Understanding Work Order Maintenance Software
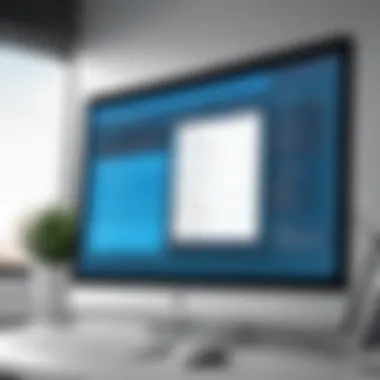
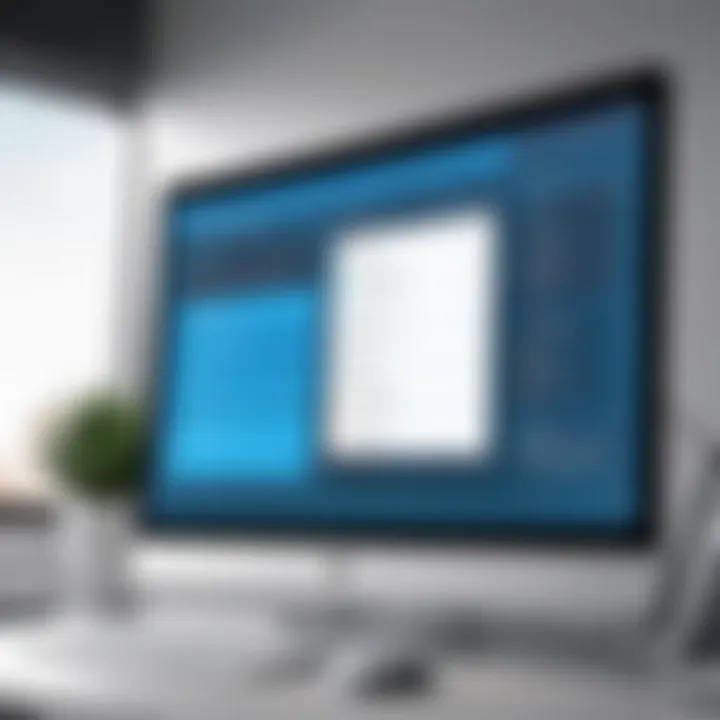
Intro
In today's fast-paced business landscape, work order maintenance software has emerged as a critical tool for organizations aiming to optimize operational efficiency. The constant pressure to improve productivity while minimizing costs requires decision-makers to explore effective solutions. This software is designed to manage work orders seamlessly, ensuring that maintenance activities are conducted efficiently. Businesses that embrace such technology often find themselves with significant advantages over competitors that rely on traditional methods.
Understanding the intricacies of work order maintenance software is essential for business leaders and IT professionals. From recognizing key functionalities to discerning integration capabilities, the knowledge gained here can empower organizations to make informed decisions about the tools they implement.
Features Overview
Work order maintenance software encompasses various features that serve to enhance its usability and effectiveness. By breaking down these key functionalities, organizations can better appreciate the value this software brings to daily operations.
Key Functionalities
The fundamental functionalities of work order maintenance software include:
- Work Order Management: Automating and tracking work orders is central to the software. Users can create, modify, and close work orders, all while maintaining a comprehensive record.
- Preventive Maintenance Scheduling: This feature allows organizations to preemptively manage equipment and asset maintenance, reducing downtime and unforeseen costs.
- Resource Allocation: Efficiently distributing tasks among available personnel ensures that the right resources are utilized for each job, maximizing workforce productivity.
- Reporting and Analytics: Gleaning insights from performance data enables organizations to make informed decisions and drive continuous improvements.
These functionalities not only streamline processes but also foster a culture of accountability by ensuring all maintenance activities are traceable.
Integration Capabilities
For work order maintenance software to be truly effective, it must integrate seamlessly with existing systems. Notable integration capabilities include:
- ERP Systems: Many organizations use Enterprise Resource Planning systems. The ability to connect maintenance software with ERP leads to improved resource management and alignment of operational goals.
