Exploring the Infoplus Warehouse Management System
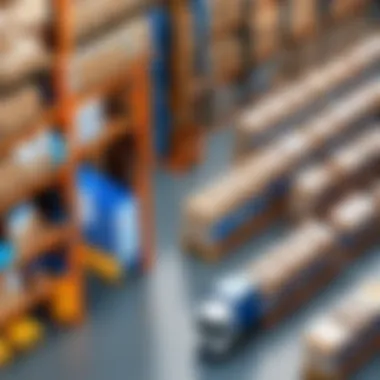
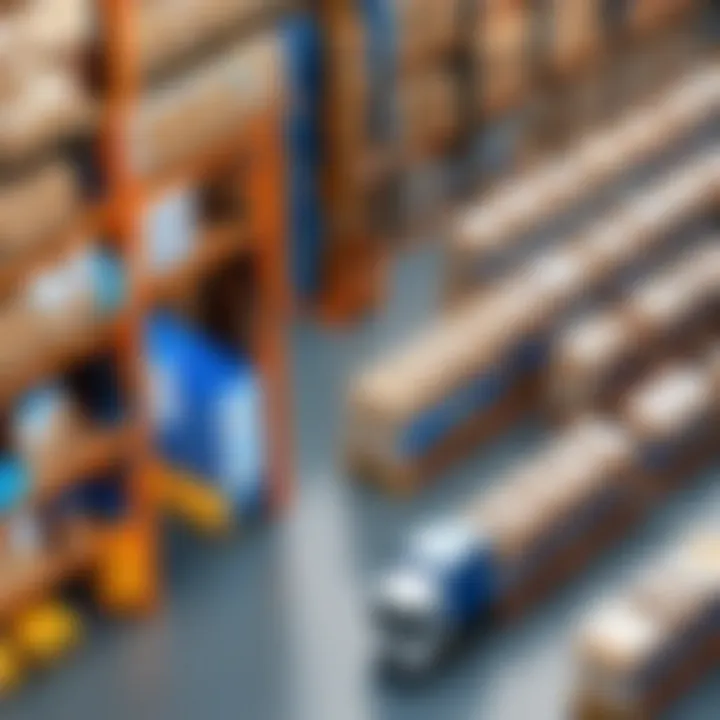
Intro
In today's fast-paced business environment, optimizing warehouse operations has become not just a competitive advantage, but a necessity. The Infoplus Warehouse Management System presents a comprehensive solution for organizations looking to streamline their logistics processes. This platform offers a range of functionalities designed to enhance efficiency, increase accuracy, and ultimately save costs. Understanding the ins and outs of Infoplus can be the difference between a well-oiled machine and a disorganized stockroom.
This exploration dives into the nuts and bolts of the Infoplus system, detailing its key features, integration capabilities, and the pros and cons associated with its implementation. For professionals navigating the dizzying world of B2B software solutions, this guide will serve as an invaluable resource, shedding light on how Infoplus can help redefine warehouse management.
Features Overview
The Infoplus Warehouse Management System is designed with an array of features that cater to the diverse needs of a modern warehouse.
Key Functionalities
The core functionalities of Infoplus include:
- Inventory Management: Keep tabs on stock levels, manage reorder points, and track product movements efficiently.
- Order Fulfillment: Automate order processing, pack, and ship with precision, ensuring customers receive their goods when they expect.
- Reporting and Analytics: Generate insightful reports to monitor warehouse performance, spot trends, and make data-driven decisions.
- Mobile Access: Stay connected with mobile capabilities that allow staff to manage tasks right from their smartphones or tablets.
These functionalities revolve around the fundamental goal of boosting productivity while minimizing errors.
Integration Capabilities
Integrating Infoplus with existing systems can significantly enhance overall operational efficiency. Here are a few integration capabilities:
- E-commerce Platforms: Seamlessly connect with popular platforms such as Shopify and Amazon to enhance order processing.
- Shipping Carriers: Connect to USPS, FedEx, and UPS for real-time shipping rates and tracking.
- Accounting Software: Integrate with tools like QuickBooks to simplify financial management.
By facilitating these integrations, Infoplus allows businesses to foster a more responsive and dynamic operating environment.
Pros and Cons
Like any robust software solution, Infoplus comes with its set of advantages and disadvantages.
Advantages
- Scalability: Infoplus can grow alongside your business, adapting to increased inventory and order volumes.
- User-Friendly Interface: Designed with usability in mind, training new employees on the system can be quick and straightforward.
- Customizable Workflows: Tailor the system to meet specific operational needs, ensuring it works the way your team operates.
