Managing Multi-Location Inventory with QuickBooks
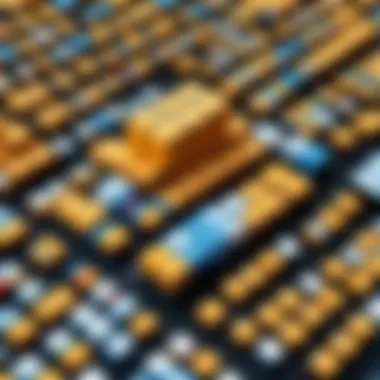
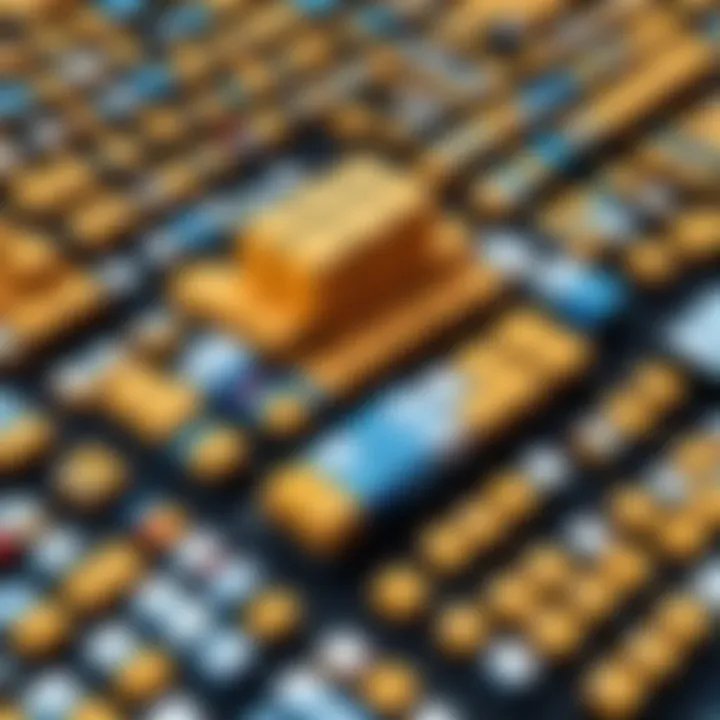
Intro
Managing inventory across multiple locations poses significant challenges for businesses. The complexity increases with each additional site, leading to potential inaccuracies and inefficiencies. Companies must track stock levels, sales data, shipments, and more, all while ensuring that operations run smoothly. To address these challenges, many organizations turn to QuickBooks, a versatile accounting software suite that offers comprehensive features for inventory management.
This guide aims to explore how QuickBooks can facilitate effective management of multi-location inventory. By delving into the specific functionalities, integration options, and practical tips, we will equip decision-makers with the tools needed to enhance their operational efficiency. Through this comprehensive analysis, our goal is to empower businesses with knowledge that fosters improved inventory decision-making in a multi-site environment.
Features Overview
Key Functionalities
QuickBooks provides various functionalities specifically designed to streamline inventory management across multiple locations. Key features include:
- Multi-location Tracking: QuickBooks allows users to categorize items based on different locations. This ensures that each siteβs inventory can be monitored separately, facilitating accurate stock management.
- Real-Time Data Updates: With QuickBooks, inventory data is updated in real-time. This feature minimizes discrepancies and allows managers to make informed decisions quickly.
- Automated Inventory Alerts: The software can send notifications when stock levels fall below a predefined threshold, enabling proactive restocking processes.
- Reporting Capabilities: QuickBooks offers robust reporting tools that give insights into inventory trends, sales performance, and stock utilization across locations.
Integration Capabilities
One of the significant advantages of QuickBooks is its ability to integrate seamlessly with other software solutions. This capability is crucial for multi-location inventory management, as it enables businesses to:
- Link to E-commerce Platforms: Integrating QuickBooks with platforms like Shopify or WooCommerce ensures consistent inventory data across sales channels.
- Utilize Shipping Solutions: With integrations available for shipping services like UPS and FedEx, users can manage shipping logistics without leaving the QuickBooks environment.
- Connect with CRM Systems: A connection to customer relationship management systems can enhance customer insights, leading to improved inventory decisions based on customer purchasing trends.
Pros and Cons
Advantages
Using QuickBooks for multi-location inventory has several advantages:
- User-Friendly Interface: QuickBooks is generally easy to navigate, making it accessible for users at different skill levels.
- Comprehensive Support: QuickBooks offers extensive resources and customer support, which can be beneficial for businesses new to multi-location inventory management.
- Cost-Effective Solution: For small to medium-sized enterprises, QuickBooks can be a more affordable solution compared to other specialized inventory management systems.
Disadvantages
However, there are some disadvantages to consider:
- Limited Customization: Some businesses may find QuickBooks lacks the level of customization required for specific inventory processes or complex operations.
