Detailed Insights into Inventory Management Systems
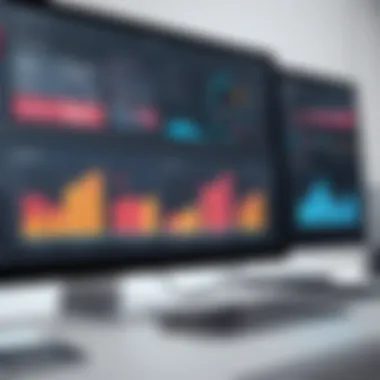
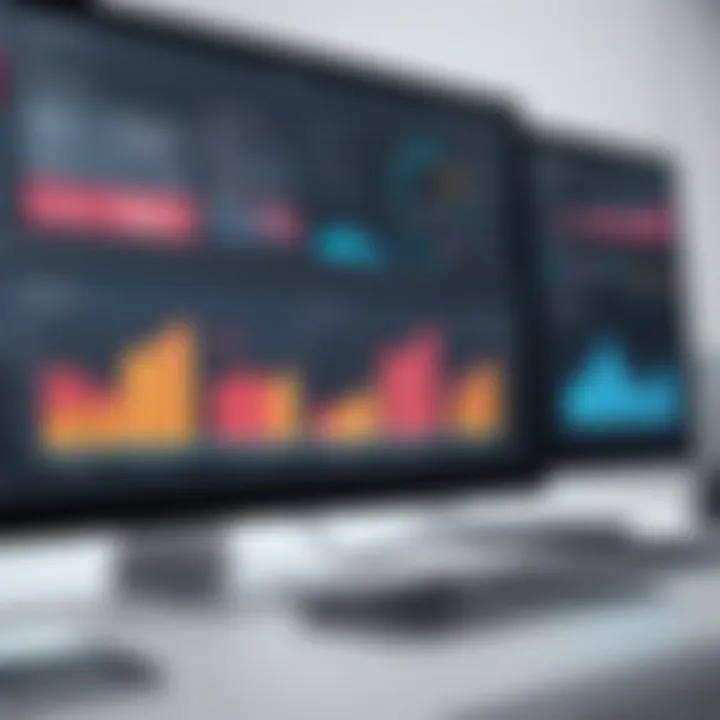
Intro
In the bustling world of modern business, managing inventory effectively is paramount. Companies, big or small, face the challenge of keeping track of products, anticipating demand, and maintaining optimal stock levels. The intricacies of inventory management can be quite a puzzle, especially with the avalanche of options that come with technology today. Understanding the available systems helps businesses not just survive, but thrive.
An accurate overview of inventory management systems provides clarity on how these tools work. From automating the ordering process to generating insights through data analytics, these systems play a crucial role in every operation, regardless of the sector.
For instance, a boutique clothing store relies heavily on inventory systems to manage seasonal stock changes effectively. This is not just about knowing what you have on hand; it's about making decisions that drive profitability. A warehouse dealing in bulk goods, on the other hand, may focus on tracking items through complex supply chains and ensuring efficient turnovers.
Let’s dive into the features that distinguish these systems and see how they can meet various needs, starting with a closer look at the specific functionalities they offer.
Understanding Inventory Management Systems
Inventory management systems play a pivotal role in the smooth operation of businesses. They are essential tools that aid companies in controlling their stock, preventing overstock and stockouts, and ultimately ensuring customer satisfaction. As enterprises grow, the complexity of inventory management rises. Therefore, understanding these systems is key to navigating the modern business landscape effectively.
Definition and Purpose
At its core, an inventory management system is a set of processes and tools that help businesses track and manage their inventory. This includes everything from raw materials to finished goods. The primary purpose of such systems is to ensure that the right amount of products is available at the right time. They incorporate various functions such as tracking stock levels, orders, sales, and deliveries.
Without a robust inventory management system, companies may find themselves navigating treacherous waters. Consider a retailer who does not know how much stock they have on hand, as they rely on manual methods. The risk of either running out of an essential product or holding too much unsold inventory is high, both resulting in poor customer experience and financial losses. Thus, the definition is not just a technical term; it encapsulates a fundamental aspect of operational efficiency.