In essence, these advantages contribute to not just easing daily tasks but also fostering long-term success.
Disadvantages
- Cost: Implementing the entire suite can represent a significant upfront investment for smaller businesses.
- Learning Curve: Although user-friendly, some features may still require time to fully grasp, particularly for those less tech-savvy.
- Reliance on Internet Connectivity: Being cloud-based means that stable internet access is crucial. Outages can impede operations.
While these disadvantages may pose challenges, many businesses find the benefits outweigh the drawbacks, especially when it comes to enhancing supply chain efficiencies.
"Investing in the right warehouse management system is a crucial step towards achieving a seamless supply chain experience."
With this foundational understanding of the Infoplus Warehouse Management System, professionals are better positioned to evaluate how this platform can fit into their operational landscape, helping to not only meet but exceed their logistical demands.
Understanding Warehouse Management Systems
In the highly competitive landscape of logistics and supply chain management, Warehouse Management Systems (WMS) have emerged as a core component. By helping businesses manage warehouse operations more effectively, WMS solutions play a pivotal role in enhancing efficiency. Grasping the essence of these systems is crucial for companies aiming to optimize their storage capabilities and streamline operations. With rapid growth in e-commerce and customer expectations, understanding warehouse management isn’t just an option; it’s a necessity.
Definition and Purpose
A Warehouse Management System is a software application designed to support and optimize warehouse functionality and distribution center management. Its primary purpose is to facilitate the management of inventory and logistics operations through various processes such as tracking stock levels, order processing, and shipping activities. Essentially, the system acts as a backbone of the warehouse environment, ensuring that goods are stored correctly and accessible when needed. When implemented correctly, a WMS can drastically cut down on the chances of errors, ensuring that correct items reach customers quickly.
Key Components of WMS
The intricate functions of a WMS are driven by various components that work in unison. Understanding these components is fundamental for anyone looking to leverage a WMS effectively:
- Inventory Control: The heartbeat of WMS, it helps in tracking inventory movements, ensuring a real-time view of stock levels and preventing overstock or stockout situations.
- Order Management: Seamlessly processes incoming orders while managing their fulfillment with precision, handling everything from picking to packing.
- Shipping Management: Coordinates the picking and shipping processes, enhancing logistics efficiency and ensuring timely delivery.
- Receiving Management: Manages incoming goods to ensure that items are accounted for and properly integrated into inventory.
- Reporting & Analytics: Offers insights into various operational aspects, which aids in forecasting demand, optimizing storage, and improving operational processes.
These components embody the workings of a WMS, making it a vital tool for modern warehouses.
Importance in Modern Logistics
The significance of Warehouse Management Systems cannot be overstated, especially in today’s fast-paced digital world. A robust WMS not only enhances efficiency but also serves as a catalyst for greater strategic planning. Here’s why understanding a WMS is so crucial:
- Operational Efficiency: Reducing manual errors and optimizing workflows leads to a more streamlined operation. WMS contributes to shorter order processing times, which in turn drives customer satisfaction.
- Cost Reduction: By improving inventory accuracy and reducing waste, WMS assists businesses in saving costs related to overtime labor and misplacement of stock.
- Scalability: As business grows, a WMS can scale along with it. This flexibility is essential for handling increased workloads without significant downtime or restructuring.
- Data-Driven Decisions: The analytical capabilities of a WMS offer companies the ability to make informed decisions based on real-time data, thus enhancing their strategic positioning.
Investing in a Warehouse Management System stands not just as a tactical response to operational challenges, but as a strategic initiative poised to align logistics with overarching business goals.
