In-Depth Examination of Warehouse Ordering Systems
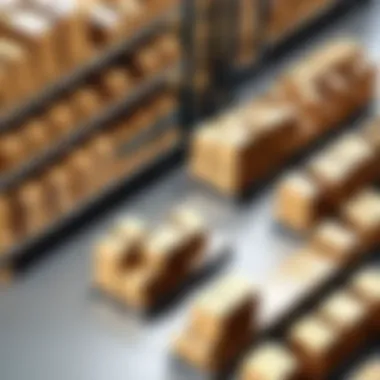
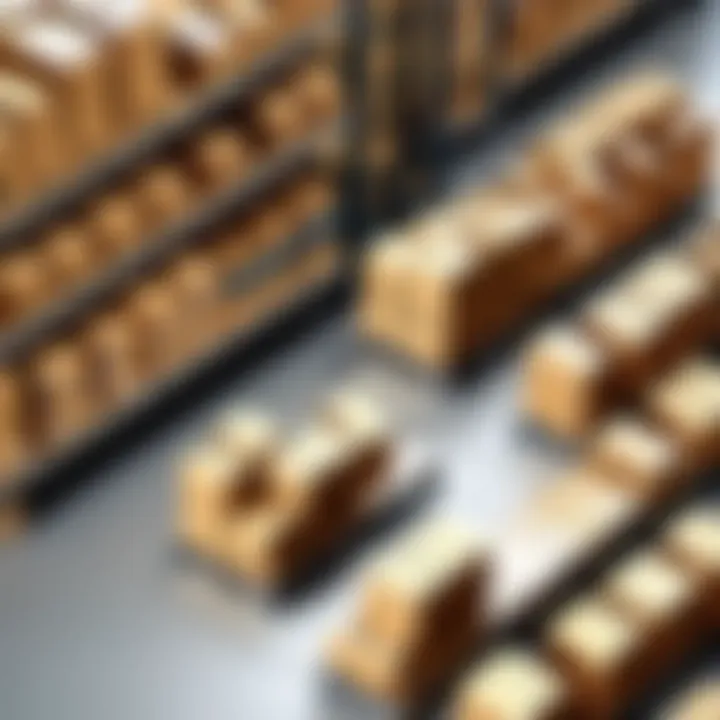
Intro
In the rapidly evolving landscape of logistics and supply chain management, warehouse ordering systems play a crucial role. These systems streamline the process of managing inventory, processing orders, and optimizing resource allocation. A well-designed warehouse ordering system can lead to significant improvements in efficiency and accuracy. This analysis delves into the core features and functionalities of such systems, examining their advantages, drawbacks, and integration capabilities. It also addresses critical considerations for selection and implementation, paving the way for better decision-making.
Features Overview
Warehouse ordering systems possess several key features that enhance operational efficiency.
Key Functionalities
The central functionalities of a warehouse ordering system may include:
- Inventory Management: Effectively tracking stock levels, orders, sales, and deliveries. This helps prevent overstocking and stockouts.
- Order Processing: Automating the steps from order receipt to fulfillment. This minimizes human error and ensures faster delivery times.
- Real-Time Tracking: Providing live updates on inventory and order status. This transparency enhances communication among stakeholders.
- Reporting and Analytics: Generating relevant data insights for better strategic planning and forecasting. This helps in making informed business decisions.
Integration Capabilities
Integration capabilities are vital for seamless operations. A warehouse ordering system should ideally integrate with:
- Enterprise Resource Planning (ERP) Systems: To synchronize data between different business functions.
- Customer Relationship Management (CRM) Software: To provide sales teams with up-to-date customer order information.
- Shipping Platforms: To optimize shipping processes and logistics.
Pros and Cons
Every technology comes with its pros and cons, and warehouse ordering systems are no exception.
Advantages
The benefits of implementing a warehouse ordering system are numerous:
- Increased Efficiency: Automation speeds up order processing and inventory management tasks.
- Lower Operational Costs: Optimized resource allocation can reduce waste and associated costs.