- IoT Devices: Internet of Things technology is playing an increasingly vital role in maintenance strategies. Connecting sensors and devices to work order software allows for real-time monitoring of equipment conditions.
- Mobile Access: Ensuring that technicians can access work orders through their mobile devices enhances flexibility and responsiveness in the field.
These integrations reinforce the functionality of work order maintenance software, transforming how maintenance tasks are handled across organizations.
Pros and Cons
Understanding the advantages and disadvantages of work order maintenance software is crucial for a thorough analysis.
Advantages
- Increased Efficiency: Streamlined processes reduce the time spent on manual tasks, thereby enhancing productivity.
- Cost Reduction: Proactive maintenance practices lead to fewer breakdowns and unexpected expenses.
- Enhanced Visibility: Management can gain comprehensive oversight of maintenance tasks and performance metrics.
- Improved Compliance: Regulatory requirements can be managed more effectively with automated documentation and reporting.
Disadvantages
- Initial Investment: The cost of acquiring and implementing this software can be significant.
- Training Requirements: Staff may need training to adapt to new systems, which can temporarily slow operations during the transition.
- Dependence on Technology: Over-reliance on software can pose risks if systems fail or data is lost.
Prelude to Work Order Maintenance Software
Work order maintenance software is a critical tool in today’s fast-paced business environment. Its importance cannot be overstated, as it serves as a backbone for operational efficiency across industries. Understanding this software can significantly impact an organization’s bottom line and overall productivity.
This section aims to unpack the complexities of work order maintenance software, laying the groundwork for the subsequent discussions in this article. The main aspects include defining the software, examining its evolution, and considering various factors that influence its implementation.
With clear insights, decision-makers can appreciate how this tool not only streamlines maintenance tasks but also integrates with broader operational strategies. The careful selection and implementation can lead to more effective resource utilization, fewer downtimes, and ultimately, enhanced service delivery.
Defining Work Order Maintenance Software
Work order maintenance software refers to digital tools designed to manage maintenance tasks and track work orders efficiently. These applications facilitate the creation, scheduling, and tracking of maintenance requests and activities. At their core, these systems automate processes, ensuring that maintenance operations are carried out on time and to specification.
Functions of this software often include:
- Creating and assigning work orders: Users can generate work orders based on specific needs or maintenance schedules.
- Tracking progress: Information about each work order can be monitored in real-time, allowing for management transparency.
- Reporting: Most software solutions offer robust reporting features that generate insights about maintenance operations, helping organizations make data-driven decisions.
In sum, work order maintenance software improves workplace efficiency by automating repetitive tasks and centralizing information flow.
Evolution of Maintenance Software
The landscape of maintenance software has changed drastically over the years. Initially, maintenance tasks were managed through paper-based systems, which were prone to errors and inefficiencies. As technology progressed, the advent of computerized systems marked a significant shift.
In the early 2000s, businesses began adopting Computerized Maintenance Management Systems (CMMS). These systems allowed for comprehensive tracking of assets and operational activities.
Today, the trend has moved towards cloud-based solutions, enabling real-time accessibility and collaboration across teams. This shift offers flexibility and scalable solutions that can adapt to organizational growth. Furthermore, integration with IoT devices has become common, providing users with automated data input and improved predictive maintenance capabilities.
"The evolution of maintenance software reflects broader technological advancements, with an emphasis on efficiency and data management."
In this context, understanding work order maintenance software in its current form allows organizations to leverage its full potential, ensuring they remain competitive. The ongoing innovations in this field indicate a trajectory toward even more intelligent and user-friendly solutions.