Importance in Business
The importance of inventory management systems in business cannot be overstated.
- Cost Efficiency: Effective inventory management helps reduce costs associated with excess stock and storage. When companies can predict demand accurately, they can avoid tying up cash in unsold goods.
- Informed Decision-Making: Accurate data provided by these systems allows business leaders to make informed decisions quickly. For instance, if there is a sudden spike in demand during a holiday season, a good inventory system will alert the management to adjust purchase orders in time.
- Enhanced Customer Satisfaction: Customers expect products to be available when they need them. A well-managed inventory system ensures that desired items are always in stock, improving the chances of repeated business.
- Regulatory Compliance: In industries such as food or pharma, keeping track of inventory is a regulatory necessity. An effective system helps businesses comply with these regulations, avoiding penalties and ensuring safety.
"In today's fast-paced market, a well-organized inventory management system is not just nice to have; it’s a necessity for survival."
Understanding these elements is crucial for any business aiming to thrive in a competitive environment. From large corporations to small startups, the benefits of implementing an inventory management system resonate across all sectors.
Key Features of Inventory Management Systems
The realm of inventory management is a critical aspect for any business. A robust inventory management system holds the potential to streamline operations, reduce costs, and enhance customer satisfaction. When assessing inventory management solutions, it's vital to focus on specific key features, which are indispensable for today's tech-savvy enterprises. The importance of these features extends beyond mere functionality; they can mean the difference between a well-oiled operation and a chaotic mess of stock. Here's a breakdown of the major features you'll encounter.
Real-Time Tracking
In a world where every second counts, real-time tracking stands as a cornerstone of effective inventory management. This feature enables businesses to monitor stock levels, movements, and status instantaneously. Imagine walking into a warehouse where you can view the exact quantity of each item without rummaging through piles of paperwork. That's the power of real-time tracking.
The benefits include:
- Increased Accuracy: Minimizing human error that often plagues manual tracking methods.
- Enhanced Decision Making: Timely data empowers managers to make informed decisions about procurement and sales strategies.
- Improved Customer Service: With current information, businesses can provide accurate updates to customers about stock availability, preventing frustrating backorders.
Many of the leading inventory management systems incorporate advanced barcoding and RFID technologies to facilitate this kind of tracking. These technologies not only increase speed but also ensure precision when it comes to managing stock.
Automated Reordering
Next up is automated reordering. Consider this: Running out of a popular product can lead to lost sales, while overstocking can tie up capital unnecessarily. Automated reordering addresses this delicate balance by setting predefined thresholds that trigger new orders when stock levels fall below a certain point.
Here's why this feature is crucial:
- Efficiency: Saves time and reduces the need for manual checks on inventory levels.
- Cost Management: Helps preserve cash flow by ensuring that purchases occur only when needed. This reduces costs related to excess inventory.
- Protection Against Stockouts: Ensures that popular items are always available, which is crucial for customer retention and satisfaction.
Implementing automated reordering features effectively can position businesses to respond swiftly to market demands while minimizing risks associated with inventory mismanagement.
Reporting and Analytics
Finally, reporting and analytics are vital for understanding the inner workings of inventory management. Advanced systems go well beyond basic reports, delving into meaningful data that informs strategic decisions. With analytics, businesses can scrutinize trends, demand forecasting, and sales patterns, leading to actionable insights.
Consider the advantages:
- Data-Driven Decisions: Equip managers with the necessary insights to shape purchasing strategies or shift inventory focus based on emerging trends.
- Performance Metrics: Set KPIs and measure success regarding turnover rates, stock levels, and overall efficiency.
- Enhanced Forecasting: Utilize historical data to predict future trends, allowing for more accurate planning.
In an age where data is king, having powerful reporting tools means businesses can stay ahead of the curve, adapting to changes in consumer behavior with agility.
"The right inventory management system isn’t just a luxury; it’s key to maintaining competitiveness in a rapidly evolving marketplace."