Overview of Infoplus WMS
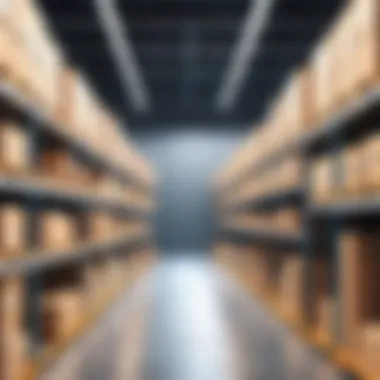
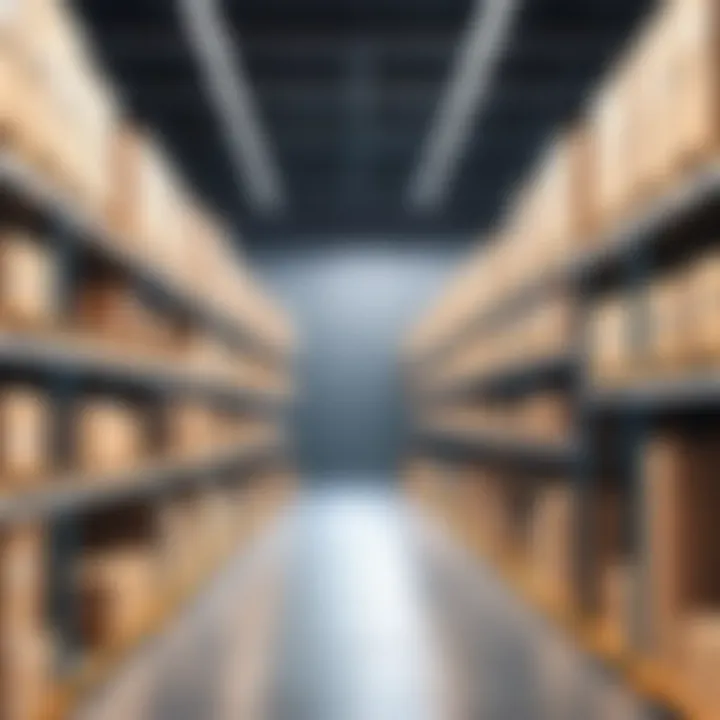
The Infoplus Warehouse Management System (WMS) stands as a critical component in the realm of logistics and supply chain management. In today's fast-paced and ever-evolving market, businesses face the challenge of efficiently managing inventory, fulfilling orders, and maintaining data accuracy. This overview will dissect not just the system's framework but also its pivotal role in transforming warehouse operations.
Company Background
Infoplus has carved out a niche in providing robust and adaptable solutions tailored for warehouses of all sizes. Founded with the mission to streamline operational processes, the company boasts years of expertise in the logistics sector. Infoplus WMS was developed to address the growing complexities that come with managing a modern warehouse.
From humble beginnings, Infoplus has expanded dramatically, aligning itself with businesses that aim to enhance their order fulfillment strategies. Its reputation rests on its ability to cater to both small startups and large, established enterprises. This versatility speaks volumes about the adaptability and scalability of the WMS.
Core Functionality
At its core, Infoplus WMS is designed to enhance operational efficacy. Here are some key functionalities worth noting:
- Inventory Management: The system allows the tracking of stock levels in real time, minimizing the risk of overselling or stock shortages.
- Order Fulfillment: Automated order processing ensures swift and accurate order picks, helping businesses meet customer demands promptly.
- Shipping Integration: Infoplus WMS supports various shipping carriers, cutting down on shipping time and errors.
- Custom Reporting: Users can generate comprehensive reports, which not only provide insights into the business but also help in making informed decisions.
In essence, Infoplus WMS offers a holistic approach to warehouse management. It enables businesses to optimize their operational flow, ensuring that they remain competitive in a landscape filled with challenges and opportunities. As companies continue to seek innovative ways to streamline logistics, systems like Infoplus WMS will be essential in paving the way forward.
"Effective warehouse management is the backbone of successful supply chain operations. With tools like Infoplus WMS, businesses can glean insights that enhance productivity and drive growth."
By understanding the significance of Infoplus WMS, businesses can not only optimize their logistics frames but also prepare themselves for future challenges. It stands as a testament to the changing dynamics of the warehouse management landscape.
Key Features of Infoplus WMS
In the realm of warehouse management systems, discerning the vital features offered by Infoplus is central to understanding its role in enhancing logistics efficiency. The system’s capabilities don't just exist in isolation; they interlink to bolster productivity and streamline operations across the board. Being tech-savvy is not merely a trend; it’s a necessity, and Infoplus stands as a beacon for businesses aiming to modernize their warehouse processes with sophistication and ease.
Inventory Management
At the heart of Infoplus WMS lies its robust inventory management feature. Businesses often grapple with keeping tabs on their stock levels, which is where this system shines. With real-time tracking, organizations can avoid the pitfalls of overstocking or stockouts.
Moreover, automated alerts notify users of low inventory, allowing timely replenishments. This negates the guesswork that often leads to either excess capital tied in products or missed sales opportunities due to unavailability. Imagine a store where shelves are always stocked without any manual checks; that’s what effective inventory management through Infoplus facilitates.
- Real-Time Visibility: Track inventory across multiple locations instantly.
- Automated Reordering: Reduces manual labor and speeds up the restocking process.
"With Infoplus WMS, you're not just monitoring inventory—you're mastering it."
Order Fulfillment Processes
The order fulfillment processes within Infoplus serve as a linchpin in the overall efficiency of warehouse operations. Every order processed not only impacts customer satisfaction but also reflects the business's operational prowess. Infoplus optimizes these processes by integrating pick, pack, and ship functionalities into a seamless workflow.