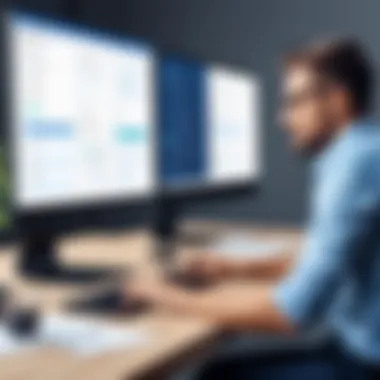
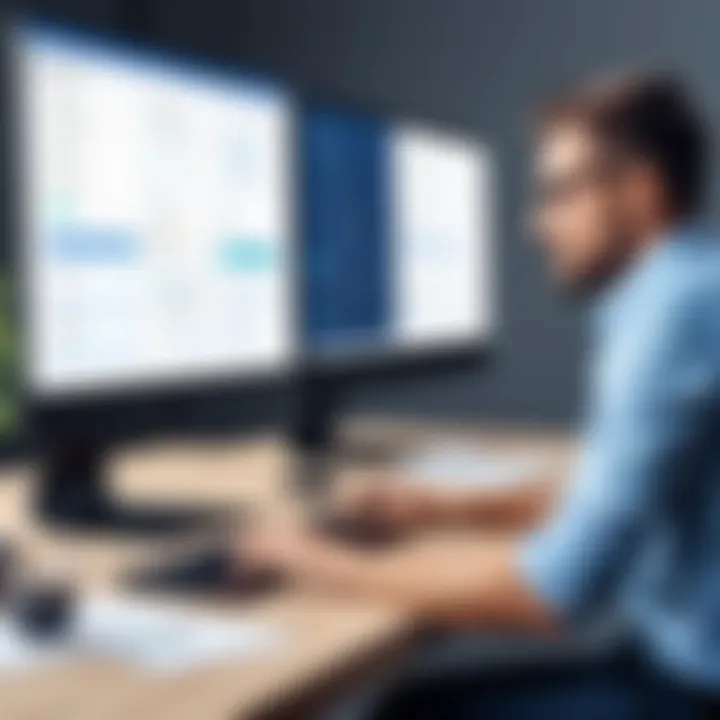
Key Features of Work Order Maintenance Software
Understanding the key features of work order maintenance software is essential for organizations aiming to enhance their operational efficiency. Each feature plays a crucial role in supporting maintenance tasks, ensuring that processes are not only followed but optimized. Such software systems have evolved significantly, and their current capabilities are designed to streamline tasks while providing insights that help businesses make better decisions. In this section, we will delve into the specific features that define effective work order maintenance software and discuss their relevance in today’s business environment.
Work Order Creation and Management
Work order creation and management is at the core of any effective maintenance software. This feature allows users to generate work orders quickly, providing a clear plan for maintenance activities. A well-designed system enables users to input necessary details such as the type of work, the location, and the person assigned to the task. This not only improves clarity but also helps prioritize jobs based on urgency or importance.
Moreover, the ability to track the status of work orders in real time is invaluable. This transparency allows managers to see who is working on what and reallocate resources if necessary. In addition, automating notifications when work orders are created or completed can ensure smooth operations. This interaction fosters a more dynamic and responsive maintenance culture, leading to reduced downtime and improved productivity.
Asset Tracking and Inventory Management
Asset tracking and inventory management are critical components in work order maintenance software. Keeping track of physical assets means understanding their current state, location, and usage history. This feature helps in minimizing losses that can occur from misplacement or theft of tools and equipment. Proper asset management enables organizations to avoid over-purchasing through an understanding of their existing inventory.
Using features like barcoding or RFID (Radio Frequency Identification) can enhance the accuracy of asset tracking. When an asset is checked in or out, the software updates in real time, providing a true snapshot of inventory. This information is crucial for planning maintenance schedules and ensuring that the necessary parts and tools are available when needed.
Scheduling and Dispatching
Scheduling and dispatching capabilities provide users with a framework to manage their workforce efficiently. A comprehensive scheduling tool allows for the assignment of tasks based on availability, skill level, and urgency. Advanced software solutions can incorporate calendar views and scheduling conflicts, automating the assignment process and reducing the need for manual adjustments.