- Scalability Issues: As a company grows, its inventory needs may outpace what QuickBooks can provide, leading to the need for a more robust solution eventually.
Preface to Multi-Location Inventory Management
Managing inventory across multiple locations is becoming increasingly vital in todayβs global market. As businesses expand, the challenges of keeping tabs on stock levels, turnovers, and supply chain complexities grow. Using advanced tools to coordinate these activities can significantly improve business operations and decision-making processes.
Understanding Multi-Location Inventory
Multi-location inventory refers to the ability to manage stock in various physical locations effectively. This can involve warehouses, retail outlets, or distribution centers. Each location needs a robust method for tracking incoming and outgoing inventory to avoid stockouts and overstock situations. Accurate tracking helps in understanding which products are performing well and which are not, allowing businesses to adjust strategies accordingly.
Key components of understanding multi-location inventory include:
- Visibility: Knowing what stock is available where often defines success for businesses. A clear overview helps in timely replenishment and curtailing excess inventory.
- Demand Forecasting: Effective forecasting can be accomplished using historical data, which in turn helps in making informed decisions about inventory levels at each site.
- Integration: Different locations often use various systems for inventory management. Integrating these systems can streamline operations and reduce errors.
The Importance of Inventory Management
Inventory management is crucial as it directly impact a company's bottom line. Efficient handling of inventory can lead to reduced operational costs, improved cash flow, and enhanced customer satisfaction.
Some factors that highlight the importance of effective inventory management are:
- Cost Reduction: Optimizing stock levels can prevent tying up capital in unsold inventory, leading to better utilization of resources.
- Improved Efficiency: Automating inventory tasks can free up staff to focus on strategic initiatives rather than repetitive tasks.
- Customer Satisfaction: Quick and reliable order fulfillment enhances customer experience, which is essential in a competitive landscape.
"Effective inventory management is not just about keeping track of stock; itβs about aligning inventory strategies with business objectives to maximize profitability."
In summary, the introduction to multi-location inventory management emphasizes the need for visibility and control in todayβs complex business environments. QuickBooks offers functionalities designed to tackle these challenges efficiently. Thus, a systematic approach to this management is vital for achieving operational excellence.
Challenges of Managing Inventory Across Multiple Locations
Managing inventory across multiple locations presents various difficulties. Each location operates independently, yet they all contribute to the overall efficiency of the business. Therefore, understanding these challenges is crucial. By acknowledging them, businesses can implement solutions to improve their operations and maintain customer satisfaction.
Inventory Discrepancies
One major challenge is inventory discrepancies. This situation occurs when the recorded stock levels do not match the actual stock on hand. Such discrepancies can arise from miscounts, theft, or errors in data entry. The effects can ripple through the supply chain, leading to stockouts, overstock situations, and lost revenue. Organizations must maintain accurate records, often through regular audits and checks, to overcome this issue. Utilizing QuickBooks can streamline tracking and reporting, helping businesses pinpoint these discrepancies more effectively. By establishing clear protocols for inventory management, discrepancies can be minimized.
Logistical Complexities
Logistical complexities also play a significant role in managing inventory across locations. The movement of goods between sites must be efficiently coordinated to ensure timely delivery. If one location runs low on stock, transferring inventory from another site requires precise planning and timing. Inaccuracies in these processes can lead to delays and increased costs. Technologies like QuickBooks facilitate streamlined logistics management by providing functionalities to schedule and track transfers. Implementing standardized procedures can alleviate confusion and enhance synergy between different locations.
Data Synchronization Issues
Data synchronization is another essential factor to consider. When managing multiple locations, it is vital that all data remains consistent and up-to-date across the board. Discrepancies in data can lead to chaotic inventory levels and can hinder decision-making processes. With QuickBooks, businesses can centralize information, making it easier to synchronize data in real-time. Regular updates and a solid communication strategy are critical components in achieving successful data synchronization. Without it, inventory management can become chaotic, hindering operational efficiency.
Overview of QuickBooks for Inventory Management
Understanding how QuickBooks supports inventory management is crucial for any business operating in multiple locations. Its capabilities not only streamline processes but also enhance decision-making efficiency. QuickBooks provides tools that can manage inventory from different sites, integrate data, and maintain consistency in stock levels. Given the complexities of managing inventory across various locations, utilizing a robust software solution like QuickBooks can save time and reduce errors.
By leveraging QuickBooks, businesses gain visibility into their inventory levels in real time. This visibility is essential for making informed decisions about purchasing and sales strategies. Moreover, QuickBooks aids in generating useful reports, which facilitate strategic analysis about stock levels and movements. Companies that understand these features can optimize their inventory management practices, improving overall efficiency and reducing operational costs.