In summary, the key features of inventory management systems—real-time tracking, automated reordering, and reporting and analytics—are integral to successful inventory strategies. By honing in on these operations, businesses can ensure streamlined processes, enhanced accuracy, and ultimately, improved profitability.
Types of Inventory Management Systems
Inventory management systems come in various flavors, each equipped to address the distinct needs of businesses operating in diverse environments. Understanding the differences among these systems is essential for organizations that strive for operational efficiency and effectiveness. Choosing the right type can significantly impact the management of stock, reduce carrying costs, and enhance order fulfillment processes. Unlike a one-size-fits-all solution, the variety of inventory management systems reflects the complexities found in modern business operations. Here’s a closer look at the three main types: Cloud-Based Solutions, On-Premise Software, and Hybrid Systems.
Cloud-Based Solutions
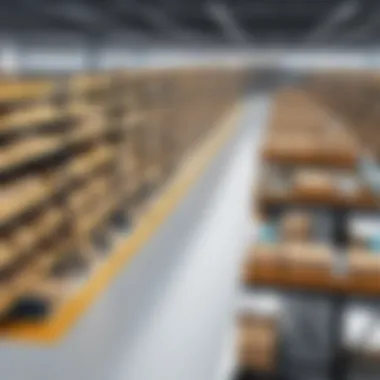
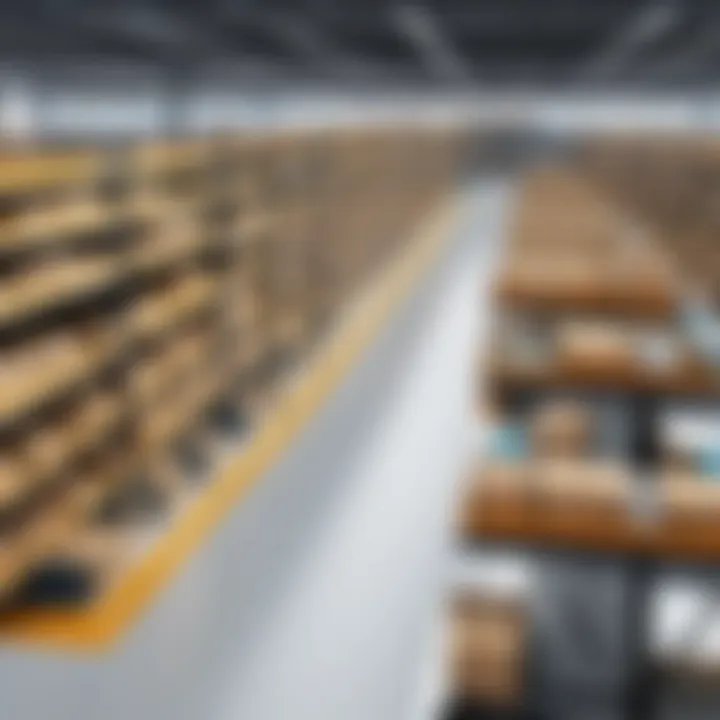
Cloud-based inventory management systems are gaining traction for several reasons. They allow users to access real-time data from any location and on any device connected to the internet. This flexibility makes it easy to manage stock across multiple locations and collaborate with team members regardless of physical barriers. Businesses can also benefit from automatic updates and the ability to scale according to their needs, so when growth happens—in terms of products or sales—these systems adapt without significant manual intervention.
Key considerations for cloud-based systems include:
- Cost-Effectiveness: Generally, they operate on a subscription model, reducing upfront costs and maintaining predictable expenses.
- Ease of Use: Many cloud solutions feature user-friendly interfaces, making it easier for staff who may not have extensive technical know-how to perform their tasks efficiently.
- Security and Compliance: Providers often handle security updates and data backups, reducing the burden on internal IT teams.
However, it’s worth noting potential drawbacks, such as reliance on internet connectivity and possible concerns around data privacy.
On-Premise Software
On-premise inventory management systems offer a more traditional approach and are hosted on the company’s own servers. For organizations that prioritize control over their data and prefer not to depend on third-party services, this option may be appealing. On-premise solutions tend to provide comprehensive features tailored to specific industries, making them suitable for businesses with unique inventory management needs.