- Pick Lists: Staff can access optimized picking routes, saving time on repetitive tasks.
- Packing Automation: Automation ensures accuracy, reducing the chance of errors that can lead to returns.
This system helps cut down fulfillment times, ensuring customers receive their orders faster. It transforms what could be a chaotic juggling act into a well-organized, efficient ballet of logistics.
Reporting and Analytics
In a world where data drives decision-making, reporting and analytics features of Infoplus become indispensable tools for warehouse administrators. The system harnesses data from various operation aspects, providing insightful reports and trend analysis. For instance, managers can quickly identify which products fly off the shelves and which sit idly, adjusting their strategies accordingly.
- Customizable Dashboards: Tailor reports to focus on metrics that matter most to your operations.
- Forecasting Tools: Anticipate demand trends, enabling proactive management of stock levels.
By leveraging these analytical capabilities, businesses can pivot strategies swiftly, optimizing their inventory and fulfilling customer expectations with greater precision.
Integrations with Other Systems
Lastly, the integration capabilities of Infoplus WMS set it apart as a flexible solution that aligns with existing business processes. Compatibility with various systems, whether it's ERP software like NetSuite or e-commerce platforms such as Shopify, allows users to work within a familiar framework rather than starting from scratch.
- APIs for Custom Solutions: Create tailored applications that connect seamlessly with Infoplus.
- Cross-Platform Functionality: Ensure data consistency across different operational systems.
This adaptability means Infoplus can grow alongside businesses, ensuring long-term viability without the burden of frequent overhauls.
In summary, these key features of Infoplus WMS can radically enhance warehouse operations. They not only contribute to significant cost reductions through efficiency but also bolster accuracy and customer satisfaction. As companies navigate the complex logistics landscape, understanding these features is critical for making informed decisions that impact their bottom lines.
Benefits of Using Infoplus WMS
The Infoplus Warehouse Management System offers a range of benefits that significantly enhance warehouse operations and overall logistics management. Understanding these benefits is key for any company looking to optimize their supply chain processes. As businesses strive to meet the demands of contemporary commerce, leveraging such systems becomes not just a choice but a necessity. Let's delve into the specific advantages it can provide.
Enhanced Efficiency and Productivity
One of the standout features of Infoplus WMS is its ability to boost efficiency and productivity. This system automates various warehouse tasks, which helps in reducing human error and speeding up processes. Tasks that traditionally took a good chunk of time, like inventory tracking and order processing, can now be executed rapidly and with greater accuracy. As the saying goes, "time is money," and in the fast-paced world of logistics, every second saved in operations can lead to improved outputs.
- Streamlined Workflows: By leveraging Infoplus WMS, businesses can create more fluid workflows that eliminate bottlenecks. Imagine a warehouse where picking, packing, and shipping processes flow as smoothly as a well-rehearsed dance. That’s the goal that Infoplus WMS aims to achieve.
- Real-Time Inventory Management: Knowing exactly what's in stock and what needs replenishing can drastically reduce downtime. The system updates inventory levels in real-time, allowing teams to make swift decisions based on accurate data.
In sum, by enhancing efficiency, Infoplus WMS not only supports better day-to-day operations but also positions a business for long-term growth.

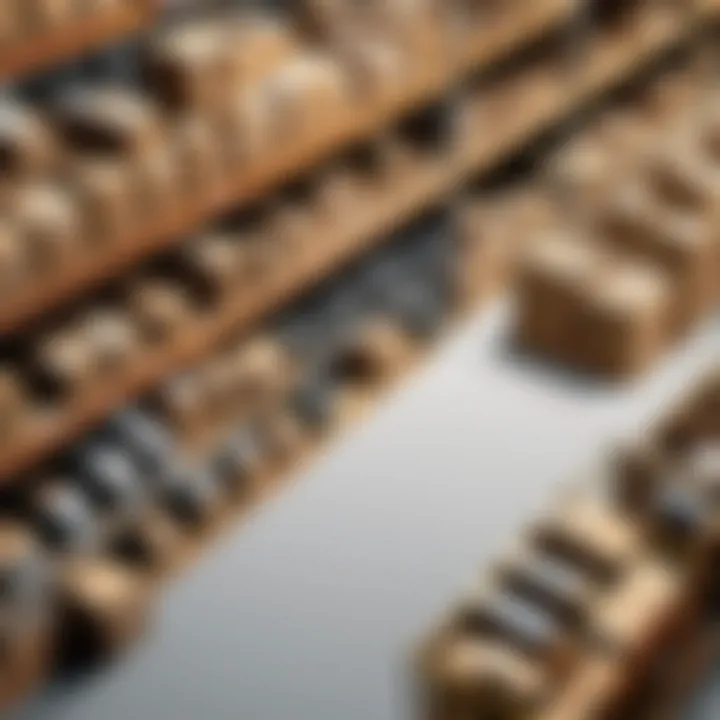
Cost Savings and Resource Management
Cost management is always top of mind for business owners. The Infoplus WMS provides ways to save money while optimizing resource usage. This isn’t just about looking at the bottom line; it’s about finding more value in every dollar spent.