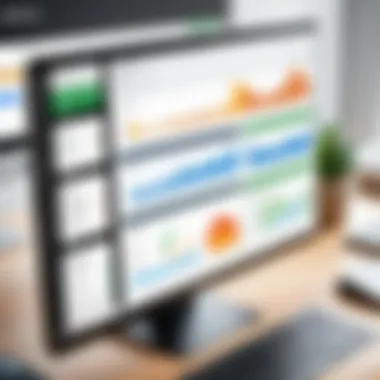
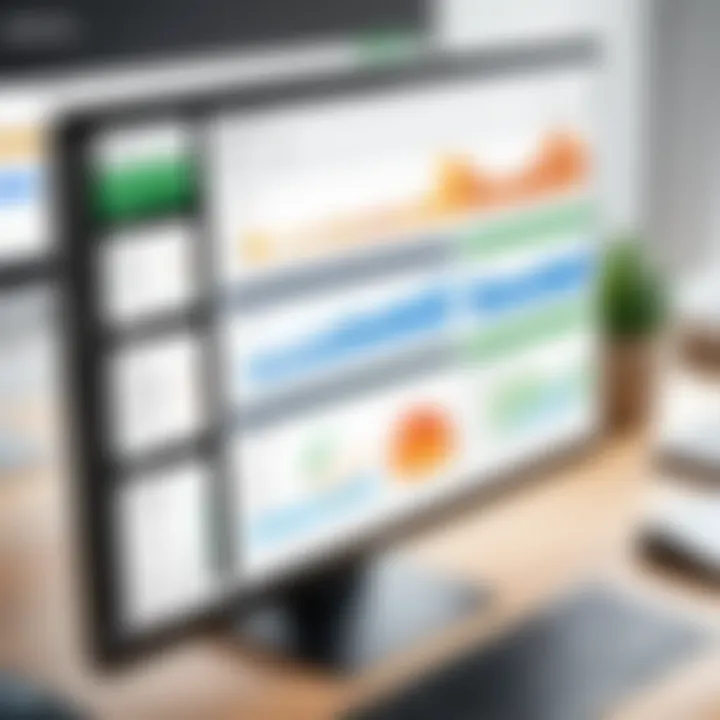
Key Features of QuickBooks
QuickBooks provides a variety of features tailored for effective inventory management:
- Real-Time Inventory Updates: This enables businesses to monitor stock levels as they fluctuate.
- Multi-Location Tracking: Companies can manage inventory across various sites seamlessly.
- Integration with E-commerce: QuickBooks connects with online sales platforms, consolidating data in one location.
- Reporting Tools: Advanced reporting features provide insights into sales trends and stock performance.
Each of these features plays a pivotal role in addressing the unique challenges that arise from managing inventory across multiple locations. QuickBooks equips users with the necessary tools to stay organized and proactive.
Different Versions of QuickBooks
Choosing the correct version of QuickBooks is essential based on specific business needs. Here are the main versions offered:
- QuickBooks Online: Ideal for businesses that require flexibility. This version can be accessed from any device with internet connectivity. It provides real-time inventory tracking and integrates with various apps.
- QuickBooks Desktop: A robust solution for businesses that prefer offline access. This version offers extensive inventory management features but may require more setup.
- QuickBooks Enterprise: Designed for larger organizations, it accommodates complex inventory requirements and extensive reporting capabilities.
Understanding the differences between these versions helps businesses select the solution that best aligns with their operational strategy. QuickBooks can adapt to various scales, making it suitable for startups as well as established enterprises.
"Choosing the right QuickBooks version can dramatically affect how efficiently your business runs its inventory management."
Selecting the appropriate version offers critical advantages that reflect on inventory handling and operational effectiveness.
Setting Up QuickBooks for Multi-Location Inventory
Setting up QuickBooks for multi-location inventory management is crucial for businesses operating across various sites. Effective configuration allows organizations to streamline their inventory processes, ensuring that data is accurate and up to date. Proper setup can lead to significant operational efficiencies. Businesses can control inventory levels and make informed decisions based on real-time data. This ultimately supports smarter purchasing, optimized stock levels, and improved customer satisfaction.
Configuring Multiple Locations
When configuring multiple locations within QuickBooks, it is essential to understand how the software can manage distinct inventory needs. Each location can represent a physical site where stock is held, allowing for tailored inventory tracking. To begin configuring, navigate to the company settings. This is typically under the Lists menu, followed by Locations.
- Enable Location Tracking: First, ensure that location tracking is enabled. This can be found in the Sales and Customers section of the configuration settings. Enabling this feature creates a foundation for managing data across different sites.
- Create Locations: Next, each physical site needs to be added. Here, you will input details such as the location name and address. Accuracy is vital, as this information supports logistics and customer orders. Locations can also be organized by region or type, further enhancing clarity in inventory management.
- Assign Products to Locations: After creating locations, assign inventory items to each site. This ensures that stock levels are monitored accurately. QuickBooks allows businesses to track how much inventory is available at each location, thus preventing overstocking or stockouts.