In addition, the dispatching function ensures that technicians receive their assignments promptly. This quick access to work orders can lead to faster response times, especially in emergency situations. The combination of effective scheduling and dispatching can greatly enhance workplace efficiency, making it easier to complete tasks on time and within budget.
Reporting and Analytics Tools
Reporting and analytics tools are pivotal in providing insights into maintenance operations. With the right data, decision-makers can identify trends, measure performance against key performance indicators (KPIs), and evaluate the effectiveness of their maintenance strategies. These tools enable customization of reports to meet specific needs, be it for upper management or operational teams.
Some systems also employ advanced analytics, predictive modeling, and AI technologies. This can inform preventive maintenance strategies, allowing companies to forecast issues before they become critical. Accurate operational data leads to enhanced decision-making, which is essential for organizations focused on continuous improvement. Analyzing this data can reveal opportunities for cost savings and efficiency gains, proving the value of maintaining comprehensive records through this software.
Benefits of Implementing Work Order Maintenance Software
Implementing work order maintenance software offers several tangible benefits for organizations. Understanding these benefits is crucial as decision-makers evaluate whether to invest in such technology. Each of these advantages reflects a deeper perspective on how efficient systems can transform operational processes.
Increased Efficiency
One of the standout advantages of work order maintenance software is the marked increase in operational efficiency. This software streamlines the work order process, enhancing tracking and management. Tasks can be assigned more efficiently, and staff can prioritize their workload with clarity.
For instance, a maintenance team that previously juggled manual operations can quickly see which issues need attention through their dashboard. The ability to view work orders in real-time allows for quicker response times to emergencies or scheduled maintenance, resulting in a more proactive approach. As the software reduces redundant efforts, teams can focus on more critical tasks, hence optimizing resource usage.
Cost Reduction
Cost reduction is another significant benefit that organizations cannot overlook. Work order maintenance software minimizes paperwork and administrative tasks, which often translate to lower operational costs. Moreover, through better asset management, organizations can prolong the life of their equipment and reduce replacement costs.
Effective scheduling provided by the software ensures that maintenance occurs only when necessary. This mitigates the risk of over-maintaining or under-maintaining equipment, which can lead to unforeseen expenditures and losses. Over time, these efficiencies contribute to a healthier bottom line, proving that investment in maintenance software can yield substantial financial returns.
Enhanced Communication
Communication gaps can plague maintenance teams, leading to delays and confusion. Work order maintenance software fosters improved communication among team members. It allows for real-time updates, meaning that every stakeholder is on the same page regarding tasks, timelines, and outcomes.
For example, field technicians can easily update the status of a work order directly from their mobile devices. This immediate feedback loop allows for quicker decision-making and a more agile workflow. Additionally, this enhanced communication can extend beyond the maintenance team to customers and suppliers, creating a more transparent operational environment.
Improved Compliance and Safety
Safety and compliance are paramount in any operation, particularly in industries with stringent regulatory standards. Work order maintenance software contributes to improved compliance with regulations by automating documentation and reporting processes. This level of organization helps ensure that all maintenance activities meet necessary guidelines.
Furthermore, by maintaining optimal equipment performance through regular maintenance updates, organizations can mitigate safety risks. The software can also prompt when to implement specific safety procedures, ensuring that nothing is overlooked. Compliance becomes a seamless aspect of the operation rather than an afterthought.
In summary, investing in work order maintenance software is not just about managing tasks; it's about empowering organizations to work smarter, reduce costs, enhance communication, and maintain safety standards.
Through these four key benefits, businesses can transform their maintenance processes, paving the way for a more efficient, cost-effective, and compliant operational framework.