- Reduced Labor Costs: Automation leads to fewer hours needed for manual tasks, which can significantly curtail labor costs. In many cases, companies find they can operate with a leaner workforce, focusing their human resources where they add the most value.
- Minimized Errors: The cost of errors—whether through mispicks, shipping mistakes, or inventory shortages—can seriously add up. Infoplus WMS offers tools that minimize these errors, thereby saving companies from added expenses.
- Better Use of Space: A good warehouse management system can also help with physical space management. By optimizing layouts, Infoplus WMS ensures that every inch of usable warehouse space contributes to overall efficiency, leading to potential reductions in overhead costs related to storage.
In short, implementing Infoplus WMS translates into tangible cost savings, making it an investment that pays off in more ways than one.
Improved Accuracy in Order Processing
Order accuracy is paramount in building customer trust and loyalty. With Infoplus WMS, errors in order processing can be significantly reduced, creating a smooth experience from start to finish.
- Automated Verification Processes: The system automatically cross-checks orders against inventory, helping catch errors before they reach the customer. This kind of technology acts like a safety net, ensuring that what gets shipped matches what was ordered.
- Clearer Communication: With better data accuracy, communication among team members improves. Everyone works from a single version of the truth, which fosters collaboration and reduces misunderstandings.
"Accuracy is crucial. In today's market, one misstep can lead to lost customers."
- Enhanced Customer Satisfaction: Finally, delivering the right product on time leads to happier customers. In a marketplace saturated with options, companies that excel in accuracy stand out, leading not just to retention but also to positive word-of-mouth.
Ultimately, by prioritizing improved accuracy in order processing, Infoplus WMS contributes to a more streamlined, reliable service that drives customer satisfaction and loyalty.
Implementation Strategies for Infoplus WMS
When it comes to deploying the Infoplus Warehouse Management System, numerous strategies come into play. Formulating a solid implementation plan is not just about gliding through the stages but an essential part of ensuring that the initial investment translates into real operational benefits. A well-thought-out approach can mitigate the customary bumps in the road that organizations often encounter during such transitions. This section sheds light on the vital components of implementing Infoplus WMS, focusing on assessing business needs, migrating data, and ongoing staff support as key elements.
Assessment of Business Needs
Understanding one's own business needs is the first step in realizing the full potential of Infoplus WMS. Initially, organizations must engage in a thorough evaluation of their current warehousing processes. This involves taking a close look at inventory levels, order processing times, and resource allocation.
- Identifying Pain Points: Engaging stakeholders through interviews or surveys can help pinpoint specific inefficiencies in the current workflow. Are there bottlenecks in order fulfillment? Is inventory tracking a constant headache? Recognizing these areas is crucial.
- Setting Clear Objectives: Establish what the organization hopes to achieve with the new system—whether it’s cutting down order handling times, enhancing accuracy, or scaling operations to meet rising demand. These objectives will guide the configuration of the WMS to align with business goals.
The outcome of this assessment should be a tailor-made blueprint. This outlines the journey ahead, making sure that the selected features of Infoplus WMS will directly tackle the identified needs.
Data Migration and Setup
Once the assessment phase is concluded, the next step involves migrating existing data into the Infoplus platform. Data migration might sound as simple as pressing a few buttons, but without proper planning, it can become a logistical nightmare.
- Data Cleansing: Before migration, ensure your data is accurate and complies with the new system's requirements. This means filtering out duplicates and correcting any errors during this phase.
- Choosing the Right Migration Tools: Infoplus often provides a set of tools or services for smoother data transfer. Utilize these resources to facilitate a fuss-free migration process.
- Testing Before Going Live: Run tests in a sandbox environment to ensure the migrated data behaves as expected. Spotting discrepancies ahead of time can save a lot of headaches.
Ultimately, this phase is about laying a solid foundation. A well-executed data migration sets the stage for system functionality, making for smoother operations as you dive into the next steps.