Configuring locations rightly during the setup phase significantly reduces confusion later on. It enhances key processes, such as transferring goods between sites, fulfilling orders, and reconciling inventory.
Creating Inventory Items
Creating inventory items in QuickBooks is one of the fundamental steps in managing multi-location inventory. Each item represents a specific product or good that is stocked. To create these items, follow these steps:
- Access the Item List: Within QuickBooks, go to the Lists menu and select Item List. Here, you will see your existing inventory and have the option to add new items.
- Create New Item: Click on the Item button and select New. Choose the appropriate item type based on your inventory. For multi-location tracking, you may want to select either Inventory Item or Non-inventory Item depending on how you plan to manage it.
- Input Details: Fill in the item details such as item name, description, and purchase information. Ensure to designate the location to which this item primarily belongs. This assists in tracking and managing stock levels effectively.
- Set Up Inventory Levels: Establish the quantity on hand for each location. This data is vital for real-time inventory tracking. Setting these levels allows QuickBooks to calculate the reorder points and alert you when stocks are low.
Creating well-defined inventory items ensures that QuickBooks can provide accurate reporting and analysis later. It serves as a critical reference point for inventory levels and helps with financial forecasting.
Accurate setup of QuickBooks for multi-location inventory allows businesses to monitor stock efficiently, reduce discrepancies, and enhance overall productivity.
By meticulously configuring locations and accurately creating inventory items, organizations position themselves for better inventory control and streamlined operations.
Tracking Inventory Levels Across Locations
Tracking inventory levels across multiple locations is crucial for maintaining operational efficiency in businesses with diversified inventory systems. It enables companies to optimize stock levels, reduce excess inventory, and improve order fulfillment rates. When done effectively, real-time tracking can lead to significant cost savings and enhance customer satisfaction.
The importance of this process is manifold. It helps businesses avoid stockouts, which can hinder sales and damage customer loyalty. Additionally, understanding inventory levels enables organizations to make informed purchasing decisions. With the proper data, decision-makers can allocate resources where they are needed and decrease the risk of overstock situations that tie up capital.
Moreover, precise inventory tracking is vital for accurate financial reporting. Accurate records of inventory levels contribute to effective balance sheets and facilitate better organizational insights. Thus, businesses that prioritize tracking inventory levels can position themselves favorably in a competitive market.
Real-Time Inventory Tracking
Real-time inventory tracking is a core feature that many businesses need in todayβs fast-paced environment. This capability allows businesses to monitor stock levels continuously, giving them immediate insights into the balance of goods across their locations. With tools like QuickBooks, businesses can receive alerts when stock levels reach predefined thresholds, ensuring they can quickly respond to changing demands.
Using real-time inventory tracking offers several advantages:
- Immediate Updates: Changes in inventory are recorded instantly across all channels and locations, reducing the chance of discrepancies.
- Enhanced Visibility: Decision-makers can see exactly where inventory is located and how it is moving.
- Efficient Replenishment: Businesses can automate reordering processes based on current stock levels, minimizing manual interventions.
Real-time tracking can be integrated into e-commerce platforms or warehouse management systems, providing a seamless approach to inventory management.
Setting Reorder Points
Setting reorder points is a vital practice in inventory management that helps ensure businesses do not run out of stock. A reorder point is the predetermined inventory level that triggers the need to reorder products. By accurately calculating these points based on sales data and lead times, companies can streamline the restocking process effectively.
Factors to consider when setting reorder points include:
- Sales Velocity: Understanding how quickly products sell is crucial for determining when to reorder.
- Lead Time: The time it takes for suppliers to deliver products impacts how early reorder points should be set.
- Safety Stock: Keeping a buffer stock helps mitigate risks associated with demand surges or supply chain disruptions.
Businesses that implement reorder points effectively can enhance their inventory management strategy, ensuring they maintain adequate stock levels without overstocking.
"Effective inventory management hinges on the ability to track and anticipate product flow across multiple locations."
In summary, tracking inventory levels across multiple locations and implementing strategies, such as real-time tracking and setting reorder points, are integral to effective inventory management. Utilizing solutions like QuickBooks for these processes allows businesses to function more efficiently, ultimately boosting profitability and customer satisfaction.
Managing Transfers Between Locations
Managing inventory across multiple locations is not just about tracking stock levels; it also involves efficiently transferring items between sites. This process is crucial for maintaining operational efficiency and ensuring that customers receive their products promptly. With QuickBooks, businesses can streamline this process, minimizing delays and reducing the risk of stockouts or overstock situations. The ability to transfer inventory seamlessly aids in achieving optimal stock levels across all locations, thereby enhancing customer satisfaction and increasing sales opportunities.