Advantages of using on-premise software include:
- Data Control: Companies have full control over their data security, making it easier to comply with strict regulations.
- Customization Options: They can be tailored extensively to meet specific business processes and requirements, from customizing workflows to creating specialized reports.
- Integration: On-premise solutions can integrate directly with existing systems without the limitations sometimes faced by cloud applications.
Nevertheless, they often come with hefty upfront licensing fees and ongoing maintenance costs. Companies must also manage their backup and disaster recovery plans, potentially adding complexity.
Hybrid Systems
Hybrid systems combine elements of both cloud-based and on-premise solutions. This approach is especially useful for organizations looking to balance flexibility with data security. Hybrid systems allow businesses to maintain sensitive data locally while leveraging cloud capabilities for less critical information or processes.
Some benefits of hybrid systems include:
- Flexibility: Firms can choose which data to store on the cloud while keeping other information secured in-house, thus maintaining tight control where necessary.
- Scalability: They can scale storage and processing in a manner that suits operational demands, which effectively optimizes costs.
- Advanced Capabilities: Hybrid systems can often utilize the strengths of both deployment models, leading to reduced latency in accessing vital data while enhancing collaborative opportunities.
Nonetheless, hybrid systems can introduce complexity, requiring careful management to ensure data is synchronized correctly and security measures are consistently applied.
Overall, understanding the types of inventory management systems helps decision-makers tailor their choices to fit their business model better. Investing effort in this decision-making process can translate into higher efficiency and reduced operational hiccups.
Examples of Inventory Management Systems
Examining examples of inventory management systems is crucial for understanding how these tools cater to diverse business needs. Each system reveals unique elements, benefits, and considerations that can significantly impact operational efficiency. With the variety of options available, businesses can find the right fit for their specific requirements, whether they are in retail, manufacturing, or distribution. Identifying the strengths and weaknesses of these systems aids decision-makers in choosing the most effective solution.
TradeGecko (Now QuickBooks Commerce)
Core Features
Core features of TradeGecko, now part of QuickBooks Commerce, include user-friendly inventory management capabilities paired with powerful order processing functions. This system shines with its real-time updates and seamless integration with various sales channels. A key characteristic of TradeGecko is its straightforward interface, making it accessible for businesses regardless of their technical proficiency. One unique feature is the ability to manage multiple locations from one platform, which significantly benefits growing businesses needing centralized control.
However, some users have noted that advanced functionality may require additional training, posing a potential drawback for smaller teams.
Target Users
As for target users, TradeGecko appeals mainly to small to medium-sized businesses that are scaling operations. It supports various retail and ecommerce sectors, making it a popular solution for those needing a simple yet comprehensive inventory tool. A distinctive feature of TradeGecko is its tailored support for different languages, allowing businesses with an international reach to manage inventory effectively.
That said, some larger enterprises may find TradeGecko insufficient in meeting complex needs, as it lacks certain advanced features found in high-end systems.
Pricing Overview
Pricing Overview offers tiered subscription plans that cater to businesses at different stages. The flexibility in pricing makes it a beneficial option for startups and established companies alike. A large selling point is their pay-as-you-go model, allowing businesses to adjust services based on their growth without heavy upfront costs.
On the flip side, as businesses scale and add more features, pricing can climb steeply, leading to a potentially significant investment in the long run.
Zoho Inventory
Key Functionalities
Zoho Inventory's key functionalities encompass order management, multi-channel selling, and automated stock updates. The system stands out for its intuitive dashboard, which grants users insights at a glance. One of its key characteristics is the capability to manage inventory across various sales platforms through a single interface, streamlining the process for users. An interesting feature is the integration with Zoho's other applications, enhancing business functions in accounting and customer relationship management.
Despite its strengths, some users have expressed difficulty in the learning curve related to advanced features, which could inhibit rapid onboarding for new users.