- Improved Accuracy: Enhanced data management minimizes errors in orders and inventory tracking.
Disadvantages
However, there are challenges associated with these systems:
- Initial Costs: High upfront costs for software and implementation can be a barrier for some businesses.
- Complexity: System complexity may require dedicated IT support for maintenance and troubleshooting.
- Training Needs: Employees need training to adapt to new systems, which might affect productivity initially.
In summary, warehouse ordering systems offer significant potential for enhancing operational efficiency. By understanding their features, advantages, and challenges, decision-makers can make informed choices that align with their business goals.
Preamble to Warehouse Ordering Systems
The efficiency of a warehouse ordering system is pivotal to modern supply chain management. It serves as a vital framework that coordinates various logistical elements to ensure smooth operations. The significance of warehouse ordering systems extends beyond mere order placement; they enhance inventory control, streamline shipping processes, and facilitate effective data reporting. Each of these factors contributes to overall operational efficiency.
Definition of Warehouse Ordering Systems
A warehouse ordering system is a software solution designed to manage and automate the process of order fulfillment within a warehouse environment. This includes receiving, processing, and delivering products to customers or other business units. The system integrates various functions such as order management, inventory tracking, and shipping coordination into a single platform. With these capabilities, businesses can minimize delays, reduce errors, and ensure that the right products reach the right destination on time.
Importance in Supply Chain Management
In the realm of supply chain management, warehouse ordering systems play an instrumental role. Here are some key points underscoring their importance:
- Operational Efficiency: An effective warehouse ordering system increases productivity by reducing the time taken to process orders. This directly impacts customer satisfaction and retention.
- Accuracy: The system improves accuracy in order fulfillment, which is crucial for maintaining inventory integrity. This helps in lowering the costs associated with returns and replacements.
- Real-Time Data: It provides real-time data, allowing businesses to make informed decisions quickly. Managers can track inventory levels and order status, leading to better resource allocation.
- Scalability: As businesses grow, warehouse ordering systems can easily scale to meet increased demand without significant changes to existing processes.
"Incorporating a warehouse ordering system is not just an enhancement; it can be seen as a necessity for businesses aiming for sustainable growth in competitive markets."
Core Functions of Warehouse Ordering Systems
Understanding the core functions of warehouse ordering systems is crucial for any business engaged in or reliant on the supply chain. These systems ensure that processes run smoothly and efficiently, which directly impacts productivity and service delivery. The main functions generally cover order management, inventory tracking, shipping coordination, and data reporting and analytics. Each of these elements plays a significant role in enhancing operational capabilities, driving profitability, and offering better customer experiences.
Order Management
Order management is the backbone of a warehouse ordering system. This function involves receiving, processing, and tracking customer orders. A well-implemented order management system minimizes the time from receipt of the order to delivery. Importantly, it provides real-time visibility into order status.
Key benefits of efficient order management include:
- Enhanced speed in fulfilling orders
- Improved accuracy in order details
- Decreased likelihood of errors or misunderstandings
Proper integration of an order management system with other functions is essential. For example, linking it to the inventory tracking system helps in maintaining stock levels accurately, ensuring orders are fulfilled without delay due to stock-outs.
Inventory Tracking
Inventory tracking is another critical function. It allows for real-time updates on inventory levels, locations, and the status of items within the warehouse. Effective inventory management plays a vital role in avoiding excess or shortage in stock, which can lead to increased costs or missed sales opportunities.