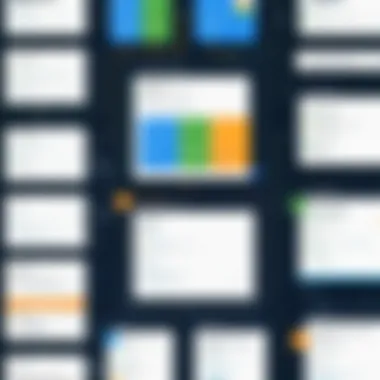
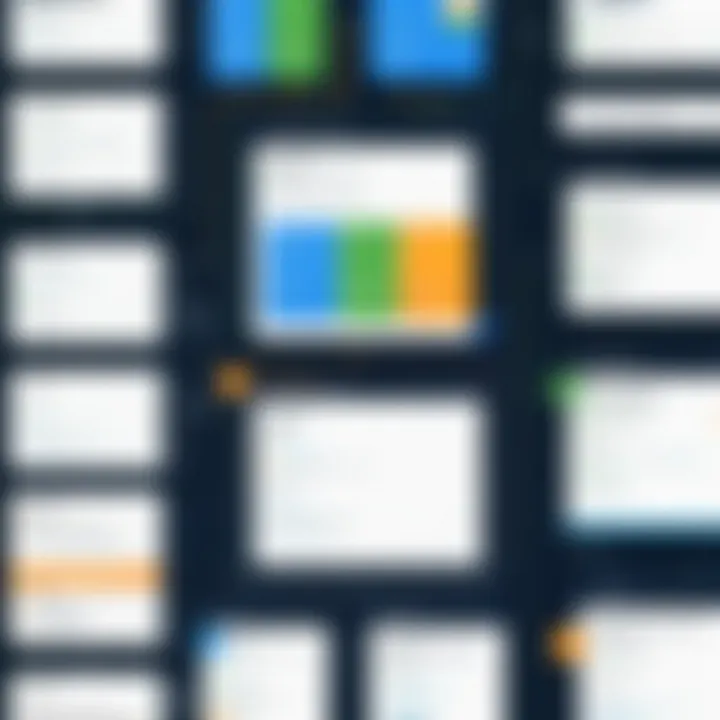
Initiating Transfers in QuickBooks
To initiate a transfer of inventory in QuickBooks, start by accessing the appropriate feature within the software. Navigate to the Inventory menu and find the option for "Transfer Inventory." This action allows you to specify the source location from where goods will be sent and the destination location where the inventory will arrive.
- Select the Item: Choose the inventory items that you wish to transfer. Each item should be clearly listed with its current quantity available in the source location.
- Enter Quantities: Carefully input the quantities being transferred. It is important to ensure accuracy to prevent discrepancies in inventory levels.
- Set Transfer Date: Assign a date for the transfer. This helps in tracking when items were moved and facilitates better record-keeping.
- Review and Confirm: Before finalizing the transfer, review the details for accuracy. Confirm all entries and then execute the transfer. This step is vital to ensure there are no mistakes that could affect inventory control.
Following these steps not only allows for a smooth transfer process but also ensures that all locations have real-time updates regarding inventory status. Such accuracy is essential for effective decision-making.
Monitoring Transfer Status
Once a transfer has been initiated, staying on top of its status is vital. QuickBooks provides functionalities that allow users to monitor inventory transfers efficiently.
Effective monitoring involves several steps:
- Check Transfer Status: Go to the "Inventory Transfers" section within QuickBooks to check the current status of pending transfers. Updates will show whether transfers are complete or still in progress.
- Receive Notifications: Set up alerts to receive notifications when a transfer is completed. QuickBooks can be configured to send these alerts, helping teams remain informed without manual checks.
- Reconcile Inventory: When items are received at the destination location, reconciliate the inventory counts. Ensure that the quantities match the transfer records generated during the initiation phase. It is important to promptly address any discrepancies as they arise.
By closely monitoring these transfers, businesses can maintain accurate records and ensure that stock is available where it is needed most. This practice allows for quicker responses to market demands and helps prevent over- or under-stocking issues that can impair business operations.
Generating Reports for Multi-Location Inventory
Generating reports for multi-location inventory is crucial for any business that operates in various locations. The ability to compile, analyze, and interpret data across different sites enables informed decision-making. These reports not only provide insights into inventory levels but also help identify trends, inefficiencies, and opportunities for improvement.
When managing inventory across multiple sites, reports can show how inventory flows between locations. They can highlight which locations have excess stock, which are at risk of running out, and where sales are strongest. This gives management a tactical edge in aligning inventory with customer demand. Here are some specific benefits of generating reports for multi-location inventory:
- Visibility: Regular and detailed reports increase visibility into stock levels and sales performance. This helps to avoid stockouts and overstock situations.
- Efficiency: Understanding inventory metrics allows businesses to enhance efficiency, streamline operations, and reduce costs.
- Strategic Planning: Data-driven reports support better forecasting and strategic inventory planning across locations.
Considerations for effective report generation include ensuring accurate data entry across locations and selecting relevant metrics that align with business objectives.