Integrations
The integrations that Zoho Inventory offers are expansive, including compatibility with platforms such as Shopify, Amazon, and eBay. The ability to synchronize with existing tools contributes significantly to its effectiveness. A notable aspect of this integration is its real-time sync, ensuring no discrepancies arise during transactions.
However, while integration is extensive, customizing connections with lesser-known platforms can sometimes be a challenge, presenting potential complications for niche businesses.
Pricing Plans
Pricing plans for Zoho Inventory cater to a vast array of businesses, highlighting their commitment to accessibility. It provides a free tier for startups and scalable tiered options as business needs grow. The greatest advantage is the competitive pricing compared to other solutions, providing a cost-effective inventory management option.
On the downside, some advanced features are only available at higher tiers, which could limit functionality for organizations with tighter budgets.
Cin7
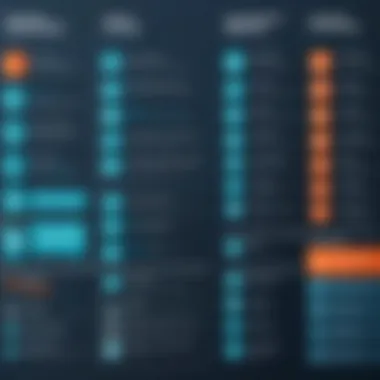
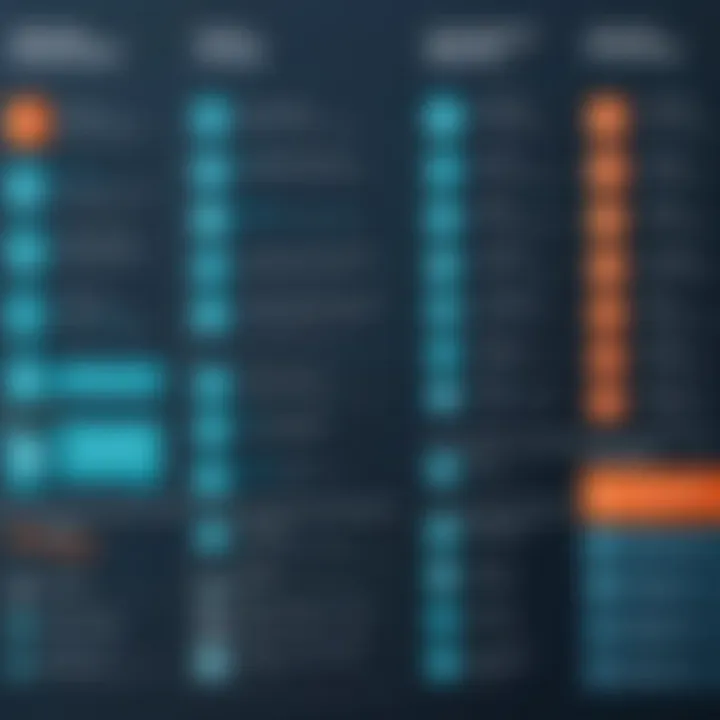
Unique Selling Points
Cin7's unique selling points lie in its all-in-one purchasing and inventory management system tailored for various industries. The intuitive design allows businesses to track stock across multiple channels seamlessly. One of its key characteristics is the integration of point-of-sale features within the inventory management tool, making it compelling for retail environments. A standout feature of Cin7 is its built-in third-party logistics (3PL) capabilities, which empowers businesses to streamline order fulfillment processes.
However, integration with some established ecommerce platforms has been reported as problematic, which can inhibit its usage in certain cases.
Business Suitability
Cin7 is particularly suitable for businesses operating in retail and wholesale, looking for comprehensive inventory management solutions. Its flexibility to adapt to diverse operational needs is a primary advantage. The software supports various product types, from serialized to bulk items, allowing for intricate stock management.
Some users might find the extensive features overwhelming, especially those in smaller businesses that require less complexity.
Cost Structure
Cin7's cost structure is relatively flexible, accommodating both smaller retailers and larger wholesalers. It has competitive pricing compared to traditional inventory systems. A notable aspect is that it includes multiple features within the pricing tier, combining functionalities that usually require separate tools.