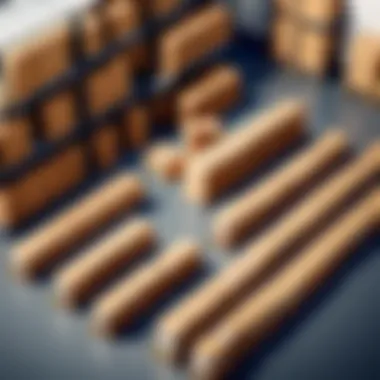
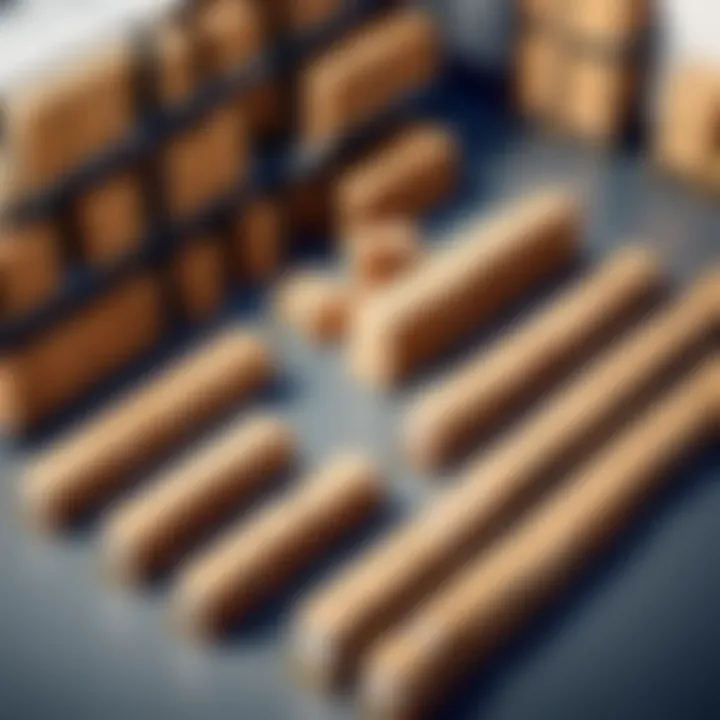
With inventory tracking, businesses can enjoy benefits such as:
- Better forecasting through analysis of trends
- Increased visibility into stock levels
- Enhanced ability to manage reorder points
As the warehouse size grows, accurate inventory tracking becomes more complex. Utilizing technology like barcode scanners or RFID can streamline the process significantly.
Shipping Coordination
Shipping coordination is pivotal in ensuring that orders reach customers timely. This function involves the planning and execution of logistics tasks for shipping products. It includes selecting shipping couriers, scheduling pickups, and tracking shipments in transit.
The significance of good shipping coordination cannot be overstated. It leads to:
- Reduction in transportation costs
- Faster delivery times
- Increased reliability of delivery schedules
By connecting the shipping process with order management, businesses can provide customers with accurate tracking information and reduce instances of late deliveries.
Data Reporting and Analytics
Lastly, data reporting and analytics provide crucial insights into warehouse operations. This function involves the collection, management, and analysis of operational data to guide decision-making. Through the right analytics tools, management can identify trends, monitor key performance indicators, and recognize areas for improvement.
The benefits include:
- Enhanced strategic planning
- Real-time insights for agile decision-making
- Identification of inefficiencies in processes
Robust data reporting can reveal patterns in order volumes or inventory turnover rates, which can be essential for planning future operations and scaling the business.
"An efficient warehouse ordering system can transform the entire supply chain, ensuring that every element works in harmony."
Understanding these core functions is the first step for businesses looking to optimize their warehouse operations successfully. Each component is interconnected and contributes to a unified system that enhances overall performance and customer satisfaction.
Benefits of Implementing a Warehouse Ordering System
The implementation of a warehouse ordering system brings a multitude of advantages, significantly transforming how warehouses operate. These benefits are crucial for businesses aiming to enhance their supply chain efficiency. Familiarity with these advantages can aid decision-makers in evaluating the necessity and potential return on investment for such systems.
Enhanced Operational Efficiency
A primary benefit of using a warehouse ordering system is the enhancement of operational efficiency. By automating various tasks, such systems streamline workflows. For instance, automated order processing reduces the time taken to fulfill requests. Workers can access real-time data to make informed decisions quickly and respond to changes in demand or inventory levels. This efficiency reduces bottlenecks that often plague manual systems and leads to quicker response times, which are essential in todayโs fast-paced market.