Sales Reports by Location
Sales reports by location are essential for understanding the performance of each site. Analyzing sales data helps businesses pinpoint geographic areas that perform well or those that may need attention. QuickBooks provides the capability to generate these reports, which can be tailored to show various time frames and metrics.
When creating sales reports, consider the following aspects:
- Monthly or Quarterly Comparisons: These comparisons help assess growth trends over time.
- Top-Selling Products: Knowing which products are best-sellers at specific locations can inform inventory stocking decisions.
- Customer Preferences: Sales reports can uncover local preferences, allowing businesses to adapt their offerings accordingly.
Sales reports by location not only enhance operational insight but also contribute to optimizing marketing strategies tailored to specific demographics or regions.
Inventory Valuation Reports
Inventory valuation reports provide a financial perspective on the value of goods held at various locations. These reports detail the overall worth of inventory, allowing businesses to understand their assets better. They are especially useful for accounting and financial analysis.
With QuickBooks, businesses can generate inventory valuation reports to:
- Assess Business Value: Understanding the total value of inventory can impact financials and investment decisions.
- Inventory Costing Methods: The reports can reflect different inventory costing methods, such as FIFO (First In, First Out) or LIFO (Last In, First Out), affecting profit margins and tax obligations.
- Liquidation Planning: Accurate valuation assists in making informed decisions about liquidating excess stock or discontinuing products.
Integrating QuickBooks with Third-Party Solutions
Integrating QuickBooks with third-party solutions is crucial for enhancing the functionality and efficiency of inventory management across multiple locations. These integrations allow businesses to leverage additional tools and systems that complement QuickBooks' capabilities. With the right integrations, companies can streamline their processes, reduce errors, and enhance overall productivity. It involves connecting modern software solutions that cater to specific needs, thus automating various tasks and providing real-time data insights. This process requires careful consideration of existing workflows, compatibility of solutions, and ongoing support to maximize the technology investments.
E-commerce Platforms
E-commerce platforms play an essential role in today's business environment. Integrating QuickBooks with e-commerce solutions such as Shopify, WooCommerce, and BigCommerce can dramatically improve inventory management. By establishing a direct connection, businesses can automatically sync sales data, inventory levels, and customer information without manual entry. This reduces the risk of errors and ensures that data remains consistent across platforms.
Here are some key benefits of such integration:
- Real-Time Updates: Inventory levels in QuickBooks reflect sales from the e-commerce platform instantly, preventing overselling.
- Enhanced Reporting: Businesses can analyze sales trends and inventory turnover across channels to make informed decisions.
- Streamlined Accounting: Automating the flow of sales data into QuickBooks simplifies bookkeeping efforts, thus saving time.
Integrating e-commerce platforms requires an understanding of both systems to ensure seamless operation. Businesses should evaluate their needs and determine the best integration methods to align with their specific e-commerce model.
Warehouse Management Systems
Integrating QuickBooks with warehouse management systems (WMS) is another pivotal aspect of effective inventory management. A robust WMS facilitates efficient tracking of stock levels and movements within warehouses. When combined with QuickBooks, businesses can gain deeper insights into their inventory processes and enhance operational efficiency.
Key considerations for integrating warehouse management systems include:
- Improved Accuracy: A WMS tracks items in real-time, ensuring that QuickBooks reflects accurate data on stock levels and locations.
- Efficient Order Fulfillment: With a WMS, businesses can pick, pack, and ship products more efficiently, decreasing order processing time.
- Inventory Optimization: These systems enable effective management of stock across multiple locations, reducing holding costs and mitigating the risk of stockouts.
The successful integration of a WMS with QuickBooks can lead to greater overall supply chain efficiency. Companies should ensure the chosen WMS is compatible with QuickBooks, providing easy-to-use interfaces and necessary support to facilitate effective communication between the two platforms.
Understanding integrations with e-commerce and warehouse management systems can unlock new efficiency levels, propelling businesses into future growth.
Best Practices for Successful Inventory Management
Effective inventory management is crucial for organizations operating across multiple locations. Implementing best practices can help in maintaining accuracy, ensuring timely access to stock, and improving overall operational efficiency. When managing inventory, especially in multi-location scenarios, having a structured approach allows businesses to reduce waste, optimize costs, and enhance customer satisfaction.
A strategic inventory management system not only streamlines processes but also aids in effective decision-making. Understanding how to implement these best practices can lead to significant improvements and a competitive edge in the market.