Nevertheless, as businesses grow or require additional functionalities, costs can escalate fast, which some users may find discouraging.
SAP Business One
Enterprise Applications
SAP Business One offers a powerful suite of enterprise applications tailored for scalability and comprehensive inventory management. Its integration across various business functions—accounting, sales, and operations—is crucial for large enterprises seeking cohesion among departments. A prominent feature is the predictive analytics functionality that assists businesses in making informed decisions based on real-time data.
The downside, however, is the complex setup process, which might deter smaller companies from adopting it.
Customization Options
Customization options of SAP Business One provide businesses with the ability to tailor the software to their specific needs. This adaptable nature allows enterprises to modify reports, dashboards, and workflows to suit their operational requirements. A key strength here is the visibility it provides for stakeholders in tracking metrics relevant to their roles and performance.
However, this flexibility comes at a higher cost of implementation and management, potentially making it a less feasible option for smaller organizations.
Licensing Costs
The licensing costs for SAP Business One reflect its comprehensive features. While it may seem higher initially, many users find that the return on investment shines through as it covers multiple functional areas in one solution. A notable characteristic of the licensing structure is its capability to scale, allowing businesses to add users and modules as their needs evolve.
Nonetheless, for startups or small businesses, the initial outlay can be prohibitive, putting it out of reach for companies with limited resources.
Fishbowl Inventory
Features and Benefits
Fishbowl Inventory showcases a variety of features that provide flexibility and control in managing stock. One key benefit is the integration with QuickBooks, which many finance departments are familiar with. Users also highlight the comprehensive manufacturing management capabilities available, which add significant value in sectors that rely heavily on production.
Conversely, the system's complexity can introduce a steep learning curve, especially for those unaccustomed to more advanced inventory practices.
Industry Focus
Fishbowl Inventory is particularly focused on manufacturing and warehousing markets. Its strong capabilities in managing raw materials and finished goods make it a go-to choice for manufacturing businesses. The highlight here is the tailored features that support multiple warehouse locations, improving inventory accuracy.
That said, its specific focus may make it less beneficial for retailers who don’t have complex inventory workflows.
Implementation Process
The implementation process of Fishbowl can require significant time and resources. This aspect is vital for users to consider, as adequate training and adjustment time is crucial for seamless operation. The standout feature of Fishbowl is its community support, which provides resources and services to help businesses during setup.
Yet, a lengthy implementation can cause disruption in operations, particularly for smaller entities with limited capacity to manage transitions.
Comparing Inventory Management Systems
When it comes to inventory management, the choices can feel overwhelming. This section digs into comparing inventory management systems, a pivotal aspect for any organization looking to streamline their processes and make informed decisions. Understanding the differences between systems is crucial because each comes with its unique blend of features and capabilities. Without this knowledge, businesses risk investing in a solution that doesn’t suit their specific needs or sizes.
A well-executed comparison allows decision-makers to highlight specific elements such as:
- Functionality
- Costs
- User experience
- Customer support options
Ultimately, choosing the right inventory management system significantly affects overall operational efficiency, which directly translates to improved financial performance.
"The right tools can separate the wheat from the chaff in inventory management; the wrong ones can turn a fine-tuned machine into a jumbled mess."
Evaluating Features Against Needs
Evaluating features against operational needs is like fitting pieces of a puzzle together. Each business has its own workflow. Therefore, understanding the essential features that align with organizational goals becomes essential. Systems may offer capabilities like tracking stock levels, managing supplier relations, and integrating with e-commerce platforms, but what matches your exact scenario?