Reduction in Errors
Another significant advantage is the reduction in errors. Manual data entry is prone to mistakes, which can lead to inventory discrepancies and fulfillment issues. Warehouse ordering systems minimize human error through automated processes. Barcode scanning and RFID technology ensure that the correct items are picked and shipped. This accuracy not only enhances the operational workflow but also boosts customer trust. Errors can result in returns and dissatisfaction, so having a system that limits these occurrences is vital for maintaining a good reputation.
Cost Savings
Cost savings is a compelling reason to implement warehouse ordering systems. While there may be an initial investment, the long-term savings can be substantial. Automation reduces labor costs as fewer personnel are needed for order processing and inventory management. Additionally, preventing errors leads to cost reductions in returns and customer service issues. By optimizing inventory levels, businesses can also decrease holding costs.
Improved Customer Satisfaction
Lastly, improved customer satisfaction is a benefit that cannot be overlooked. By ensuring timely and accurate order fulfillment, businesses can enhance the overall customer experience. When customers receive their orders correctly and on time, their loyalty increases. A warehouse ordering system provides customers with real-time tracking information, making them more informed about their purchases. Happy customers are more likely to return and recommend a business, further driving revenue.
"In an age where customer experience drives business success, efficient warehouse operations are vital."
Selecting the Right Warehouse Ordering System
Selecting the right warehouse ordering system is a critical decision for any organization aiming to streamline operations effectively. This choice directly impacts various areas including order fulfillment, inventory management, and overall efficiency. The right system enables organizations to adapt to changing demands and provides a scalable solution as the business grows.
Identifying Business Needs
Understanding specific business needs is the first step in selecting a warehouse ordering system. Every enterprise is unique, with different volumes of products and types of inventory. Assessing these unique requirements involves asking several questions:
- What types of products are stored? This concerns not only the categories but also the handling requirements.
- What is the average order volume? High turnover requires more efficient systems, while lower volumes may benefit from simpler solutions.
- What are the peaks and troughs of business activity? If business has seasonal fluctuations, a flexible system can accommodate this variability.
By conducting a thorough analysis of current and projected operational needs, businesses can narrow down options that align with their objectives.
Evaluating Software Features
After identifying needs, evaluating software features is essential. A good warehouse ordering system should offer functional components that align with those needs. Key features might include:
- Order Management: Efficiently process orders from receipt to shipment.
- Inventory Tracking: Monitor stock levels in real-time to prevent shortages or overstocking.
- Reporting Capabilities: Access to analytics helps in understanding performance metrics and making informed decisions.
Make sure to seek solutions with scalability in mind, allowing for new features as business requirements evolve.
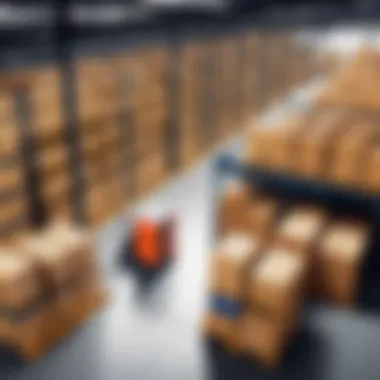
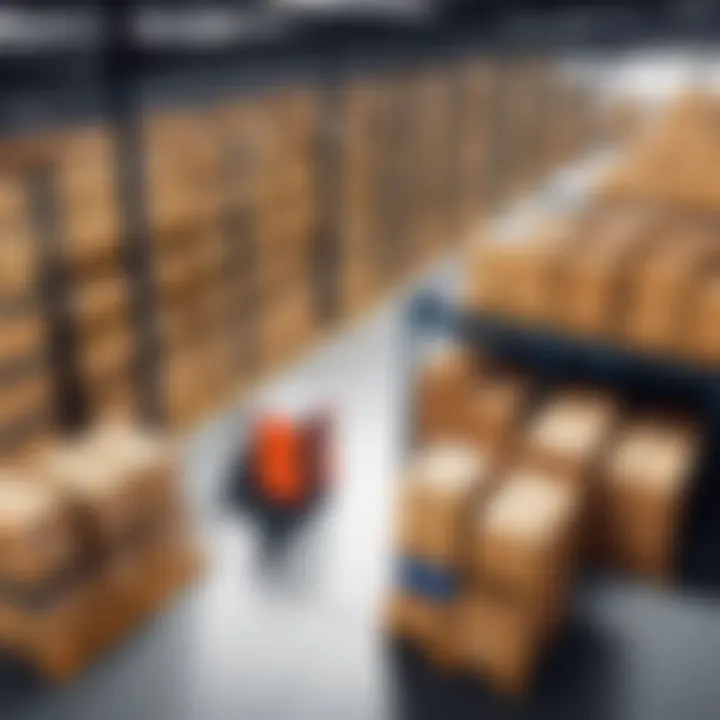
Considering Integration Capabilities
Integration capabilities are crucial when selecting a warehouse ordering system. The system must work seamlessly with existing tools such as Enterprise Resource Planning (ERP) systems, Customer Relationship Management (CRM) software, and shipping solutions.