Challenges in Selecting Work Order Maintenance Software
Selecting the right work order maintenance software can be a daunting task for many organizations. This process involves understanding a complex landscape of options, each offering distinct features and benefits. It is crucial to approach this selection phase with a clear set of criteria to ensure a positive impact on operations. The importance of this topic is not only to simplify decision-making but also to minimize potential disruptions that may arise from implementing the wrong solution.
Understanding Business Requirements
Before diving into software options, organizations must first grasp their specific business requirements. This phase includes a thorough analysis of operational pain points. Identifying these issues helps in evaluating which software features are non-negotiable. For instance, does the team need advanced reporting capabilities? Or is mobile access more crucial for field workers? Comprehending these necessities lays a strong foundation for the selection process.
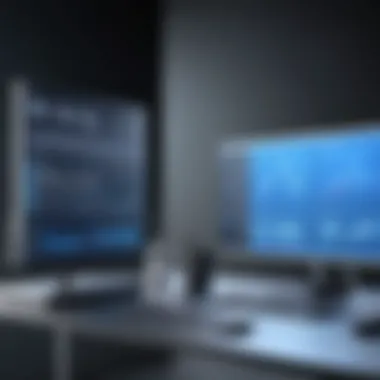

Additionally, it can be valuable to involve various stakeholders in this assessment. User feedback can provide insights into how different departments interact with work orders and maintenance tasks. Gathering these views ensures the chosen software addresses the core demands of the operation.
Navigating Vendor Options
Once business requirements are understood, organizations must navigate the plethora of vendor options available. Each vendor claims unique strengths and advantages, making it imperative to conduct a comparative analysis. Prospective buyers should consider aspects such as customer support, ease of use, and pricing structures.
Researching reviews and case studies enhances this process. Engaging with current users can yield firsthand insight into software performance.
The decision should also factor in the vendor's history. A long-standing, reputable vendor may offer more stability compared to newer entrants. Thus, organizations should evaluate not only the features but also the reliability and reputation of the vendors involved.
Integration with Existing Systems
Integrating new work order maintenance software with existing systems is a critical challenge. Software that operates in silos can create inefficiencies and a fragmented workflow. Organizations must assess how well potential solutions will integrate with current tools, such as ERP systems, asset management software, and other operational systems.
A seamless integration can foster better data flow across departments, reducing redundancy and enhancing accuracy. Technical compatibility is essential; thus, understanding API capabilities and integration support is a must.
Organizations may also want to budget for potential integration costs. Sometimes additional investment is needed to ensure that the new software works harmoniously with legacy systems, thus avoiding the pitfalls of operating with incompatible technologies.
Correctly navigating these challenges can lead to significant operational improvements, ultimately making the investment in work order maintenance software worthwhile.
By acknowledging the challenges in selecting work order maintenance software, organizations position themselves for a smoother transition and successful implementation.
Implementing Work Order Maintenance Software
Implementing work order maintenance software is crucial for organizations looking to optimize their maintenance processes. This phase translates theoretical knowledge into practice, ensuring that the chosen software aligns with business objectives. A successful implementation can lead to improved efficiency, effective asset management, and reduced operational costs. These advantages underscore the importance of meticulous planning, training, and monitoring during the adoption process.
Planning the Implementation Process
Effective planning is the foundation for a successful software implementation. Before launching the process, organizations should assess their current maintenance practices. This includes identifying inefficiencies that the software aims to address.
- Define Objectives: Clearly outline what the organization wants to achieve with the software. Possible goals include better resource allocation or enhanced reporting.
- Stakeholder Involvement: Engage key stakeholders from different departments, including IT, maintenance, and management. Their insights will help to shape the implementation strategy.
- Budget Considerations: Understand the financial implications. Allocate resources for software purchase, installation, and ongoing operational costs.
- Timeline Development: Create a realistic timeline that includes all phases of implementation, from initial analysis to full deployment.
This comprehensive planning phase allows organizations to minimize disruption and align the new system with existing workflows.