Regular Audits and Reconciliation
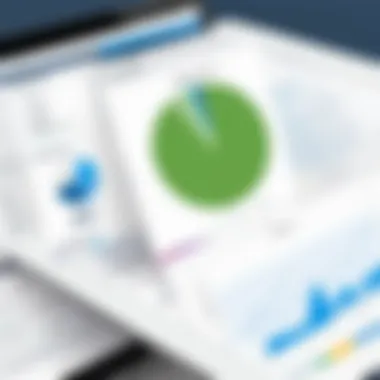
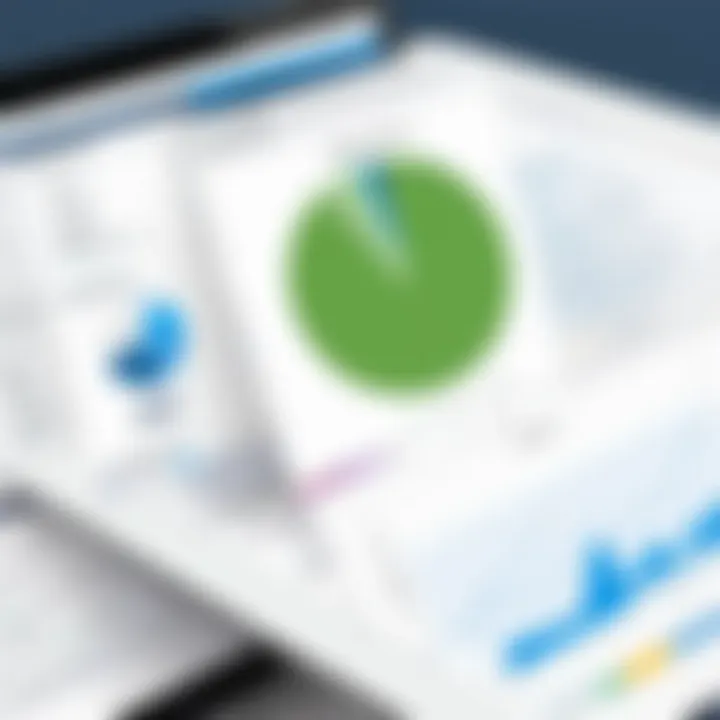
Routine audits and reconciliations are essential components of inventory management. These practices help ensure that physical stock accurately reflects recorded inventory levels in QuickBooks. Regular audits can uncover discrepancies that might arise from various sources, such as data entry errors or theft. This proactive approach significantly reduces potential losses.
Conducting audits on a regular basis can involve:
- Cycle Counting: Performing targeted audits on specific inventory items while keeping the rest unaffected ensures continuous monitoring.
- Full Inventory Counts: These are comprehensive counts conducted at designated times. This method, although disruptive, is beneficial for smaller operations needing thorough checks.
- Reconciliation: Cross-checking physical counts against QuickBooks records helps identify any mismatches and correct them promptly.
Incorporating audits into standard operating procedures fosters a culture of accountability and attention to detail. Moreover, technology can be leveraged for enhancing accuracy. Using barcodes or RFID systems integrated with QuickBooks can reinforce real-time updates and error reduction. Regular audits not only improve accuracy but also instill confidence in the overall inventory management system.
Training Staff on Inventory Procedures
Training is critical in maintaining an efficient inventory management framework. Proper staff training ensures that all employees understand the importance of inventory control and are adept at using QuickBooks for managing stock levels. Staff that are well-informed about inventory processes can help prevent mishaps that lead to data inaccuracy or logistical issues.
Key areas in staff training should include:
- Inventory Tracking: Making sure all employees know how to effectively input and track inventory changes within QuickBooks.
- Procedures for Stock Intake and Dispatch: Understanding the correct methods for receiving and delivering products can help reduce errors and speed up processes.
- Understanding Stock Value: Staff should be educated on how stock valuation affects financial reporting and decision-making.
In addition, continuous training and refresher courses are valuable. As QuickBooks updates its features, keeping staff informed ensures that they utilize all available tools effectively. Providing resources such as user manuals, video tutorials, or access to external forums can enhance learning.
"The efficiency of your inventory management system rests not just on the tools used, but also significantly on the proficiency of the personnel utilizing these tools."
Combining regular audits with training ensures an organization remains agile. This helps to navigate the complexities of multi-location inventory management effectively.
Common Mistakes to Avoid
Effectively managing multi-location inventory involves recognizing potential pitfalls that can lead to costly errors. Identifying and avoiding these mistakes not only streamlines operations but ensures accuracy in inventory data. This section outlines significant errors commonly made in this domain. Understanding these errors enables businesses to implement strategies that mitigate risk, resulting in better decision-making and enhanced operational efficiency.
Neglecting Data Accuracy
A common mistake in inventory management is neglecting data accuracy. When businesses fail to maintain precise inventory records, they run the risk of making ill-informed decisions. This can affect purchasing, sales forecasting, and even day-to-day operations.
Inventory discrepancies often arise from manual data entry errors or lack of regular audits. If incorrect figures are present, businesses might overstock or understock products, leading to dissatisfied customers or excess inventory costs.
To prevent this, businesses should implement systematic checks.
- Regular Audits: Consistent and thorough inventory audits help catch discrepancies early. This practice ensures that what is recorded matches the physical stock.