A lack of integration can lead to data silos, where important information is trapped in different systems. This can cause miscommunication and errors that reduce efficiency. Selecting a system that offers strong integration capabilities enhances workflow and data accuracy.
Reviewing Vendor Reputation
Finally, reviewing vendor reputation plays an essential role in the selection process. Investigate potential vendors to gauge their reliability and support. Considerations include:
- Customer Reviews: Feedback from other businesses that have implemented the systems.
- Industry Recognition: Awards and certifications that validate the vendorโs software quality.
- Support Services: Availability of customer support post-implementation is vital.
"A reputable vendor often provides excellent technical support and has a track record of successful implementations."
A well-informed selection process ensures that the chosen warehouse ordering system not only meets current needs but also supports future growth.
Implementation Strategies for Warehouse Ordering Systems
Successful implementation strategies for warehouse ordering systems are essential for maximizing efficiency and ensuring that the chosen solution meets the specific needs of a business. A systematic approach not only simplifies the deployment process but also encourages team involvement and minimizes disruption to ongoing operations. Implementing a warehouse ordering system can transform a warehouse's operational framework, driving tangible benefits such as increased accuracy and speed in order processing. Such strategies help in aligning the technology with business objectives, thereby facilitating smoother transitions into new workflows.
Step-by-Step Implementation Process
The implementation of a warehouse ordering system can be complex, but breaking it down into manageable steps can significantly enhance clarity and execution. Here are the key steps to consider:
- Assessment of Current System: Evaluate the existing processes, technologies, and workflow practices to identify gaps and areas for improvement.
- Defining Requirements: Gather inputs from stakeholders to determine functional and technical requirements of the new system.
- Selecting the Right Software: Based on requirements, choose suitable software. Evaluate features, integration capabilities, and scalability.
- Planning Implementation Timeline: Develop a project plan that outlines the timeline, milestones, and responsibilities.
- Data Migration: Prepare and migrate existing data into the new system, ensuring accuracy and integrity.
- System Configuration: Customize the software settings to align with the company's operational processes.
- Testing Phase: Conduct rigorous tests to ensure that the system works as intended and can handle real-world scenarios.
- Go Live: Launch the system officially, ensuring support is available for users during the transition.
- Monitoring and Support: After implementation, continuous monitoring is crucial to identify any issues that may arise and to provide necessary support.
Training Staff Efficiently
Staff training plays a critical role in the successful adoption of a warehouse ordering system. Without proper training, even the most advanced system can falter due to user error. Hereโs how to approach staff training effectively:
- Develop Training Materials: Create comprehensive training guides and resources such as manuals, videos, and FAQs tailored to different user levels.
- Hands-On Training Sessions: Organize interactive training sessions that allow employees to engage with the software in a controlled environment.
- Utilize Super Users: Designate experienced employees as super users who can offer additional support during and after the training process.
- Feedback Mechanism: Establish a feedback system so employees can share their experiences and suggest improvements regarding the training process.