Training Staff and Users
Training is a vital aspect of the implementation process. An investment in staff training ensures users are confident and efficient in utilizing the software from day one. Without proper training, even the most sophisticated software may not yield the expected results.
- Role-Specific Training: Different user roles may require specific training programs. Maintenance staff, for instance, may need hands-on training with asset management, while management might focus on reporting tools.
- Interactive Workshops: Facilitate workshops that allow users to practice using the software in simulated environments. This hands-on approach helps to build familiarity.
- Ongoing Support: Establish ongoing support channels for users to address issues as they arise. This can include regular Q&A sessions and access to an FAQ resource.
A well-trained staff is more likely to embrace the software, leading to smoother operations.
Monitoring and Evaluation Post-Implementation
Monitoring and evaluation should not be an afterthought. Collecting feedback after the implementation provides valuable insights into the software’s effectiveness. This phase allows organizations to assess whether the software meets its intended goals.
- Performance Metrics: Set specific KPIs to measure success. Metrics might include task completion rates or the time taken to resolve work orders.
- User Feedback: Regularly solicit feedback from users and incorporate necessary adjustments. Their insights can identify issues or areas for improvement.
- Review Meetings: Conduct periodic review meetings to discuss findings and adjust strategies as needed. Collaboration between departments can enhance the responsiveness of the organization to emerging challenges.
Monitoring aids continuous improvement, ensuring the software remains a valuable tool for long-term operational success.
Comparative Analysis of Work Order Maintenance Software
In today’s rapidly evolving business environment, understanding the different types of work order maintenance software is essential. Companies must make informed decisions that significantly affect their operations and bottom line. A comparative analysis allows decision-makers to assess options critically, weighing the strengths and weaknesses of various software solutions. This analysis can highlight unique features, potential return on investment, and compatibility with existing systems, guiding businesses in selecting the most suitable software for their specific needs.
Cloud-based vs. On-Premises Solutions
Choosing between cloud-based and on-premises work order maintenance software is a fundamental decision. Cloud-based solutions often provide more flexibility and scalability. They allow access from any device with internet connectivity, which can enhance mobility for field technicians. Updates and maintenance are handled by the vendor, simplifying the IT burden for organizations.
Conversely, on-premises solutions can offer heightened security and control over data. Companies in regulated industries or with strict compliance requirements might prefer this option. Integrating on-premises software with existing systems can be more complex but may be necessary for seamless operation.
A direct comparison includes:
- Cost: Cloud solutions usually operate on a subscription model, while on-premises may involve a high upfront cost and ongoing maintenance expenses.
- Accessibility: Cloud software can be accessed anytime, whereas on-premises systems require being on-site to access resources.
- Customizability: On-premises solutions can often be customized more thoroughly, though this can require significant resources.
- Updates and Maintenance: With cloud solutions, the vendor typically manages updates, while on-premises solutions require in-house IT resources.
"The choice between cloud-based and on-premises solutions is less about one being superior and more about which aligns better with business goals and operational needs."