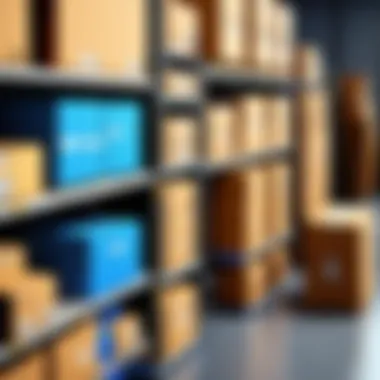
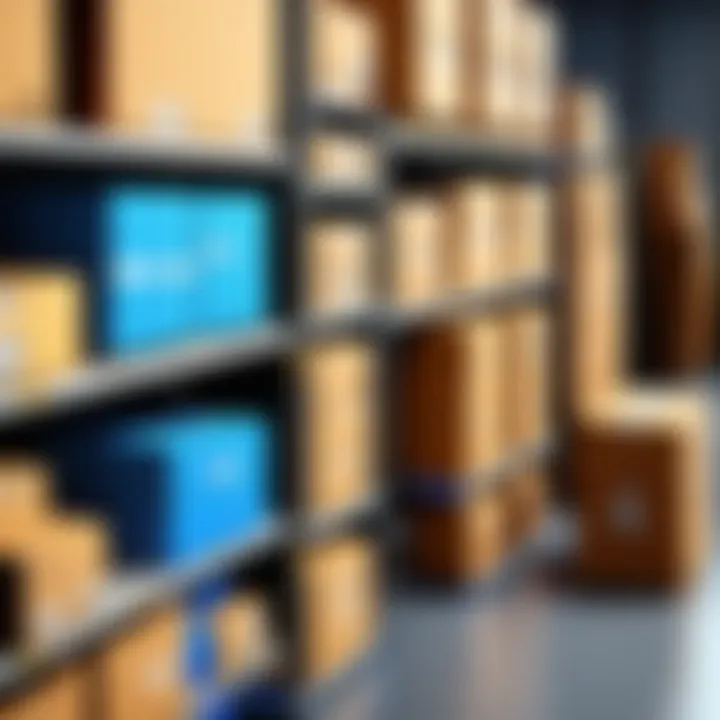
Here are some critical considerations during the evaluation process:
- Scalability: Can the system grow as your requirements expand?
- Customization: Does it allow adaptations specific to your industry?
- Automation: Are repetitive tasks automated to enhance efficiency?
By aligning features to actual needs, organizations can avoid the trap of overpaying for unnecessary functionalities or, worse, facing inadequacies that could hinder performance later on.
Cost vs. Functionality
Next up is the age-old tussle of cost versus functionality. This can be particularly tricky because the balance between what you pay and what you get can vary greatly among inventory management systems. A high price tag doesn’t always equate to superior features, nor does a budget-friendly option mean you’ll be left without essential tools.
Several factors contribute to assessing the cost versus functionality:
- Initial setup fees: Some systems require upfront investments.
- Subscription models: Recurring costs can impact long-term budgeting.
- Hidden costs: Many systems charge for support or custom features later down the line.
Determining a clear ROI based on the functionalities you truly need against the total expenditure can be a game changer.
User Experience and Support
The final piece of our comparison puzzle is user experience and support. A user-friendly interface can make the difference between effective inventory management and a frustrating process that drains resources. User experience isn’t just about aesthetics; it covers intuitiveness and ease of navigation. Training staff to use a complicated system can be time-consuming and costly.
When evaluating user experience, some key aspects to look for include:
- Intuitive design: Is the layout logical and easy to follow?
- Accessibility: Can users access the system from various devices?
- Customer Support: Is help readily available when issues occur?
Support offerings can also significantly impact operational continuity. Having a support team that understands the intricacies of inventory management can make a world of difference in resolving issues quickly and effectively.
By focusing on user experience and support, businesses ensure they choose a system that enhances rather than complicates their inventory management processes.
Industry-Specific Considerations
Understanding how inventory management systems are tailored to various industries is crucial. Different sectors have unique needs and challenges which influence the functionalities they require from these systems. The right inventory management solutions not only optimize operations but also reflect the operational priorities of different industries, ensuring efficiency, compliance, and overall success.
Retail
In retail, inventory management is not just about keeping stock; it's about enhancing the customer experience and managing a dynamic supply chain. Real-time data access is a must here because customers expect products to be available when they want them. Retailers often face seasonal trends and ever-changing consumer preferences, so having an agile inventory system is vital.