Training and Support for Staff
No matter how sophisticated a WMS may be, its effectiveness hinges on those who operate it daily. Crafting a robust training and support strategy for staff is non-negotiable. Often, user adoption becomes a hurdle when ample training is overlooked.
- Customized Training Programs: One-size-fits-all approaches typically fall flat. Tailoring training modules that focus on day-to-day operations should be the goal. This may involve workshops, online courses, or one-on-one sessions, depending on the complexity of the roles.
- Creating User Manuals and FAQs: These resources should be readily available for employees as they navigate the new system. Clear documentation can act as a handy reference that eases daily operations.
- Ongoing Support: Building a culture where staff feel encouraged to ask questions about the system can be beneficial. This could range from holding regular Q&A sessions to designating a point person for further guidance.
Effective implementation strategies that account for these aspects pave the way for a successful adoption of Infoplus WMS, optimizing warehouse operations and leading to long-term gains.
"The success of any software implementation lies as much in the people as in the technology."
Challenges in Using Infoplus WMS
Navigating the intricacies of the Infoplus Warehouse Management System (WMS) offers many rewards but also presents several challenges, which decision-makers must carefully ponder. Understanding these obstacles is essential for those who wish to maximize the benefits of this software. Ignoring potential pitfalls may lead to missteps that can affect overall warehouse efficiency and productivity.
The two primary challenges that seem to surface repeatedly are the integration complexities and user adoption issues. Addressing these hurdles head-on is the key for companies to reap the full rewards of using the Infoplus WMS while also ensuring their logistics operations run as smoothly as possible.
Integration Complexities
Integrating the Infoplus WMS with existing systems can often resemble piecing together a complex puzzle. While the potential for increased efficiency looms large, achieving seamless compatibility with other software—be it ERP systems like SAP or e-commerce platforms such as Shopify—can sometimes cause headaches.
- Technical Considerations: Not all systems play nice together. Sometimes, the data formats differ significantly, making data transfers a cumbersome task. Misalignment of system configurations can lead to incorrect data, which in turn can slow down or even derail operations.
- Cost Implications: Costs can add up quickly when dealing with integration. Whether it’s hiring skilled developers or investing in additional software, it’s an expense that often sneaks up on companies. Many underestimate how long the integration process might take, resulting in unforeseen financial strain.
- Time Constraints: Beyond financial factors, the time it takes to complete an integration project can hinder other vital operations. Warehouses need to remain agile; downtime, often unavoidable, can set back timelines and impact customer satisfaction.
Mark B. from Chicago shared his experience:
"When we integrated Infoplus with our inventory system, it felt like we were trying to fit a square peg into a round hole. There were too many adjustments, and it took much longer than we had anticipated."
Companies must assess their existing infrastructure and determine how Infoplus can fit within it. A well-planned integration strategy may alleviate some of the stress associated with this challenge.
User Adoption Issues
Let’s face it: implementing new software often meets resistance from staff. User adoption can be a tricky terrain to navigate, as employees might feel apprehensive about changing their workflow. The reluctance to embrace new technology can limit the potential success of Infoplus WMS and even muddy operational waters, thus undermining efficiency gains.
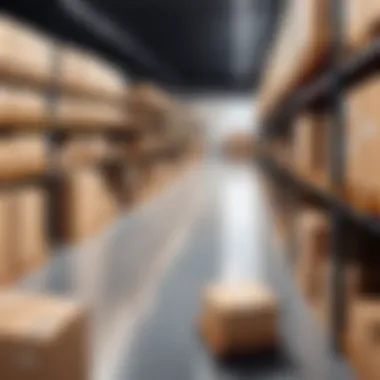
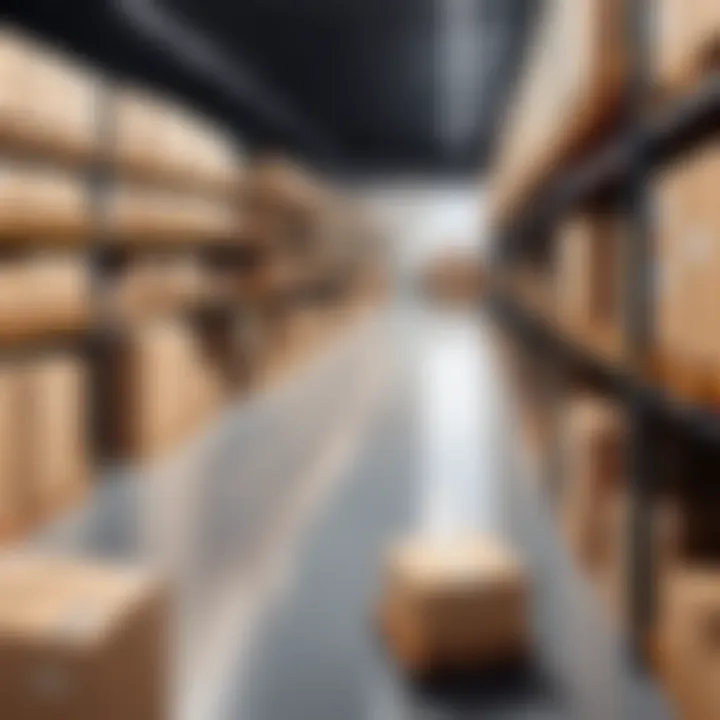
- Training Needs: It's not just about throwing a new system at users and hoping for the best. Proper training is critical. Without adequate understanding of how to utilize all the features Infoplus offers, employees may continue to rely on older, perhaps inefficient, methods of working. Companies that skimp on training often find themselves in a world of frustration.