Feature Comparison Across Leading Vendors
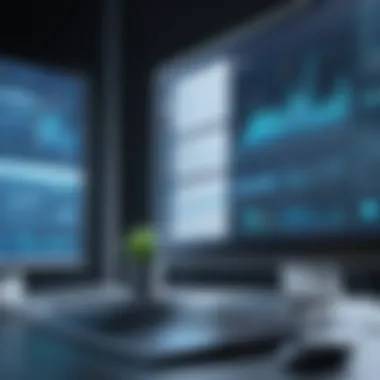
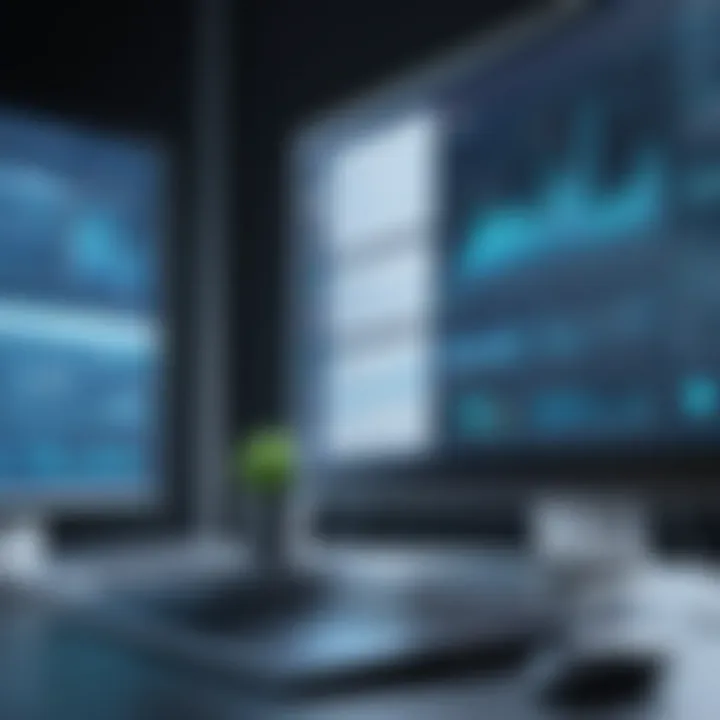
When examining work order maintenance software, features are a key focal point. Not all software is created equal, and the specific suite of tools can vary greatly from vendor to vendor. Understanding how various software options stack up against each other helps identify the best fit for specific operational requirements.
Important features to consider include:
- Work Order Management: Does the software provide robust tools for creating, assigning, and tracking work orders?
- Asset Management: Is there functionality for tracking assets and scheduling maintenance?
- Mobile Access: How well can field personnel access the system remotely?
- Integration Capabilities: Does it easily integrate with other systems such as ERP or CRM applications?
- Reporting and Analytics: Are decision-makers equipped with detailed insights and customizable reporting options?
Comparative assessments can use a feature matrix that directly contrasts the capabilities of various leading platforms. This structured approach helps organizations evaluate how closely each solution meets their criteria, ensuring a methodical selection process.
The Future of Work Order Maintenance Software
The realm of work order maintenance software is evolving rapidly. Understanding its future is crucial for organizations that aim to enhance their operations. The integration of advanced technology and shifting industry needs shape this trajectory. Thus, anticipating these changes ensures organizations remain competitive and efficient.
Emerging Trends and Technologies
Several trends are influencing the future of work order maintenance software. One of the most prominent is the shift towards cloud-based solutions. Companies increasingly prefer cloud platforms for their ability to offer real-time access and scalability. This transition reduces the reliance on in-house servers, allowing businesses to focus on core operations.
Another notable trend is the integration of mobile applications. Field technicians can now manage work orders directly from mobile devices. This capacity fosters immediate communication and enhances productivity. Technicians can update the status of tasks instantly, capturing real-time data for better decision-making.
Moreover, the use of IoT (Internet of Things) devices is on the rise. These devices facilitate continuous monitoring of assets, generating data that feeds back into the maintenance software. This leads to more informed maintenance decisions, reducing downtime and increasing asset lifespan. Organizations will benefit from adopting such technologies as part of their maintenance strategies.
Predictive Maintenance and AI Integration
The integration of predictive maintenance with work order maintenance software marks a significant advancement. This approach involves using data analytics to predict equipment failures before they happen. By analyzing patterns from historical data, companies can schedule maintenance activities proactively rather than reactively. This results in lower costs and improved efficiency.
Additionally, incorporating artificial intelligence (AI) further optimizes work order systems. AI can analyze vast amounts of maintenance data, uncovering insights that human analysis might miss. For instance, AI can identify trends and anomalies in equipment performance, prompting timely actions.
The combination of predictive maintenance and AI creates a powerful tool for decision-makers. It allows for not only efficient scheduling but also better inventory management. For instance, organizations can ensure they have the necessary parts on hand before a predicted failure, minimizing interruptions to operations.