Change Management Considerations
Change management is vital when introducing a new warehouse ordering system. Addressing the people side of change often proves as important as the technical aspects. Here are some key considerations:
- Communicate Benefits: Clearly communicate the benefits of the new system to all employees, emphasizing how it will positively impact their roles.
- Involve Employees Early: Involve employees in discussions from the outset. Their input can highlight potential challenges and solutions.
- Address Resistance: Identify common sources of resistance and create strategies for overcoming them. This may involve additional support or resources.
- Continuous Engagement: After implementation, keep engaging staff with updates and check-ins on how they are adjusting to the new system. This can foster a supportive environment.
โAn effective warehouse ordering system is only as good as the users who operate it.โ
With detailed implementation strategies, businesses can ensure a smoother transition, minimizing disruptions and maximizing the potential advantages of modern warehouse ordering systems.
Challenging Aspects of Warehouse Ordering Systems
Implementing a warehouse ordering system is not without its challenges. Addressing these challenges is essential for success. Understanding the difficulties can lead to better decision-making and smoother execution. This section covers three significant challenges: technical issues, user adoption barriers, and ongoing maintenance requirements. Each of these elements plays a crucial role in the overall effectiveness of the system.
Technical Challenges
Technical challenges are often the most daunting when it comes to warehouse ordering systems. These can include compatibility issues with existing software, lack of real-time data processing, and data security concerns. For instance, many warehouses still use legacy systems that may not integrate well with newer solutions. This results in data silos where information is not shared efficiently.
Moreover, data security is a growing concern as cyber threats evolve. Sensitive information could be at risk if proper security measures are not in place. Organizations need to invest in robust cybersecurity protocols to protect data. Failure to address these technical challenges can lead to operational disruptions and diminished trust in the system.
User Adoption Barriers
User adoption barriers often hinder the successful implementation of warehouse ordering systems. Employees may resist change due to fear of the unknown or a lack of understanding of the system's benefits. Effective training programs are crucial. They should be designed to address the skills gap and provide users with the confidence to operate the new system. Regular feedback from employees can also help improve the usability of the system.
Additionally, management must foster a culture that embraces technological adoption. If employees feel that their concerns are not heard or addressed, they may be less inclined to use the system effectively. Thus, creating an environment that encourages engagement is vital.
Ongoing Maintenance Requirements
Ongoing maintenance is another critical aspect of warehouse ordering systems. These systems require regular updates to address bugs and improve functionality. Without consistent maintenance, the system may become outdated or inefficient over time. This can lead to decreased operational efficiency and increased frustration among users.
Furthermore, organizations should also budget for potential hardware upgrades. As technology evolves, hardware that once sufficed may no longer meet demands.
Future Trends in Warehouse Ordering Systems
The warehouse industry continues to evolve rapidly due to advancements in technology. Future trends in warehouse ordering systems are essential for maintaining a competitive edge. These trends can optimize operations and respond to changing consumer demands. Understanding these developments allows businesses to prepare for the future.
Artificial Intelligence and Automation
Artificial Intelligence (AI) has significantly impacted warehouse ordering systems. AI aids in process automation, reducing manual work and streamlining operations. For instance, AI algorithms can predict order patterns, helping businesses manage inventory more effectively. This not only increases efficiency but also enhances accuracy in order fulfillment.