- Automated Entry: Utilizing software features in QuickBooks can limit manual entry errors. Integration with barcode scanners or ERP systems can enhance data accuracy, promoting improvement.
Accurate data management also aids businesses in understanding sales trends, enabling informed decisions about restocking and promotions. Thus, prioritizing data accuracy is paramount for successful multi-location inventory management.
Overcomplicating Processes
Overcomplicating inventory processes is another critical mistake. Complexity often arises from using multiple systems or complicated workflows to manage inventory. When employees face convoluted procedures, they can become overwhelmed, leading to mistakes or important tasks being ignored.
Simplification enhances clarity.
- Streamlined Workflows: Make use of QuickBooks features to create simple and straightforward workflows for handling inventory. Each stage from tracking to transferring stock should be effortless to manage.
- Standard Procedures: Adopting standard operating procedures across all locations can ensure consistency. Training team members on these procedures simplifies the inventory management process while enhancing compliance.
In addition, fewer steps in operations mean lesser chances for error. By reducing complexity, businesses can boost the productivity of their team and protect their overall operational integrity.
Remember: Simplifying processes does not undermine the effectiveness; instead, it often magnifies it.
Recognizing and addressing these common mistakes is essential in optimizing multi-location inventory management. By prioritizing data accuracy and simplifying processes, businesses can create a more efficient operational framework with QuickBooks.
Future Trends in Inventory Management
In the rapidly evolving landscape of inventory management, keeping pace with current trends is vital for success. Businesses today face increasing complexities and demands in managing their multi-location inventory. Embracing future trends can lead to operational efficiency, cost reduction, and improved customer satisfaction. This section focuses on two significant trends: automation and AI integration, along with enhanced data analytics.
Automation and AI Integration
The integration of automation and Artificial Intelligence into inventory management systems transforms traditional practices. Automation streamlines repetitive tasks, reducing human error and freeing up staff time for more strategic activities. AI integration allows businesses to forecast trends based on historical data, helping in inventory optimization. QuickBooks, for example, enables automated reporting and stock level updates across multiple locations. With these systems, companies can lead their operations more easily, ensuring the right products are stocked while avoiding overstocking or stockouts.
The capabilities of AI extend to intelligent decision-making. Algorithms can analyze sales patterns, seasonality, and customer behavior. This data-driven approach ensures that inventory levels are adjusted proactively, which is particularly beneficial in industries with fluctuating demand. Optimizing inventory through AI not only enhances efficiency but supports better financial performance.
"Businesses that embrace automation and AI are setting themselves up for a competitive edge in inventory management."
Enhanced Data Analytics
Data analytics has become a cornerstone of effective inventory management. With tools available today, businesses can analyze vast amounts of data to make informed decisions. QuickBooks provides useful reporting capabilities that reveal insights related to inventory performance and sales trends by location. This information is pivotal for adjusting purchasing strategies and inventory allocation across different sites.
By employing enhanced data analytics, businesses can also monitor key performance indicators (KPIs) related to inventory. Common metrics include inventory turnover, carrying costs, and stock variance. Tracking these indicators enables prompt identification of issues such as excess stock or slow-moving items, thus facilitating timely action to improve overall inventory health.
Overall, integrating advanced analytics into inventory systems fosters a proactive rather than a reactive approach. By making data-informed decisions, businesses can improve responsiveness to market changes and optimize operations in a sustainable manner.
Ending
Inventory management is a complex yet crucial aspect of running a multi-location business. This article has delved deep into various dimensions of managing multi-location inventory using QuickBooks. Understanding how to effectively manage inventory across multiple sites can lead to significant improvements in operational efficiency and cost-effectiveness.
Summary of Key Points
- Multi-location inventory management is essential for businesses with various sites. It helps streamline operations and ensures that stock levels are accurate across locations.
- Challenges such as inventory discrepancies, logistical complexities, and data synchronization issues need to be addressed for effective management.
- QuickBooks offers key functionalities that cater specifically to multi-location inventory needs, including real-time tracking and reporting.
- Setting up QuickBooks correctly is vital. Configuring multiple locations and creating inventory items is the first step to efficient management.
- Monitoring transfers between locations and generating tailored reports are other critical elements that enhance decision-making and operational workflow.
- Best practices include regular audits, staff training, and avoiding common mistakes like neglecting data accuracy.
- The future of inventory management is leaning towards automation and enhanced analytics, which QuickBooks can facilitate.
Final Thoughts on Using QuickBooks
Using QuickBooks for managing multi-location inventory simplifies many of the challenges faced by businesses. This software not only supports the logistical aspect of managing inventory across various locations but also empowers businesses through robust data analytics. By consistently monitoring inventory levels and generating insightful reports, businesses can make informed decisions that can lead to growth and efficiency.
Emphasizing the integration of QuickBooks with third-party solutions can further enhance inventory management capabilities. As trends like automation continue to evolve, adapting to these changes with QuickBooks sets a foundation for successful inventory practices.