"Harnessing the power of AI and predictive maintenance transforms how organizations approach their maintenance strategies, enhancing efficiency and reducing costs."
Real-World Applications of Work Order Maintenance Software
Work order maintenance software serves a crucial role in various sectors by streamlining processes and enhancing operational efficiency. These applications extend beyond mere work order management; they integrate into the fabric of daily operations in companies, ensuring that resources are utilized effectively. Such software empowers organizations to handle maintenance tasks more effectively, leading to improved service delivery and maintenance outcomes.
Case Studies in Various Industries
Several industries exemplify the positive influence of work order maintenance software. For example, in the manufacturing sector, General Electric has integrated this software into its operations to monitor machine performance and schedule preventive maintenance. This approach minimizes downtime and extends the lifespan of equipment, thus reducing costs considerably.
In the healthcare sector, Vanderbilt University Medical Center utilizes work order maintenance software to manage its facilities and equipment maintenance. By using real-time data, the center can quickly address potential issues before they escalate. This proactive maintenance helps the hospital maintain a high level of service quality, directly impacting patient care.
Moreover, Walmart implements work order maintenance software for its retail operations. The system assists in managing store facilities and inventory, ensuring timely maintenance of equipment. By prioritizing work orders based on urgency and impact, Walmart reduces operational disruptions and enhances the shopping experience for customers.
Success Stories and Measurable Outcomes
The implementation of work order maintenance software often leads to quantifiable improvements. For instance, after deploying its maintenance software, Delta Airlines reported a 25% reduction in aircraft maintenance delays. This success can be attributed to better communication among teams and clearer scheduling of maintenance tasks.
Similarly, Coca-Cola has benefited significantly from its work order system, achieving a 30% decrease in maintenance operational costs. The software enables Coca-Cola to forecast maintenance needs based on historical data, making it simpler to plan and budget resources effectively.
"Work order maintenance software not only improves functionality but also transforms how teams collaborate and communicate, leading to significant long-term savings."
These cases show that the advantages of adopting work order maintenance software are tangible. Organizations across different sectors see reductions in downtime, cost efficiencies, and enhanced service delivery by carefully examining their unique needs and procedure. In today’s competitive landscape, leveraging such technology is not just beneficial but essential.
Ending
In concluding our exploration of work order maintenance software, it is essential to recognize the profound impact such tools have on operational efficiency and strategic decision-making in various industries. This software not only optimizes task management, but also strengthens communication across teams, elevates asset management, and ultimately drives productivity.
Importance of Key Elements
The significance of features, benefits, and challenges discussed in the earlier sections cannot be overstated. Key features such as work order creation, asset tracking, and reporting capabilities are integral in streamlining maintenance processes.
Benefits derived from these functionalities are equally vital. The software enhances efficiency by automating routine tasks, which allows staff to focus on more complex issues. Moreover, the cost reductions associated with minimized downtimes and efficient resource management present a strong case for its adoption.
Considerations for Implementation
When considering the implementation of work order maintenance software, organizations must also evaluate their specific needs. It is not merely about acquiring the latest software but understanding how it aligns with existing systems and workflows. Proper training and change management strategies are crucial to ensure smooth transitions and user acceptance.
Additionally, organizations should be aware of the ongoing evolution in this field. As new technologies emerge, such as artificial intelligence and predictive analytics, decision-makers must remain adaptable, continuously assessing the software’s ability to meet changing demands.
The Bigger Picture
Ultimately, this article serves as a comprehensive guide for technology-focused leaders. By embracing work order maintenance software, organizations can position themselves to better address both current operational challenges and future demands. Not only does it reflect an investment in efficiency, but it also signifies a commitment to adapting in a fast-paced, technology-driven world.
"In the realm of business, effective tools are not just nice-to-haves but necessities that pave the way for sustained success."