- Cultural Barriers: Company culture plays a significant role in user acceptance. If the culture doesn't encourage learning or adaptability, there's a high chance the new system will be met with skepticism. Engagement from upper management can make a world of difference in fostering a positive attitude toward such changes.
- Support Systems: Ongoing support is another aspect to consider. Without a dedicated support team to address issues and questions, staff may feel lost. Continuous guidance can make a huge impact in ensuring employees feel confident in using the new system.
User adoption may be one of the more challenging facets of introducing Infoplus WMS, but with the right strategies and support, warehouses can navigate this hurdle.
User Experiences and Case Studies
User experiences and case studies play a critical role in understanding the practical implications of the Infoplus Warehouse Management System. Through real-world examples and narratives, businesses can glean insights about how the software performs under varying conditions and challenges. Firsthand accounts from users offer invaluable lessons that can steer new adopters in the right direction, highlighting both the capabilities of the system and potential pitfalls.
In this section, we’ll explore two prominent aspects: the successes achieved by companies using Infoplus and the lessons they’ve learned during implementation. These upticks in real-life scenarios not only depict the system's effectiveness but also echo the sentiments of professionals entrenched in logistics and supply chain management who seek authentic, candid evaluations of WMS.
Positive Outcomes and Success Stories
Many companies have reported notable enhancements in efficiency after integrating Infoplus into their operations. For instance, a medium-sized e-commerce retailer based in Ohio saw their order processing time cut by nearly 40% within the first few months of using the software. The streamlined inventory management features helped to eliminate much of the manual effort that previously slowed down operations. As a result, they could fulfill orders more swiftly and accurately, increasing customer satisfaction significantly.
Another clear success story comes from a large food distribution center in California. They faced storage issues and real-time tracking challenges due to an overwhelming number of SKUs. Post-implementation of Infoplus, they reported a marked improvement in their storage organization and inventory visibility. Staff members noted that fewer errors occurred, leading to less wasted product and a more robust bottom line.
"Transitioning to Infoplus made us not just faster but also smarter in how we handle our inventory. It felt like a game changer," quoted the Operations Manager of the distribution center.
These examples illustrate that infusing technology into warehouse operations can yield remarkable transformations. Beyond efficiency, the software also empowers businesses to adapt to market dynamics more fluidly.
Lessons Learned from Implementation
While the benefits of the Infoplus Warehouse Management System are clear, several organizations have underscored the importance of a meticulous implementation process. One major takeaway is the necessity for thorough training. A retail chain in New York noted that their initial struggles stemmed largely from staff not being adequately trained on the new system. This led to frustration and slow adoption until they committed to a robust training program.
Additionally, businesses learned the significance of customization. A medical supply distributor realized early on that while the out-of-the-box features of Infoplus were impressive, tailoring the system to fit their unique needs resulted in a smoother workflow. Adapting the software to their specific business operations not only aided in maximizing efficiency but also in aligning processes with regulatory standards in the healthcare sector.
As for data, companies have discovered that a well-organized data migration is paramount. One electronics retailer reported hiccups during their transition because historical data were poorly structured. Ensuring data integrity and a smooth transfer became their top priority during subsequent implementations, saving them headaches down the road.
In summary, these experiences reveal key insights that can guide future users. The take-home message is that while the Infoplus WMS is a powerful tool, its true potential is unlocked through thoughtful implementation and ongoing adjustments based on user feedback. Engaging with the user community and learning from their journeys can pave the way for newly onboarded businesses.
