can manage work orders from any location, making it easier to maintain oversight and control. Consider the ability to assign tasks remotely, monitor progress, and check in with teams from a distance—this flexibility is invaluable in today’s fast-paced work culture.
The Role of IoT in Maintenance Software
The Internet of Things (IoT) is revolutionizing the way work orders are managed. With devices increasingly communicating with each other, the flow of information improves significantly.
- Data Collection: IoT-enabled devices can collect and transmit data about equipment performance in real time. For instance, in a manufacturing setting, sensors on machinery can provide insights into usage patterns and operating conditions. This information is invaluable for making data-driven decisions regarding maintenance schedules.
- Streamlined Communication: The integration of IoT with work order maintenance software facilitates seamless communication between devices and human operators. This connectivity not only boosts response times but also enhances problem-solving capabilities, as technicians can access detailed information about issues as they arise, rather than relying on historical data alone.
"Emerging technologies like AI, IoT, and mobile accessibility are redefining how organizations approach maintenance, delivering unprecedented efficiency and foresight."
Closure
Recognizing and adapting to these future trends in work order maintenance software is not merely about keeping up with the competition. It’s about positioning one's organization to thrive in an increasingly complex environment. With AI's predictive powers, mobile solutions offering flexibility, and IoT enhancing connectivity, organizations can optimize their maintenance strategies and leap into a future that promises greater efficiency and lower operational costs.
Epilogue
The concluding section of this article draws together the threads woven throughout our exploration of work order maintenance software. A clear understanding of this tool’s significance sets the stage for informed decisions in operational management.
Summarizing Key Insights
Throughout the discussion, we’ve labored through various facets of work order maintenance software, from its foundational definitions to its practical applications within organizations. Here’s a recap of some pivotal insights:
- Operational Efficiency: Implementing this software can drastically enhance productivity by streamlining processes. Suddenly, tasks that used to take valuable time can be completed in a snap, thanks to automation.
- Cost Management: By utilizing these systems, companies can pinpoint expenditures and waste, thus giving them the chance to cut costs and improve returns on investments.
- Integration and Scalability: The myriad advantages also come from the software's ability to integrate smoothly with other systems, making it adaptable to a wide range of needs.
Moreover, moving forward, the influence of AI, mobile access, and IoT continues to reshape the landscape. The goal isn't just to keep up; it's to leverage these technologies to gain a competitive edge.
Encouraging Strategic Decision-Making
- Alignment with Business Objectives: Ensure that the selected software not only fits current requirements but also is flexible enough to grow with the business.
- User-Centric Design: Focus on solutions that are intuitive. A complex interface can be more of a hindrance than a help. Employees need tools that empower them, not complicate their tasks.
- ROI Considerations: Analyze expected returns and measure success once the software is implemented. This will help validate the investment and shape future decision-making.
The world of work order maintenance software is ever-evolving. Keeping abreast of trends and understanding the software's strategic implications can spur organizations toward greater success.
Each choice made in this context has significant repercussions. By employing this knowledge wisely, organizations can navigate the complexities of their respective industries more adeptly and ensure that they keep their operational engines running smoothly.