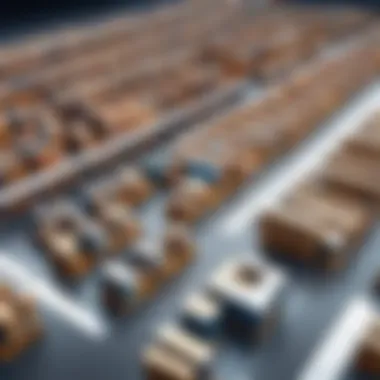
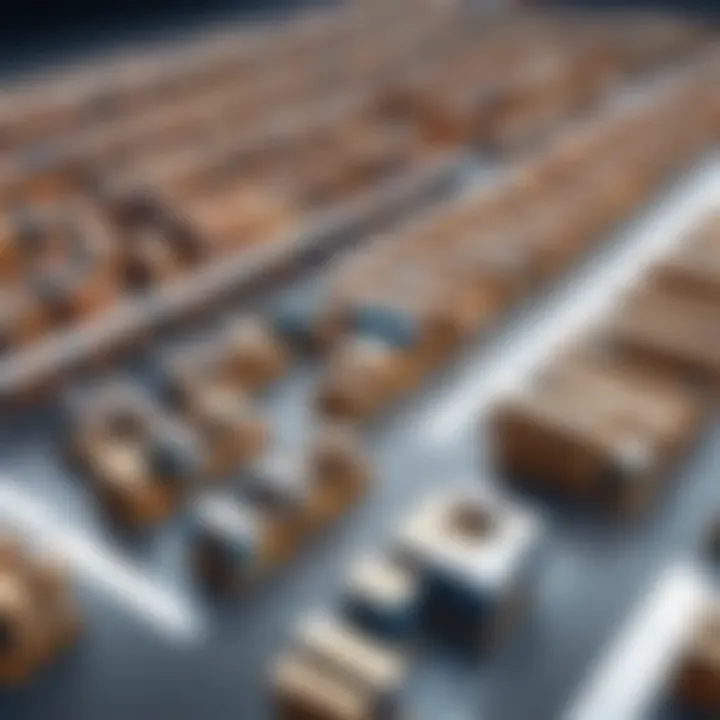
Automation through robotics is another key component. Automated guided vehicles (AGVs) and robotic arms can perform repetitive tasks, such as transporting goods across the warehouse. The implementation of AI and automation leads to faster processing times and lower labor costs.
Businesses that integrate these technologies will find themselves at a strategic advantage. It is crucial to select technologies that align with specific operational needs, ensuring a seamless integration into existing systems.
Real-Time Data Analytics
Real-time data analytics is transforming how warehouses operate. By utilizing data analytics, businesses can gain immediate insights into their processes. This includes tracking inventory levels, monitoring order status, and assessing shipping times.
Having access to this data allows for quick decision-making. For example, if stock levels drop unexpectedly, companies can reorder supplies before they run out. It also enables proactive identification of trends and challenges, allowing businesses to make informed adjustments.
Adopting real-time analytics can also improve accountability within the warehouse. Employees can access performance metrics, which allows for continuous improvement and higher productivity.
Integration with IoT Devices
The Internet of Things (IoT) has emerged as a significant trend in warehouse operations. Connecting devices through IoT networks permits vast data collection throughout the supply chain. Sensors can track temperature, humidity, and other environmental factors vital for goods management.
Integration with IoT devices can enhance workflow efficiency. For instance, wearable devices can alert workers about inventory needs or maintenance requirements. Additionally, real-time monitoring of equipment can prevent costly downtime due to malfunctions.
IoT contributes to smarter logistics overall. By providing deeper visibility into supply chain operations, businesses can respond quicker to any disruptions or inefficiencies. Integrating IoT into warehouse ordering systems is becoming vital for organizations aiming for improved operational effectiveness.
"The future of warehouse ordering systems lies in technology integration, enhancing efficiency and accountability."
Case Studies of Effective Warehouse Ordering System Implementation
The exploration of case studies surrounding warehouse ordering systems offers a vital perspective on the real-world applications and successes of these systems. By examining the experiences of various enterprises, businesses can glean valuable insights about the implementation processes, challenges, and the tangible benefits derived from these systems. Such case studies highlight specific scenarios where these systems have not only enhanced operational efficiency but also transformed the entire supply chain workflow. They provide a roadmap for future implementations while illustrating both the advantages and potential pitfalls to avoid. This section aims to dissect these experiences across different business sizes and industries, providing a holistic view of how effective implementation can unfold.
Large Enterprises
Large enterprises often face unique challenges when it comes to warehouse management. These organizations typically deal with higher volumes of inventory and more complex logistics chains. Implementing a robust warehouse ordering system can yield significant operational efficiencies. For instance, a major retailer, such as Walmart, utilizes a highly sophisticated warehouse ordering system that integrates advanced analytics with AI capabilities. This system enables them to anticipate demand fluctuations and manage their inventory dynamically.