For instance, a local boutique might utilize a cloud-based inventory management system, enabling them to track sales across multiple channels and automatically adjust stock levels. This can help prevent both overstock situations and missed sales opportunities—all while minimizing unnecessary costs. Moreover, tools that offer integrated e-commerce solutions can allow retailers to streamline online and offline operations.
Manufacturing
Manufacturing environments often require more complex inventory management strategies due to the need for raw materials and finished goods management. Effective systems help businesses manage just-in-time inventory practices, reducing waste and ensuring that production operates smoothly. Here, the spotlight is on automated reordering to avoid production delays—after all, a halted assembly line can cost a pretty penny.
An example is a company producing automotive parts. With a strong inventory management system, they can keep track of raw material supplies, monitor production levels, and adjust orders almost instantaneously when supplies run low. This deeper level of integration between different production stages leads to cost savings and improved efficiency, ultimately increasing competitive advantage.
Wholesale and Distribution
In the world of wholesale and distribution, the challenge lies in handling large volumes of inventory across multiple locations. Inventory management systems designed for this sector must manage not just the stock itself but also the intricate logistics of moving products between warehouses and the end customers. Data analytics becomes indispensable here, enabling businesses to forecast demand accurately and streamline operations.
Consider a distributor that manages several brands of consumer goods. With a robust inventory system, they can analyze past sales trends, upcoming seasonal variations, and even supplier lead times. This foresight allows them to make smart decisions about stock levels and logistics, which translates into efficient operations and higher customer satisfaction.
"Effective inventory management is the backbone of any successful wholesale operation, bridging the gap between procurement and customer satisfaction.”
Future Trends in Inventory Management
The landscape of inventory management is shifting rapidly, driven by technological advancements and evolving consumer expectations. As businesses strive to stay ahead, understanding future trends is crucial for maintaining competitive advantage. By embracing new methodologies and technologies, organizations can optimize their operations, reduce costs, and enhance customer satisfaction. In this section, we will explore three key trends shaping the future of inventory management: Automation and AI Integration, Sustainability Practices, and Data Analytics and Insights.
Automation and AI Integration
Automation has been a game changer in many industries, and inventory management is no exception. The integration of Artificial Intelligence (AI) into inventory systems brings a host of benefits that elevate operational efficiency. For instance, automated ordering systems can predict inventory needs based on historical data and market trends, thus reducing excess stock and minimizing stockouts.
"AI helps businesses stay lean by ensuring that products are available just in time, rather than overstocking."
Moreover, AI can facilitate smarter demand forecasting. This predictive analysis assists firms in understanding customer behavior, leading to more accurate supply levels that correlate with market demands. It's like having a crystal ball that aids purchasing managers in making fact-based decisions.
- Streamlined operations through automation.
- Enhanced forecasting abilities.
- Reduction in human error.
Sustainability Practices
Sustainability is no longer just a buzzword; it's an essential practice that influences inventory management strategies. Companies are increasingly focusing on how their inventory practices affect the environment. This shift is spurred by consumer demands for eco-friendly options and increasing regulations around sustainability.
Organizations are turning to greener processes in their sourcing, warehousing, and distribution practices. This might involve using biodegradable packaging, optimizing route logistics to lower carbon emissions, or collaborating with suppliers who adopt sustainable practices. Implementing these changes not only enhances brand reputation but can also lead to significant cost savings in the long-term, as energy-efficient operations are typically cheaper to maintain.
- Adoption of sustainable sourcing methods.
- Eco-friendly packaging solutions.
- Optimization of logistics for carbon footprint reduction.
Data Analytics and Insights
With the advent of big data, businesses have access to unprecedented amounts of information. Using data analytics tools, firms can unearth insights that drive smarter inventory strategies. Whether it’s identifying slow-moving items or analyzing seasonal trends, data allows for more precise decision-making.
For example, businesses can leverage customer purchase patterns to refine their inventory selection. Knowing which products are most popular during specific times can enhance stock positioning, enabling quicker responses to market demands.
- Key performance indicators (KPIs) inform decision-making.
- Real-time data facilitates agility in inventory adjustments.
- Better understanding of market trends through analytics.