Future Trends in Warehouse Management Systems
As industries evolve, so do their operations. Warehouse Management Systems (WMS) are not left behind in this race against time. Future trends in WMS represent crucial components for those looking to stay competitive, particularly in a time where supply chains can turn on a dime. This isn't just another buzzword; it's about understanding the shifts on the horizon that can impact warehouse efficiency and responsiveness. By grasping these trends, decision-makers can make more informed choices on how to enhance their logistics processes.
Technological Advancements
In the realm of warehouse management, technology is the ace up the sleeve. As advancements such as Artificial Intelligence (AI), Internet of Things (IoT), and automation continue to develop, they radically reshape operations. For instance, implementing AI can significantly improve inventory forecasting, helping to predict stock requirements based on historical data and market trends.
Moreover, IoT devices can provide real-time tracking of inventory and shipments. Imagine being able to know exactly where every item in your warehouse is located, down to the last box. This data can facilitate more efficient routing within the warehouse, ensuring that orders are picked and packed in a timely manner.
Additionally, robotic automation is becoming quite prevalent in modern warehouses. These machines are designed to handle heavy lifting and repetitive tasks which not only saves time but also can minimize human error. As businesses fully leverage these technological advancements, they note benefits such as:
- Greater operational efficiency
- Enhanced accuracy in order fulfillment
- Improved visibility across supply chains
"Adopting new technologies today helps prepare for tomorrow's challenges in warehouse management."
Shifts in Consumer Behavior
Now, it’s not just technology that’s changing the game, but also the way consumers behave. With the rise of e-commerce, expectations regarding delivery times and order accuracy have escalated. Customers nowadays expect fast, sometimes same-day delivery, which places immense pressure on warehouses to streamline their processes. This shift means that responsiveness becomes a top priority.
Besides speed, personalization is another significant factor. Shoppers want to feel valued; they appreciate customized experiences. Consequently, WMS must adapt to these preferences by enabling personalized customer interactions through features like tailored order tracking and recommendation systems.
To summarize the shifts in consumer behavior, we're seeing:
- High demand for quicker delivery times
- Increased importance on personalization
- A desire for greater transparency in the supply chain
Staying vigilant about these trends can help warehouses maintain a competitive edge.
Finale
The conclusion serves as a vital component of this article, summarizing the key insights and delivering essential considerations about the Infoplus Warehouse Management System (WMS). The overall landscape of supply chain logistics can be quite complex, and the ability to distill this information into digestible points is crucial for decision-makers. It’s not just about understanding the technical aspects of the WMS, but also grasping how it can lead to enhanced operational efficiency, reduced costs, and improved order accuracy.
In determining the benefits of adopting Infoplus WMS, one must contemplate multiple elements: from its robust inventory management features to seamless integrations with other systems. Each aspect offers unique advantages that collectively elevate warehouse operations. Companies leveraging these capabilities can expect not only streamlined processes but also a significant competitive edge in the marketplace.
Moreover, engaging with the user experiences and case studies mentioned previously enriches the perspective on practical outcomes and real-world application of the system. Such insights can guide future planning and strategic implementation.
As the industry evolves, staying aware of new trends and technological advancements may provide opportunities to further optimize the capabilities of Infoplus WMS. Therefore, the reflections and insights gathered from this discussion are not just about the present state of the system but also the continuous journey towards harnessing its full potential in the dynamic world of logistics.
Recap of Key Insights
- Core Functionality: Infoplus WMS is grounded in solid inventory management and order fulfillment processes that adapt to the scaling needs of businesses.
- Integration: Its ability to integrate with various other software solutions enhances its functionality, enabling businesses to maintain a cohesive technological ecosystem.
- User Feedback: Positive user outcomes highlight the practical benefits realized by those who have implemented the system, further reinforcing its value.
- Implementation Strategies: Proper assessment of business needs and thorough training for staff are essential steps in the successful adoption of the WMS.
- Future Vision: Keeping an eye on emerging trends and technological shifts is critical for ongoing optimization and improvement.
Final Thoughts on Infoplus WMS
In closing, the Infoplus Warehouse Management System emerges as a noteworthy player in the realm of logistics and supply chain management. For the tech-savvy audience, particularly IT professionals and business owners, it provides not just tools but a strategic avenue for enhancing operational efficiency.
Having discussed its various features, benefits, and potential hurdles, it is imperative to recognize that the system’s effectiveness will hinge on thoughtful implementation and continuous adaptation to shifting business landscapes. The quality of the data you feed into it, the willingness of staff to embrace change, and the foresight of leaders to leverage technological advancements will collectively dictate success. It’s clear that as logistics evolve, so too must the systems we use to manage them.