Benefits realized by large enterprises include:
- Streamlined Operations: Automated processing reduces the need for manual input.
- Improved Visibility: Real-time tracking of inventory allows for better restocking decisions.
- Cost Reduction: Efficient order fulfillment leads to lower operational costs.
However, large enterprises must also navigate the challenges of integration and standardization across various departments. A well-executed implementation includes engaging all stakeholders from IT to operations to ensure alignment and minimize resistance.
Small to Medium-Sized Businesses
Smaller businesses often operate under different constraints than large enterprises. They may have limited resources and require a more flexible warehouse ordering system. A case illustrative of this is a local clothing retailer implementing the TradeGecko inventory management system. This solution enabled them to automate their order management and strengthen their customer relationship by integrating with existing e-commerce platforms.
Key considerations for small to medium-sized businesses include:
- Cost-Effectiveness: The system should facilitate growth without overwhelming the budget.
- Ease of Use: A user-friendly interface is crucial for smaller teams with limited IT support.
- Scalability: As the business grows, the system should evolve to meet increased demands.
These businesses can leverage these systems to compete more effectively with larger organizations, as they allow for agile responses to market changes and customer demands.
Sector-Specific Applications
Different industries face specialized challenges that warrant tailored warehouse ordering systems. For instance, the food and beverage sector has specific requirements such as strict compliance with health regulations and rapid turnover of inventory. A company like Coca-Cola utilizes a specialized warehouse ordering system that addresses these needs. It allows for precise tracking of expiration dates, ensuring that perishable goods are managed effectively and reducing waste.
Some sector-specific applications include:
- Pharmaceuticals: Enhanced tracking protocols to meet regulatory compliance.
- Automotive: Just-in-time inventory systems to optimize supply chain responsiveness.
- E-commerce: Dynamic warehousing solutions that can adapt to variable demand patterns.
Tailoring the system to the specific needs of an industry can lead to optimized operations and improved performance metrics.
"Real-world implementations are not merely academic; they provide essential insights every enterprise should consider when investing in a warehouse ordering system."
Through examining these varied case studies, it becomes clear that effective implementation is key to unlocking the potential of warehouse ordering systems across different business contexts.
Culmination
In this article, we have explored the multifaceted realm of warehouse ordering systems, illuminating their core components and merits. Understanding the function and significance of these systems is critical for any organization aiming to optimize their logistics operation. This section aims to summarize the key insights gathered throughout the discussion, as well as to provide final thoughts for organizations considering such a system.
Summarizing Key Insights
Throughout the article, we have addressed several essential aspects regarding warehouse ordering systems. Here are some of the most critical points:
- Defining Warehouse Ordering Systems: These systems serve as the backbone of efficient supply chain management.
- Core Functions: Key functionalities include order management, inventory tracking, and shipping coordination.
- Benefits: Enhanced operational efficacy, reduction of errors, cost savings, and improved customer satisfaction are notable advantages.
- Implementation: A structured approach to implementing these systems is crucial for smooth integration into existing frameworks.
- Challenging Aspects: Understanding the potential barriers, such as technical issues and user adoption challenges, can prepare organizations for a more seamless transition.
- Future Trends: Advancements like artificial intelligence and real-time data analytics are likely to reshape the way warehouse ordering systems operate.
These insights demonstrate that adopting a warehouse ordering system can profoundly impact an organization's operational effectiveness.
Final Thoughts on Warehouse Ordering Systems
As businesses transition towards more sophisticated supply chain strategies, warehouse ordering systems become increasingly pertinent. Organizations must not only be aware of the immediate advantages but also consider the long-term implications of their decisions. The selection, implementation, and maintenance of these systems are not trivial tasks; they require thoughtful planning and ongoing evaluation.
For decision-makers, the integration of modern technologies, such as IoT and AI, into warehouse processes will likely drive new efficiency and transparency. Furthermore, establishing a culture that embraces technology can lead to successful user adoption and sustained benefits.